Mountain Bike Dropouts
As the lead for the components team in our bike building club, I thought a good project for the team to take on was to make dropouts for the club's full-suspension mountain bike project. My partner worked on the design through the lens of his bike knowledge and I helped design them through the lens of manufacturing and I did all the machining for this project.
We wanted the dropouts to work with SRAM's Universal Derailleur Hanger (UDH), a modern derailleur hanger that is quickly becoming a standard for most frame designs. Thus, understanding the documentation on the UDH was vital.
Below are some of the drawings and details about the UDH that we need to make sure the dropouts were machined to the proper dimensions and tolerances.
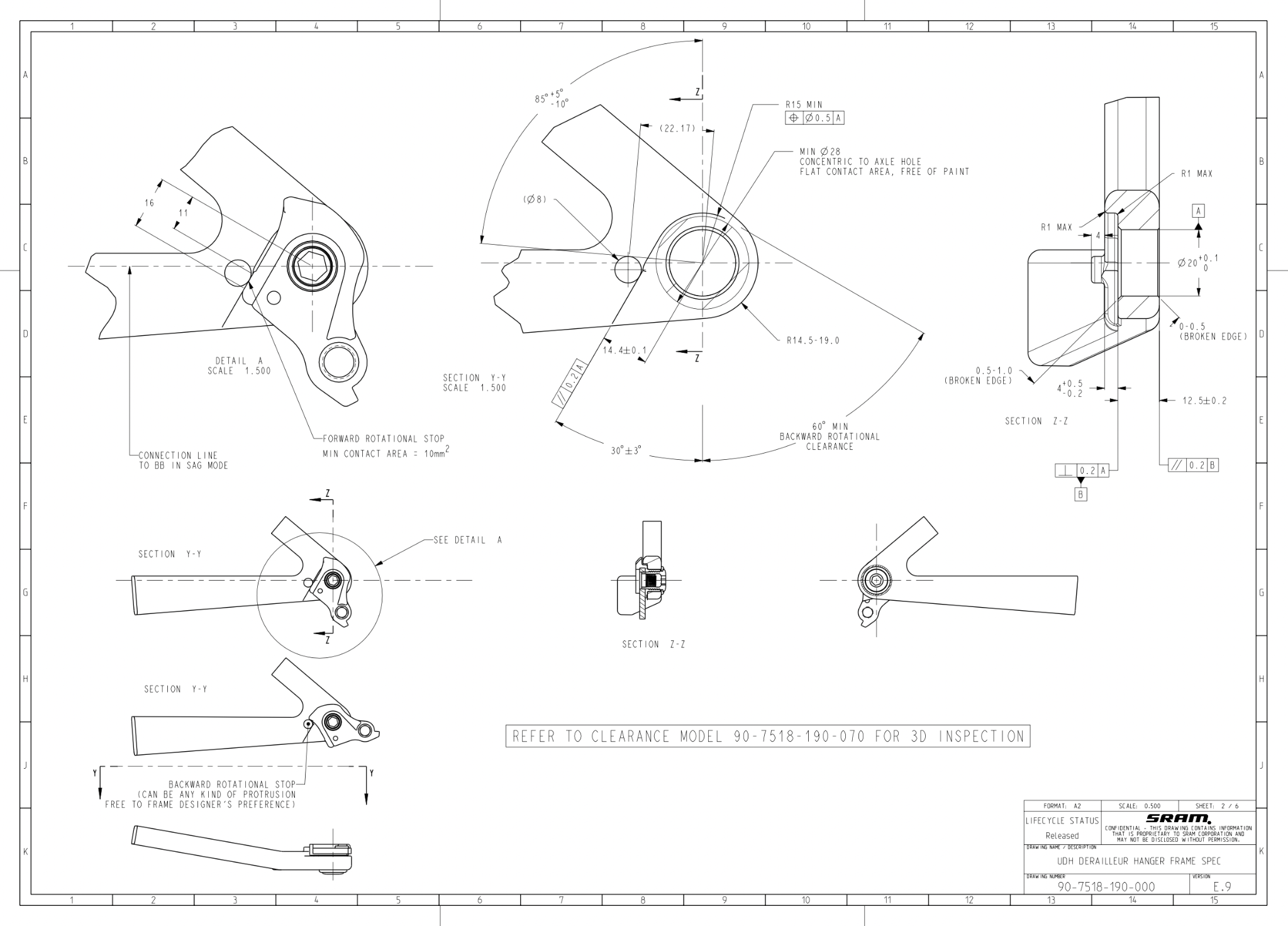
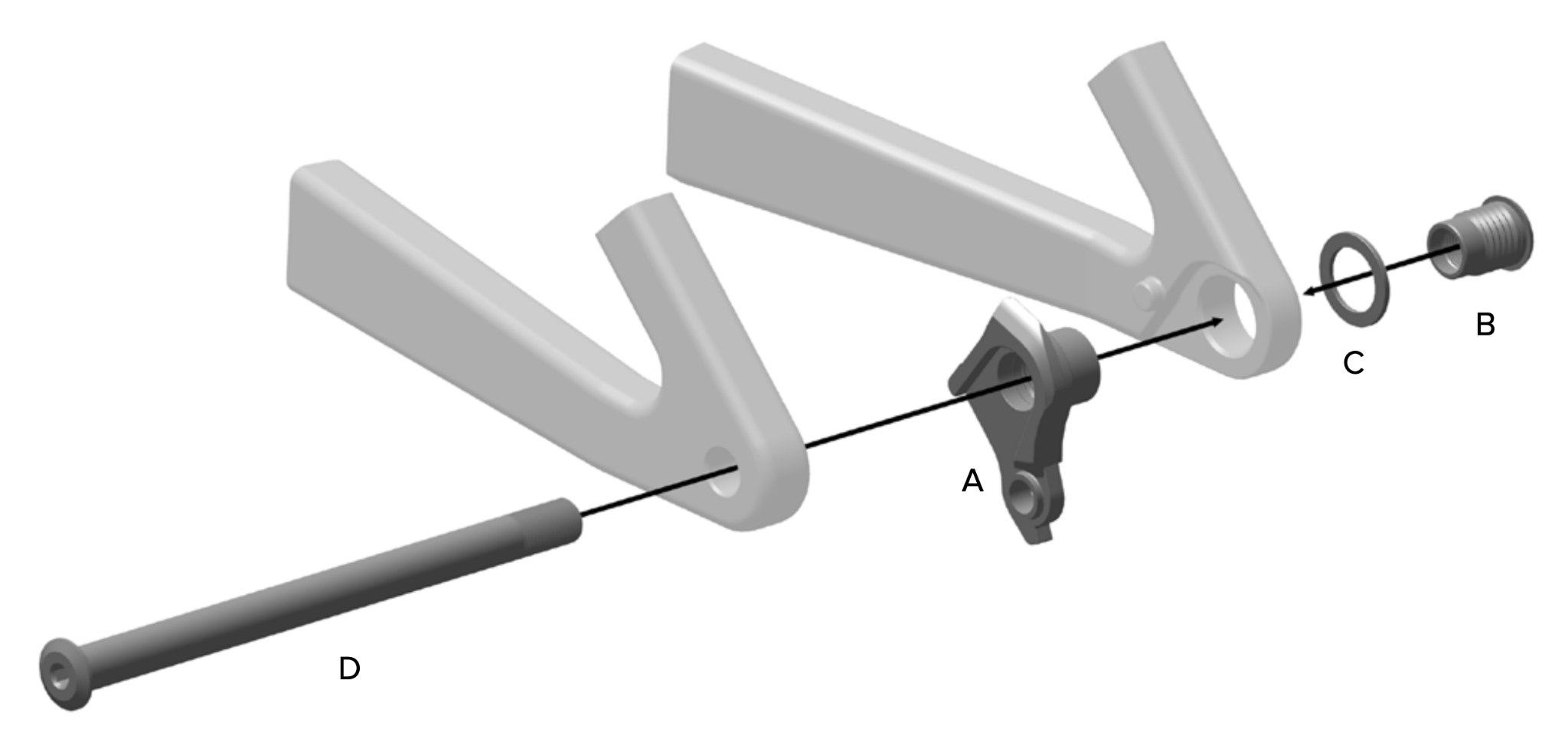
We decided to use low-carbon steel for ease of being welded to the chromium steel alloy used for the connecting rods. We designed the dropouts to be first waterjet cut and then milled to add the precise features needed. The waterjet operation removes a lot of weight and unnecessary machining time, in addition to allowing us to have some creative freedom in the design.
Each dropout is different in design: one interfaces with the UDH (drive side) and the other interfaces with the brake caliper (non-drive Side).
Drive
Side Dropout
has
UDH feature
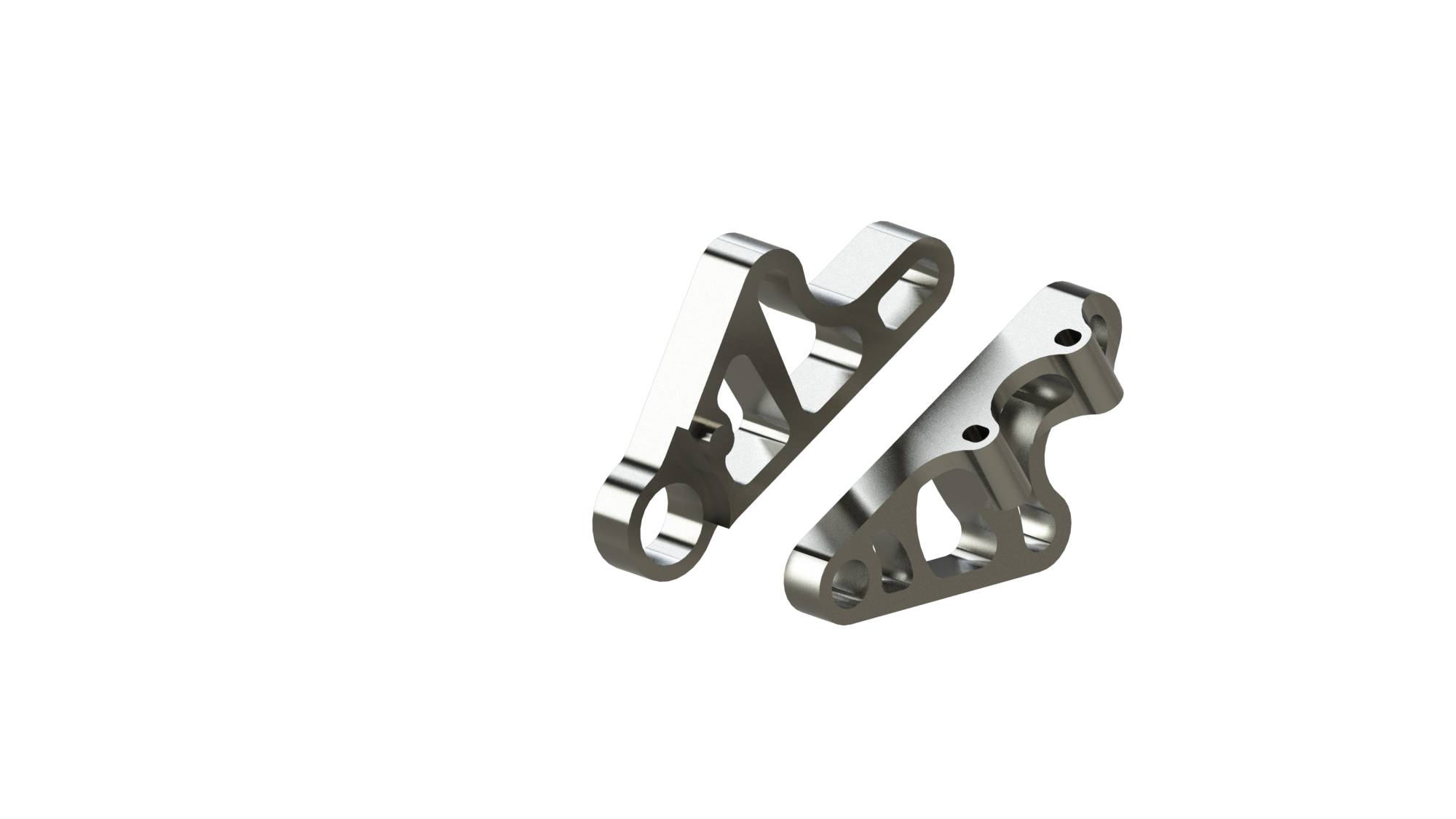
Non-Drive
Side
with
brake caliper mount
The machining process involved is essentially the same for both. However, the non-drive side dropout needed machining in an extra dimension and needed some patient hand filing to clean up. My favorite part of this machining process was using geometry measurements in CAD to make special fixtures to line up the usual waterjet cut geometry exactly how I needed it. Flip through the image slides to see the machining process for each dropout.
Drive Side Dropout
Non-Drive Side Dropout
Here are the dropouts assembled with the out-sourced parts and welded on to the frame of the bike.
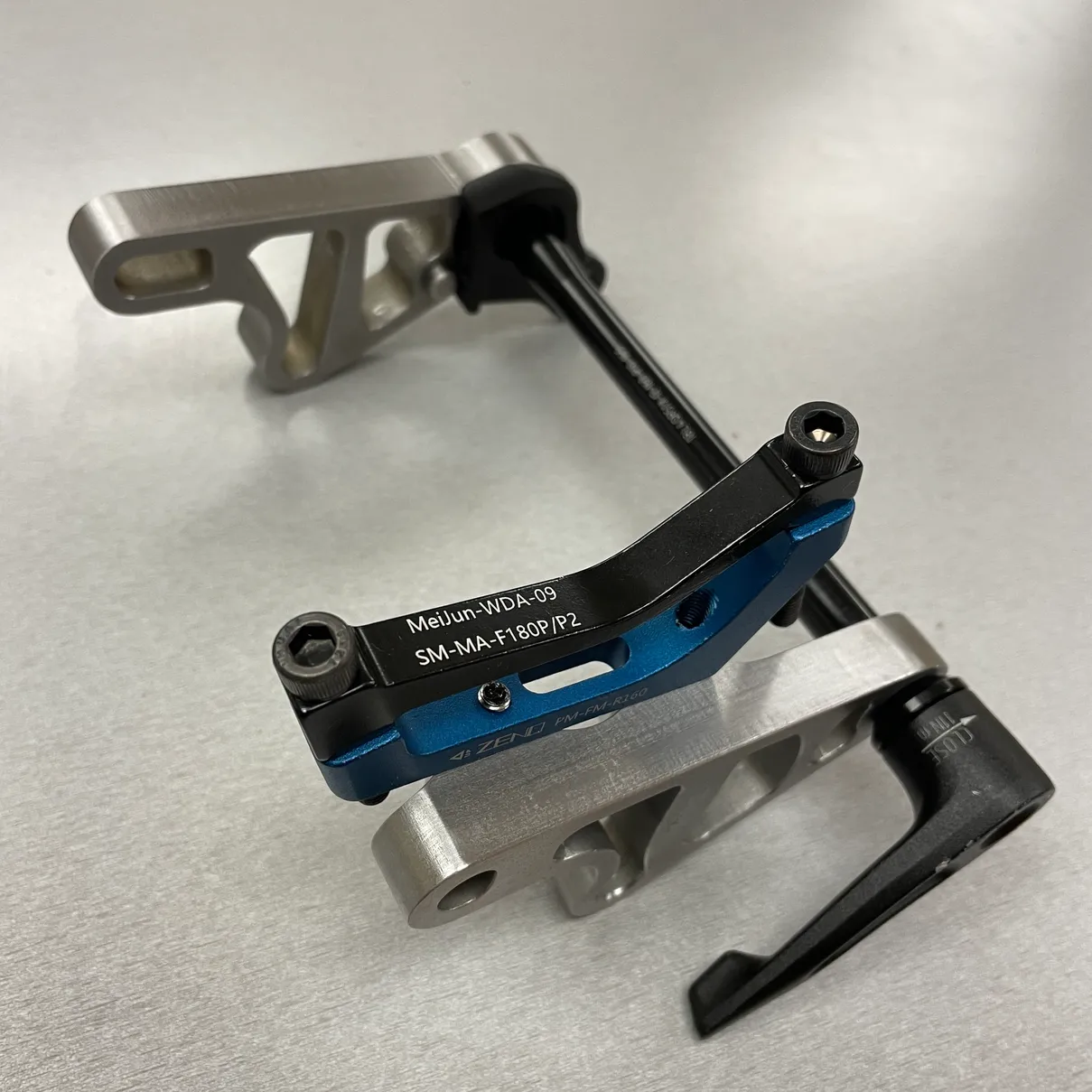
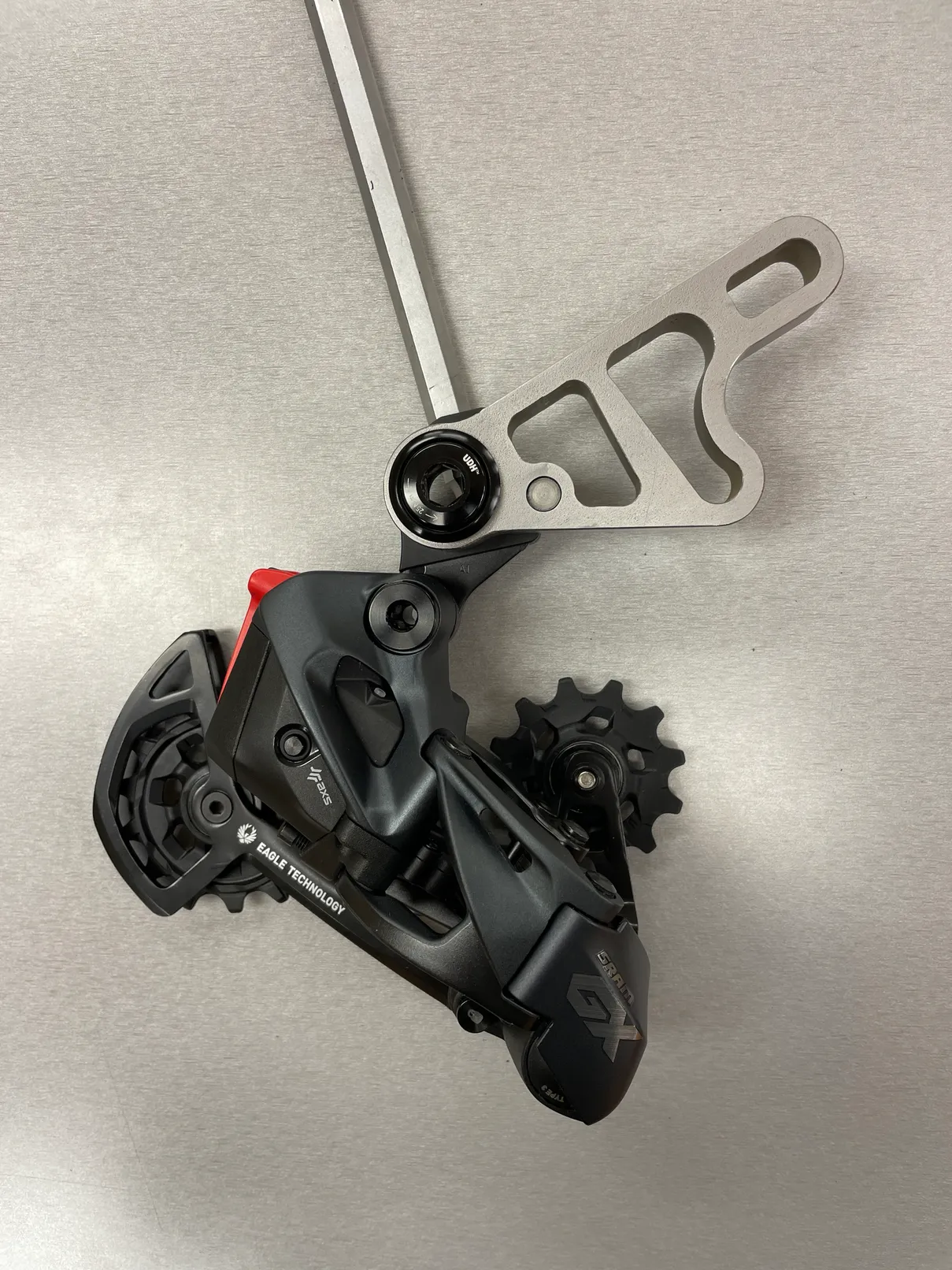
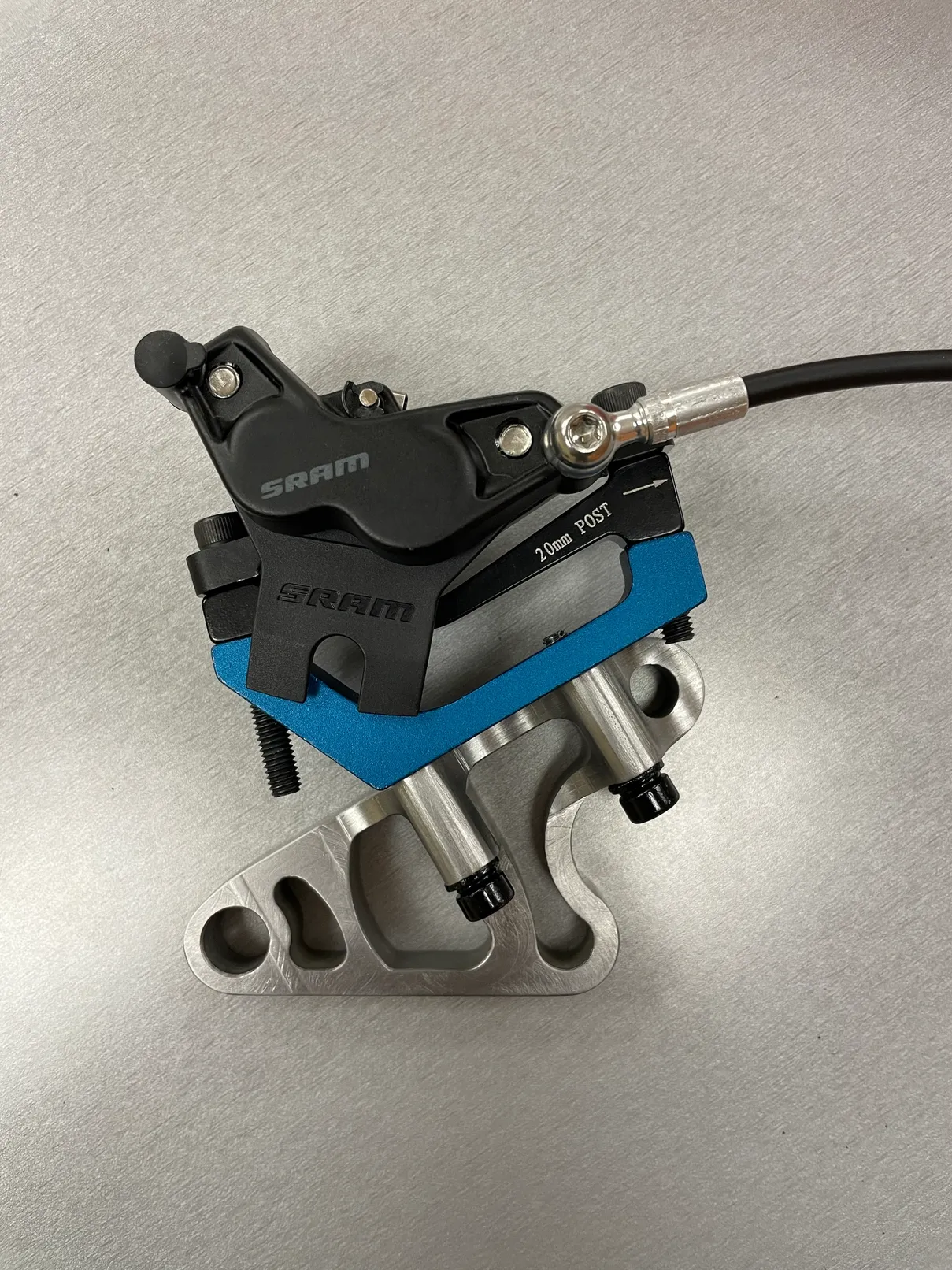
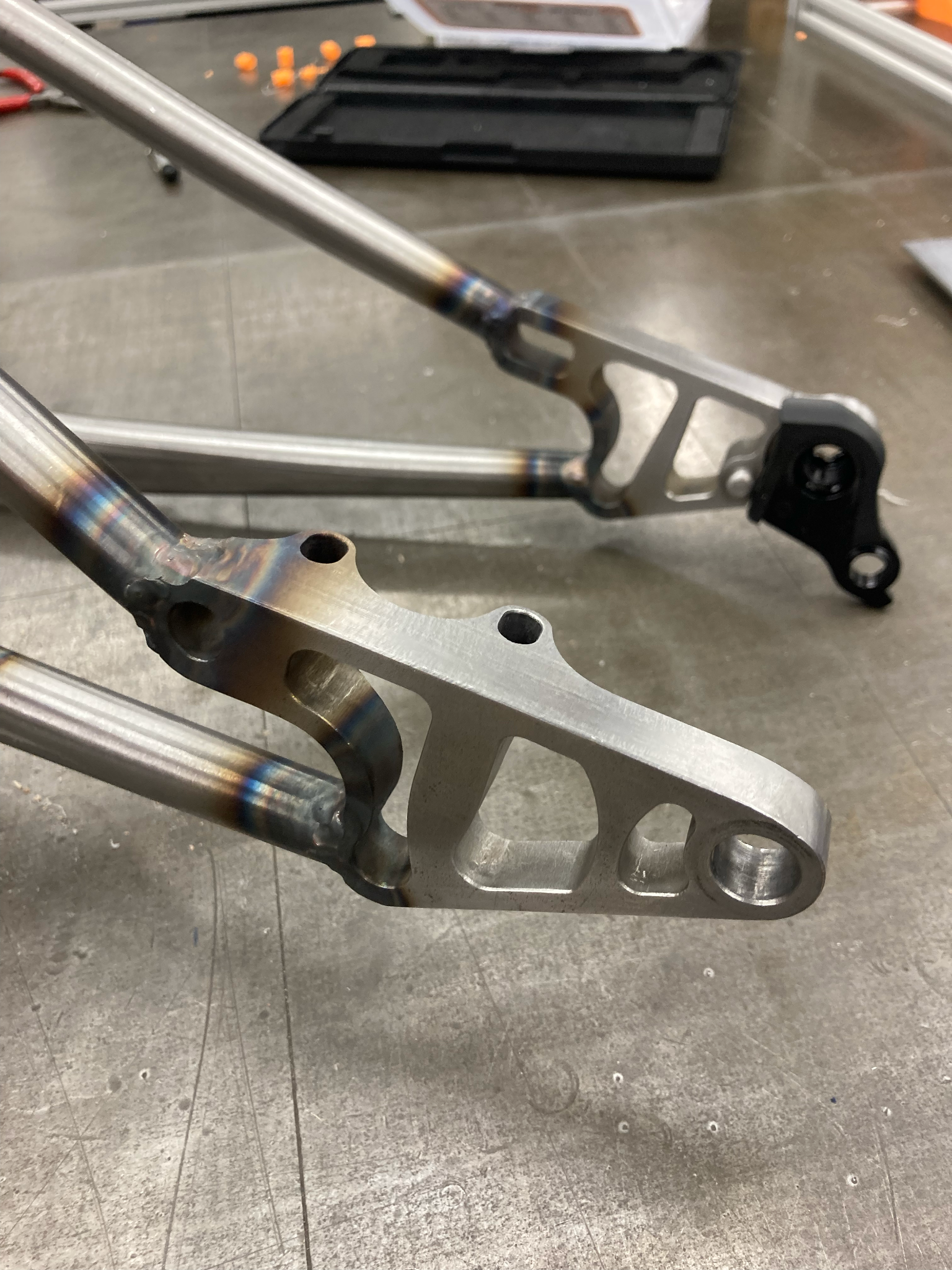
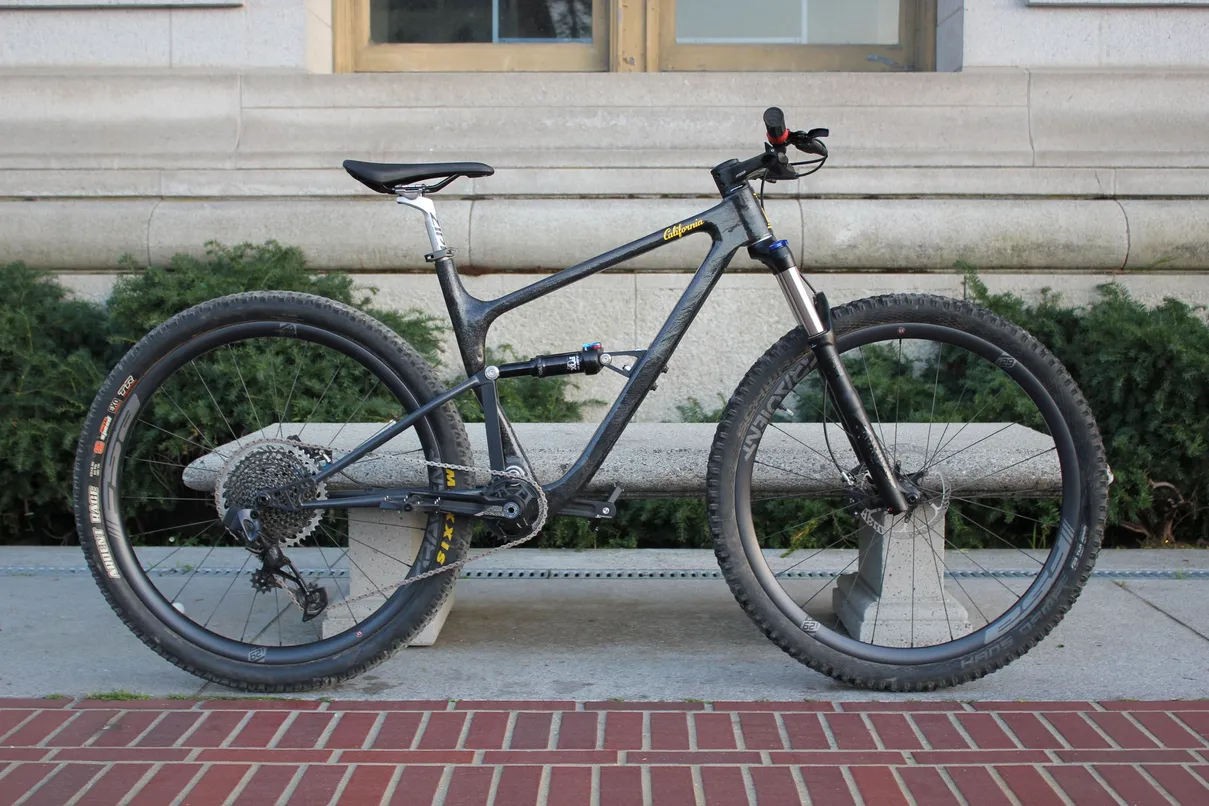