Star-Targeting and Tracking Telescope Mount
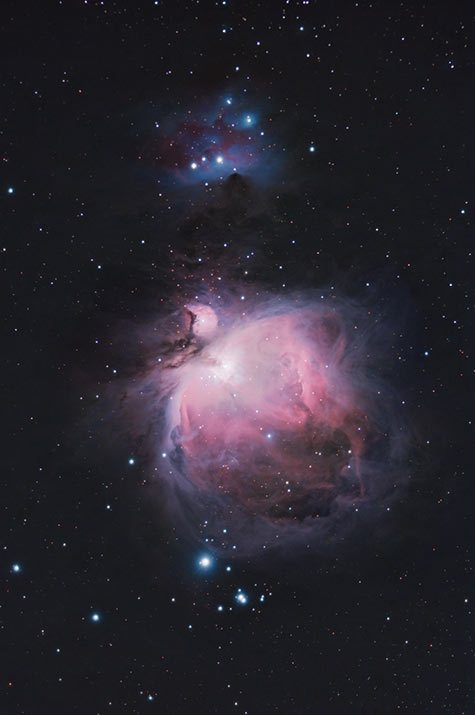
Long Exposure Photo of the Orion Nebula [1] (not our photo)
The Problem: How do you shoot high-quality images of deep sky objects on a budget?
Astrophotography is an expensive hobby if one wants to achieve high-quality photos of deep sky objects (DSOs) such as the picture of the Orion Nebula on the left. To achieve a photo like this, the photographer must:
be in an area with very little light pollution
have a telescope or long-range zoom lens
take photos with a very long exposure
needs to remain locked onto the object as it moves along with the Earth's rotation
Our Solution: ASTRID
ASTRID (Automated Star Tracking Robot with Inferred Direction) is a telescope mount that will both:
Autonomously target any visible DSO such as a star, planet, or galaxy
Remain locked on that object throughout the night (accounting for the object’s motion and the rotation of the earth)
ASTRID utilizes a mounted camera to capture an image of the stars, uses this image in a computer vision algorithm against an existing database to determine the current viewing direction, and then slews to the correct viewing direction for a desired DSO. After reaching the desired position, ASTRID revolves at a rate of once per day to counteract the Earth’s rotation, keeping the object in view. While locked onto the target, our iPhone which is mounted on the eyepiece of the telescope can now take high-quality long-exposure photos of the DSO.
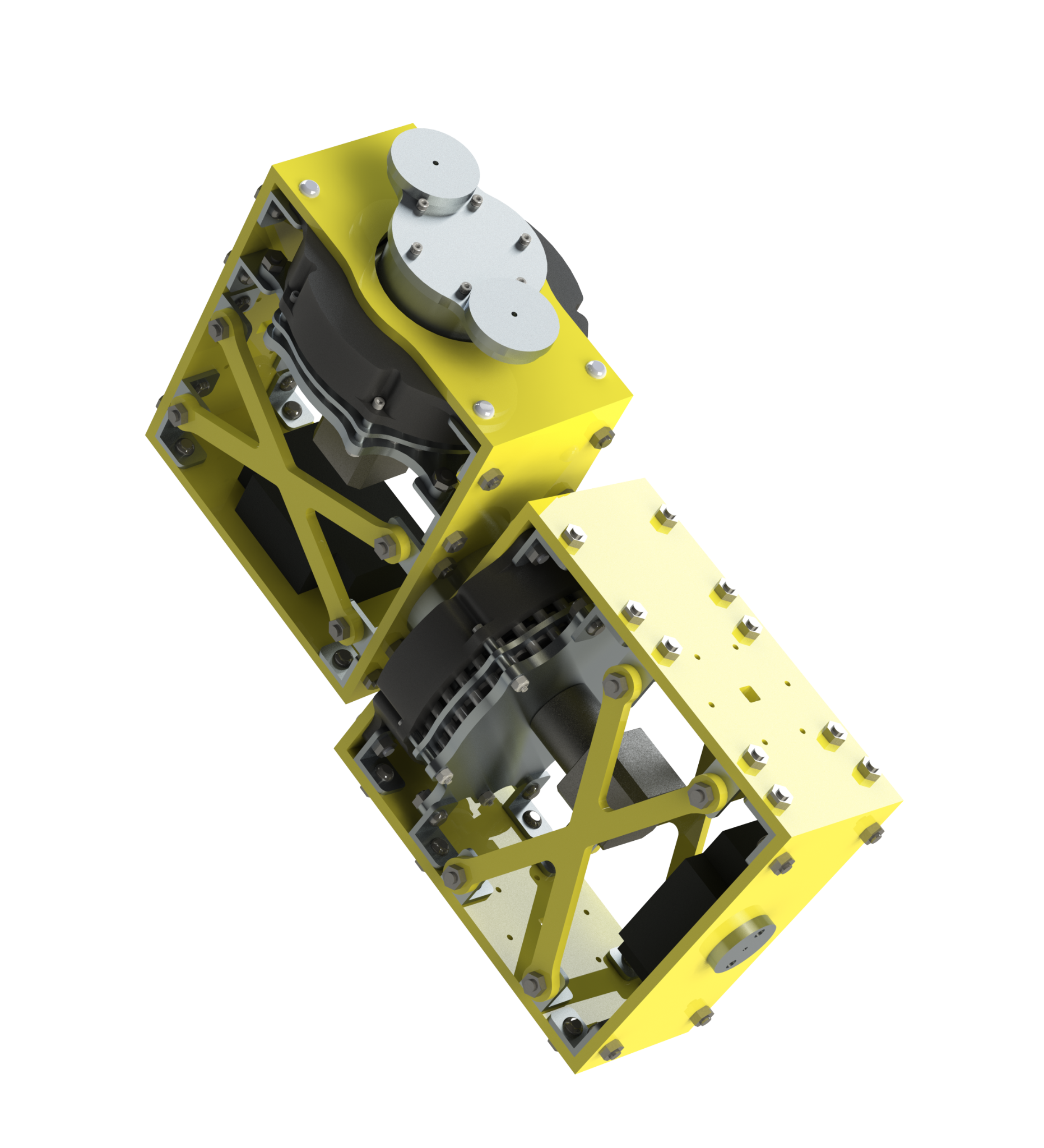
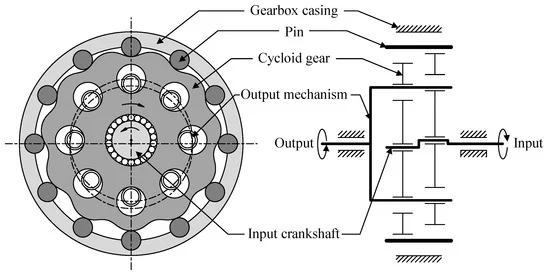
Diagram of a typical cycloidal drive [2]
Cycloidal Drives
This application will benefit from a gearbox with low backlash is essential to prevent issues during direction changes or weight shifts. Options like planetary gearboxes, harmonic drives, and cycloidal drives offer minimal backlash. For each of these options, acquiring well-designed 30:1 gearboxes from manufacturers is cost-prohibitive, especially since two are required. Therefore, opting to design and fabricate them is a more cost-effective solution and a great learning experience. A cycloidal drive, which uses circular rolling pins and a gear with a smooth spline instead of teeth, is particularly suitable for CNC milling due to its lack of sharp internal corners. Ultimately, a cycloidal drive stands out as a low-backlash gearbox that can be efficiently fabricated in a standard machine shop. A diagram showing the typical design of a cycloidal drive is shown on the left.
My role on this team was to design the cycloidal drives and fabricate the entire build. I spent about a month researching and designing the cycloidal drives and less than two weeks to fabricate both of the gearboxes and the rest of the telescope mount. The cycloidal drive is a more recently established gearbox relative to the harmonic drive and planetary gearbox, thus obtaining knowledge through academic papers and YouTube videos was difficult but very rewarding.
I had to design these drives with three things in mind: cost, surface interactions, and manufacturability. As I dove into the research, I noticed that cycloidal drives highly depended on ball bearings and that became the first design priority from a cost perspective. I also noticed that looking into low-wear and low-friction materials could be a more compact and cost-effective approach to some of the design elements. Lastly, I had to ensure that all parts could be made from the tools I had access to in the student machine shop.
Below is an exploded view of the final CAD model for the cycloidal drive I designed.
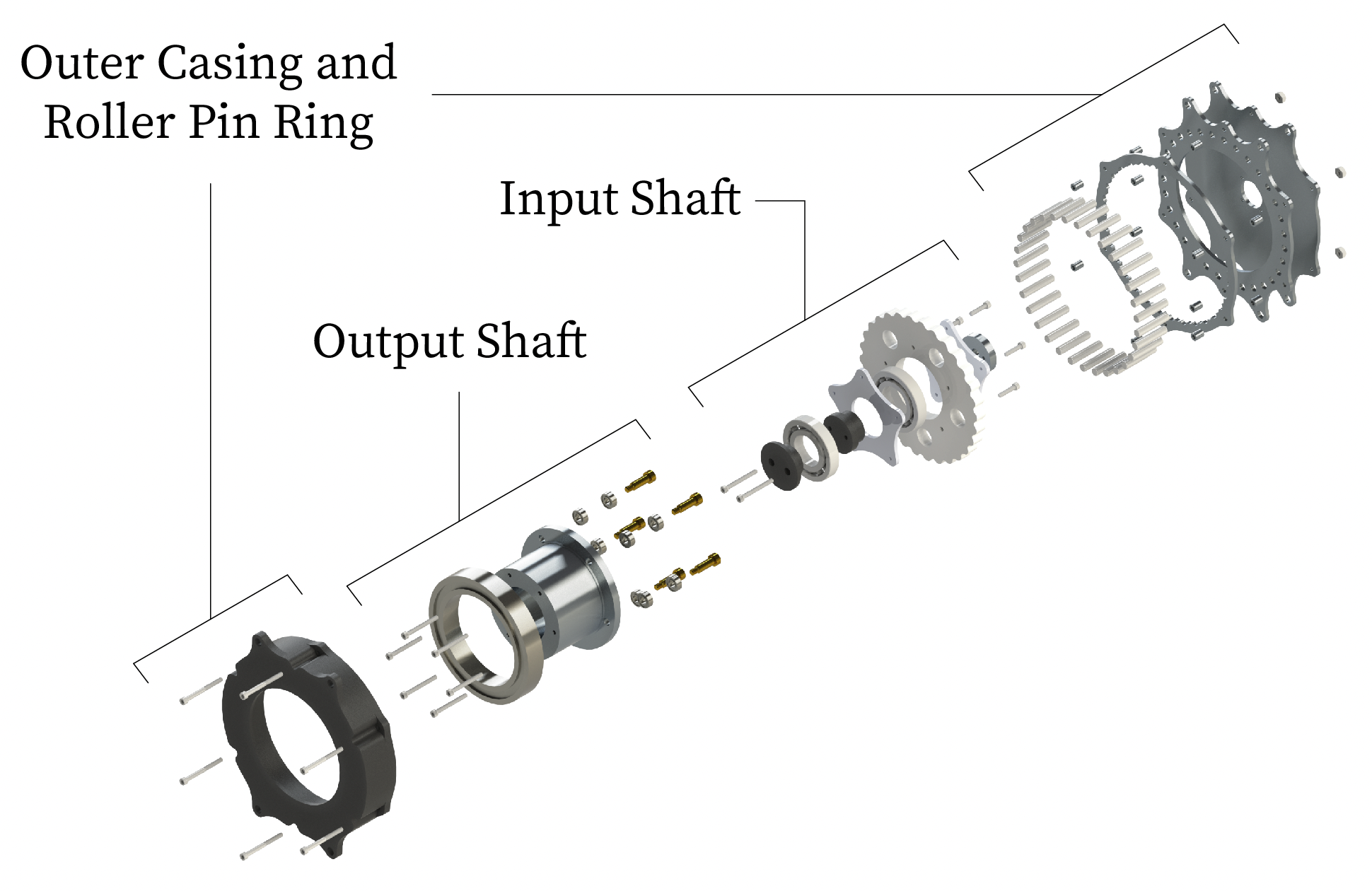
One half of the outer casing and roller pin ring is a large 3D-printed part and the other half is made from waterjet-cut aluminum sheets layered with spacers. These parts come together to retain the roller pins in a circle. The 3D-printed part had to be 3D printed to rapidly and reliably produce the large bearing press fit for the bearing on the output shaft. The other half was made from waterjet parts to avoid the cost that came with the high-quality 3D printer used in the shop.
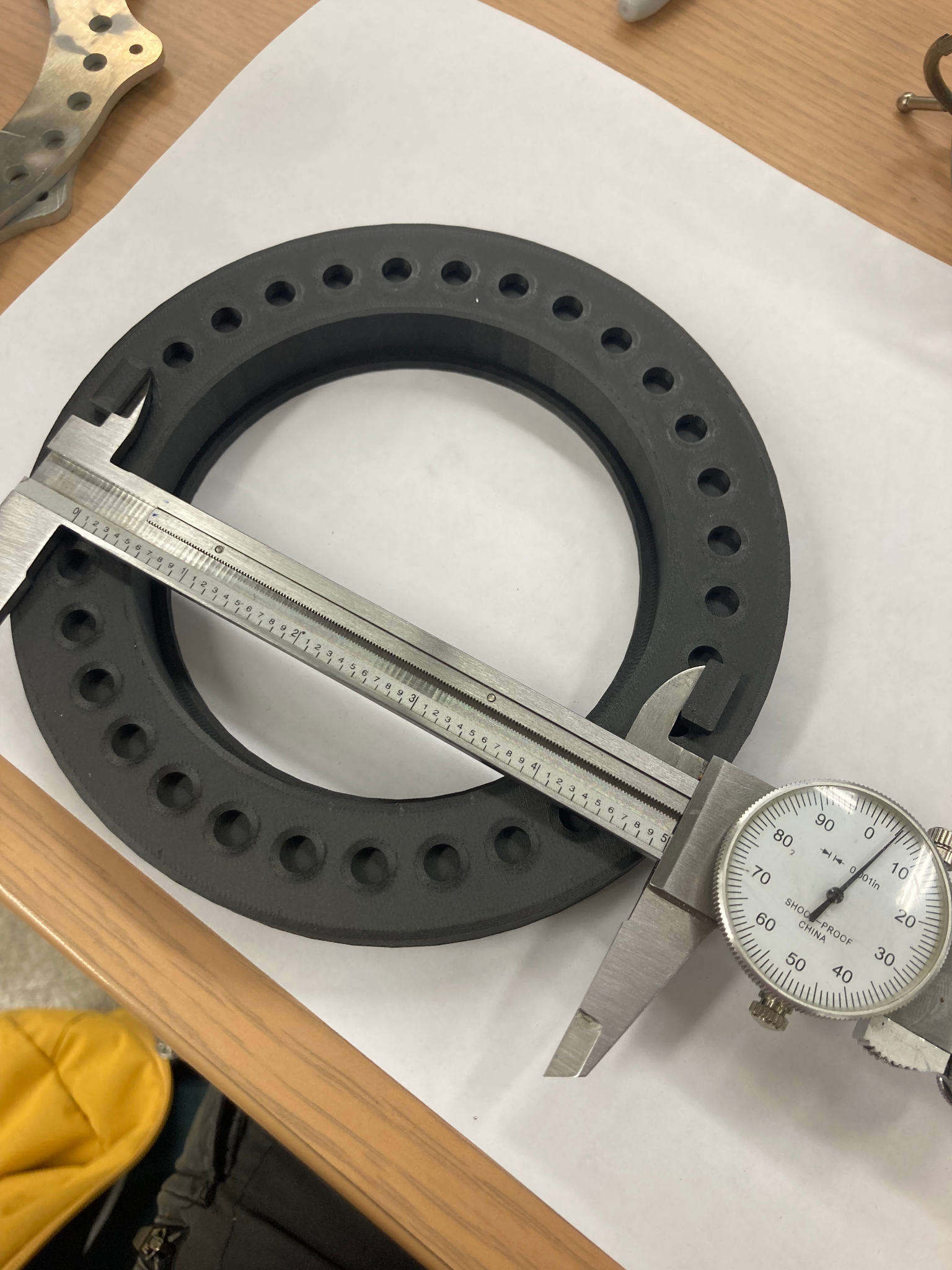
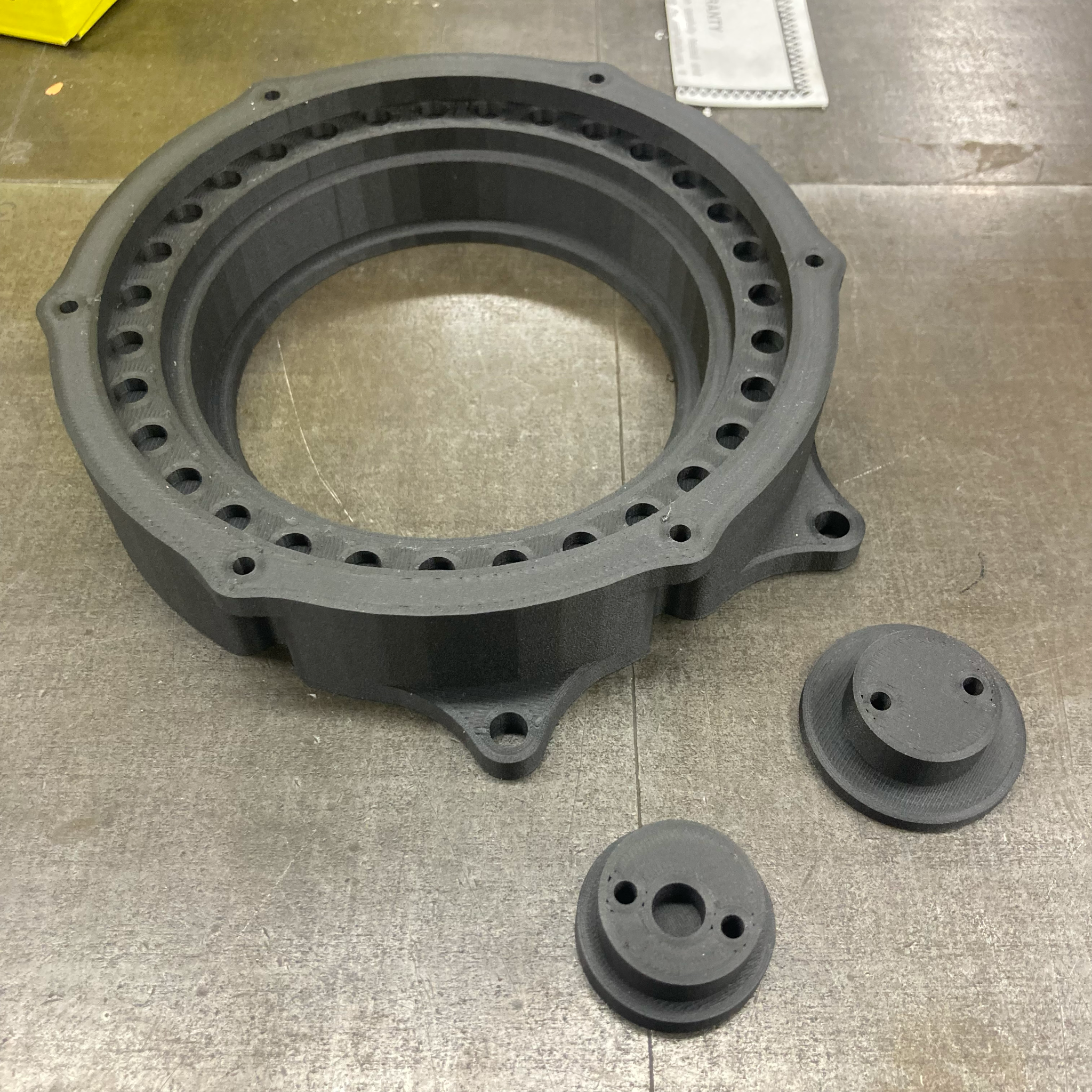
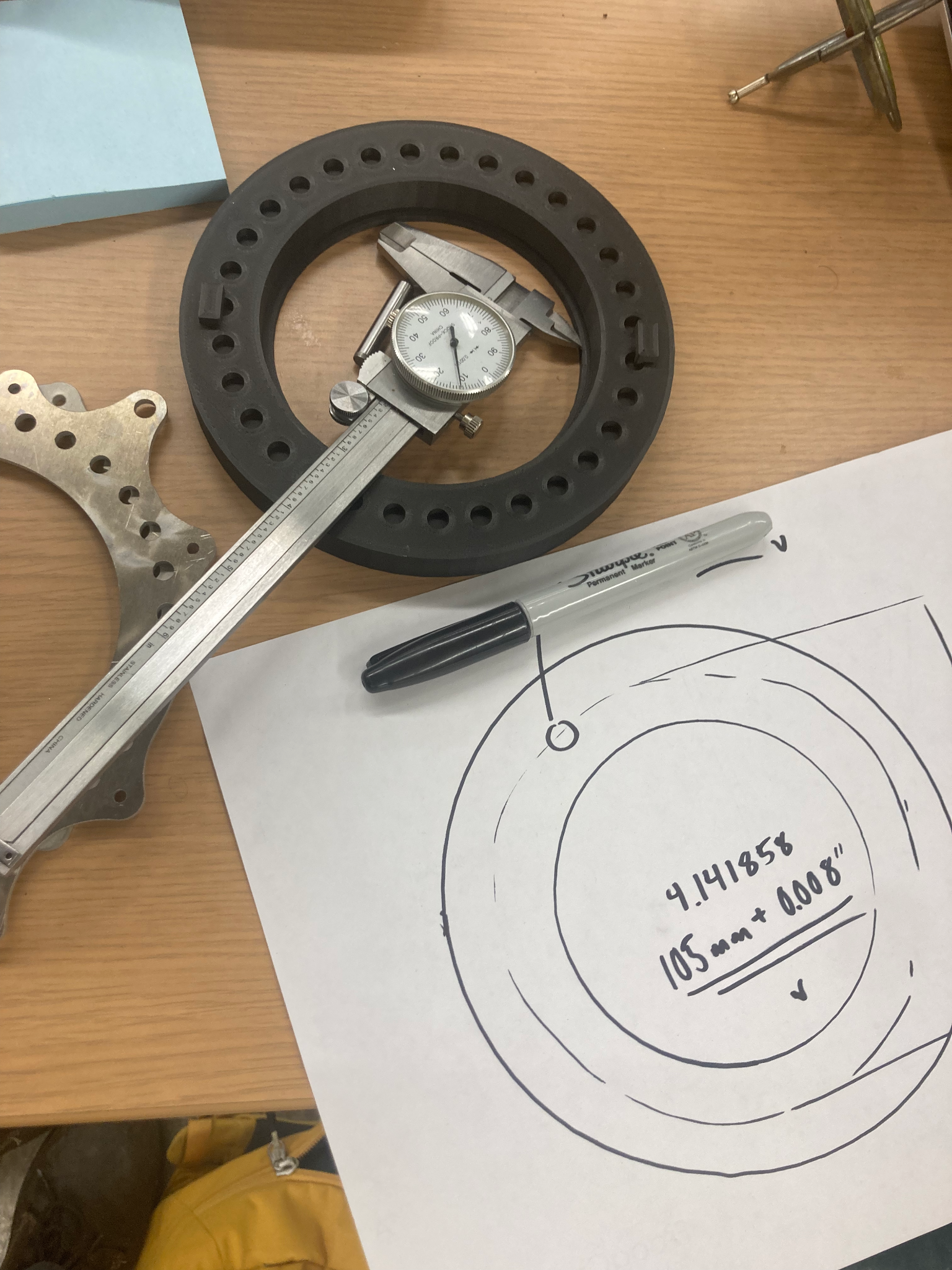

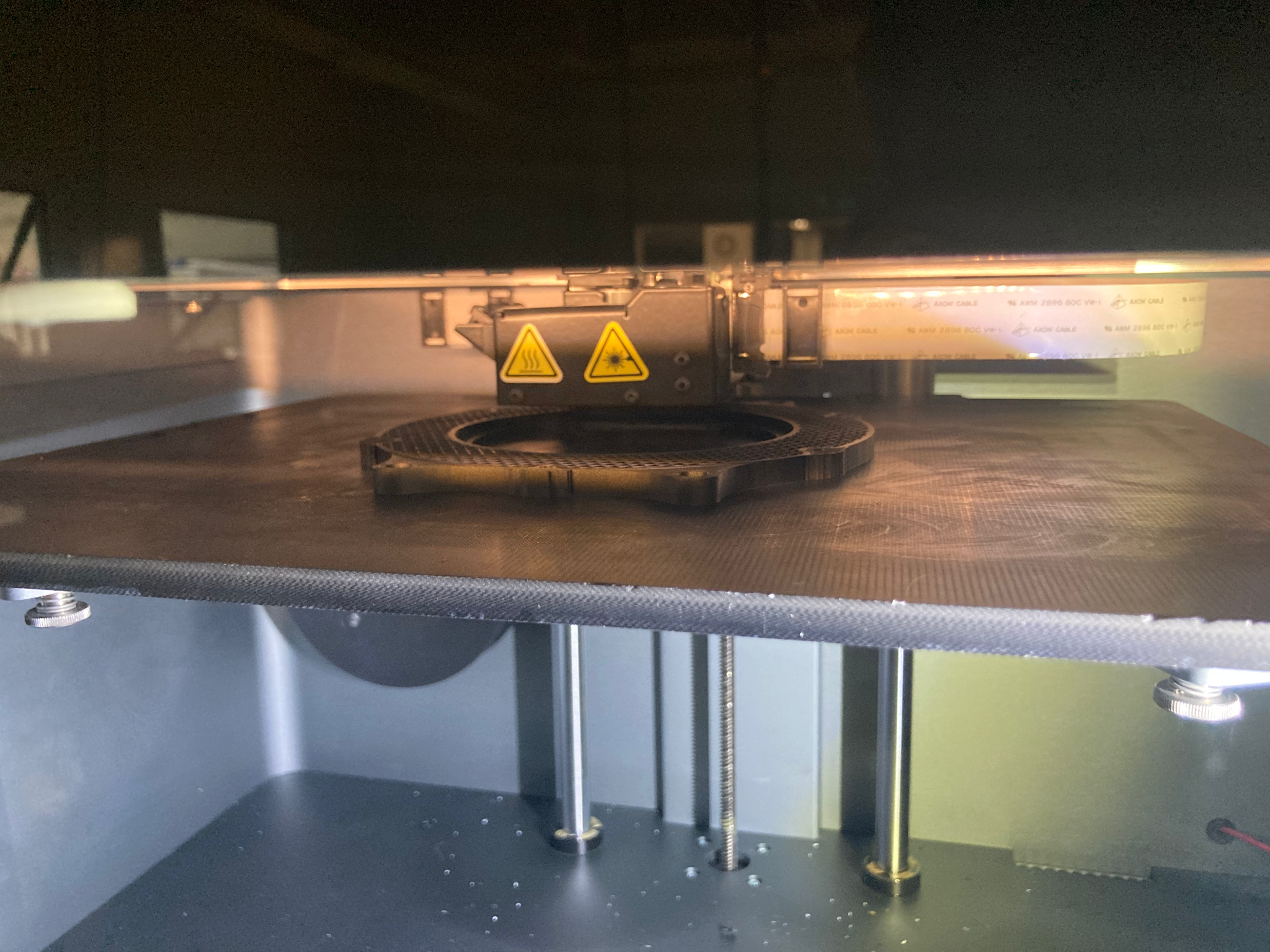
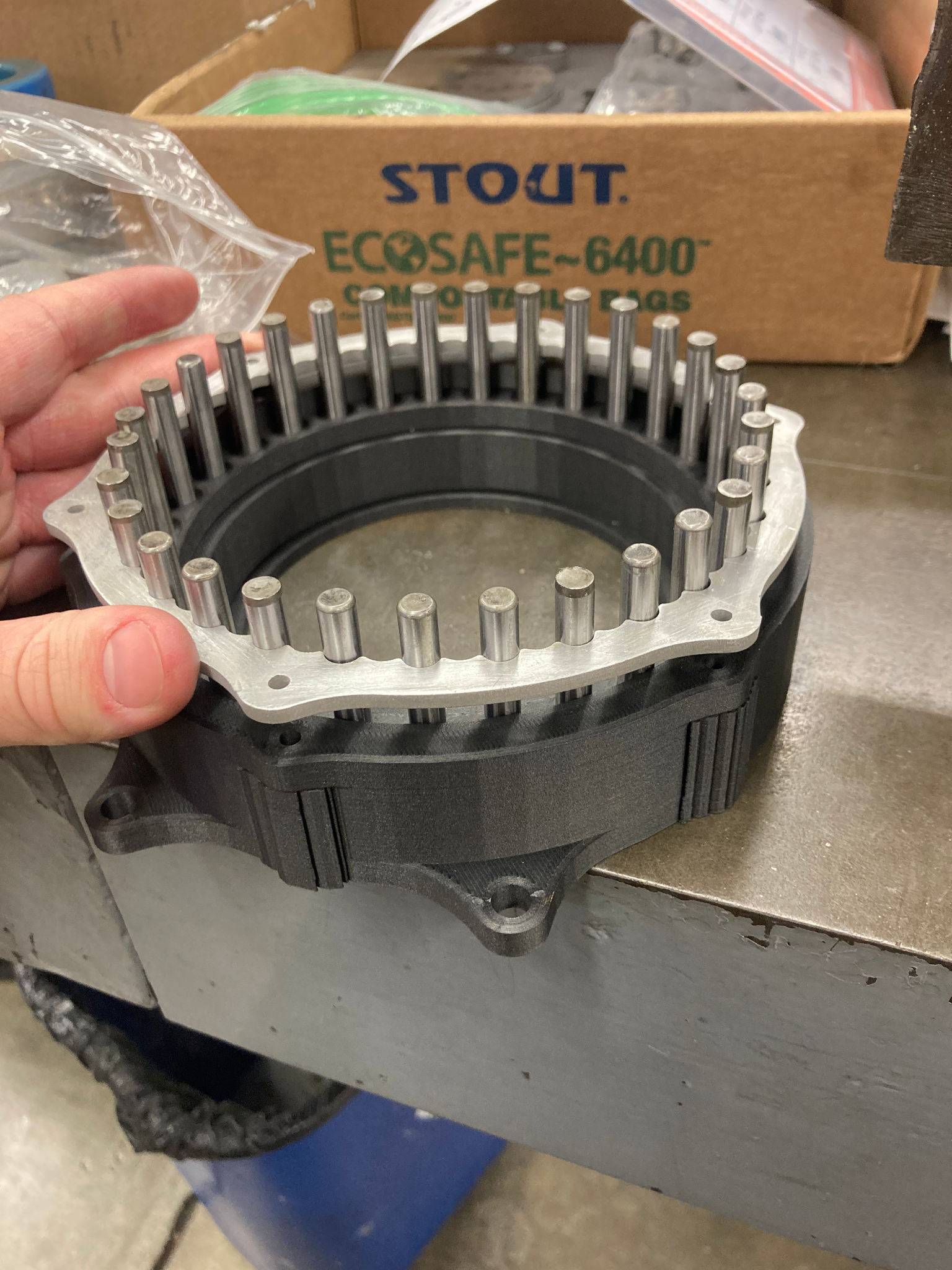
The output shaft is comprised of a large bearing, a large machined aluminum shaft, shoulder bolts, small bearings, and mounting bolts. The output shaft needed to be strong to reliably hold the cantilever-loaded shoulder bolts and have low runout, thus I chose to machine it out of aluminum. I machined the aluminum shaft to have a one-thousandth interference fit with the bearing. Because it was a large enough part, I was able to throw the shafts in the freezer for about an hour and the bearings easily fell right into place with no pressing needed.
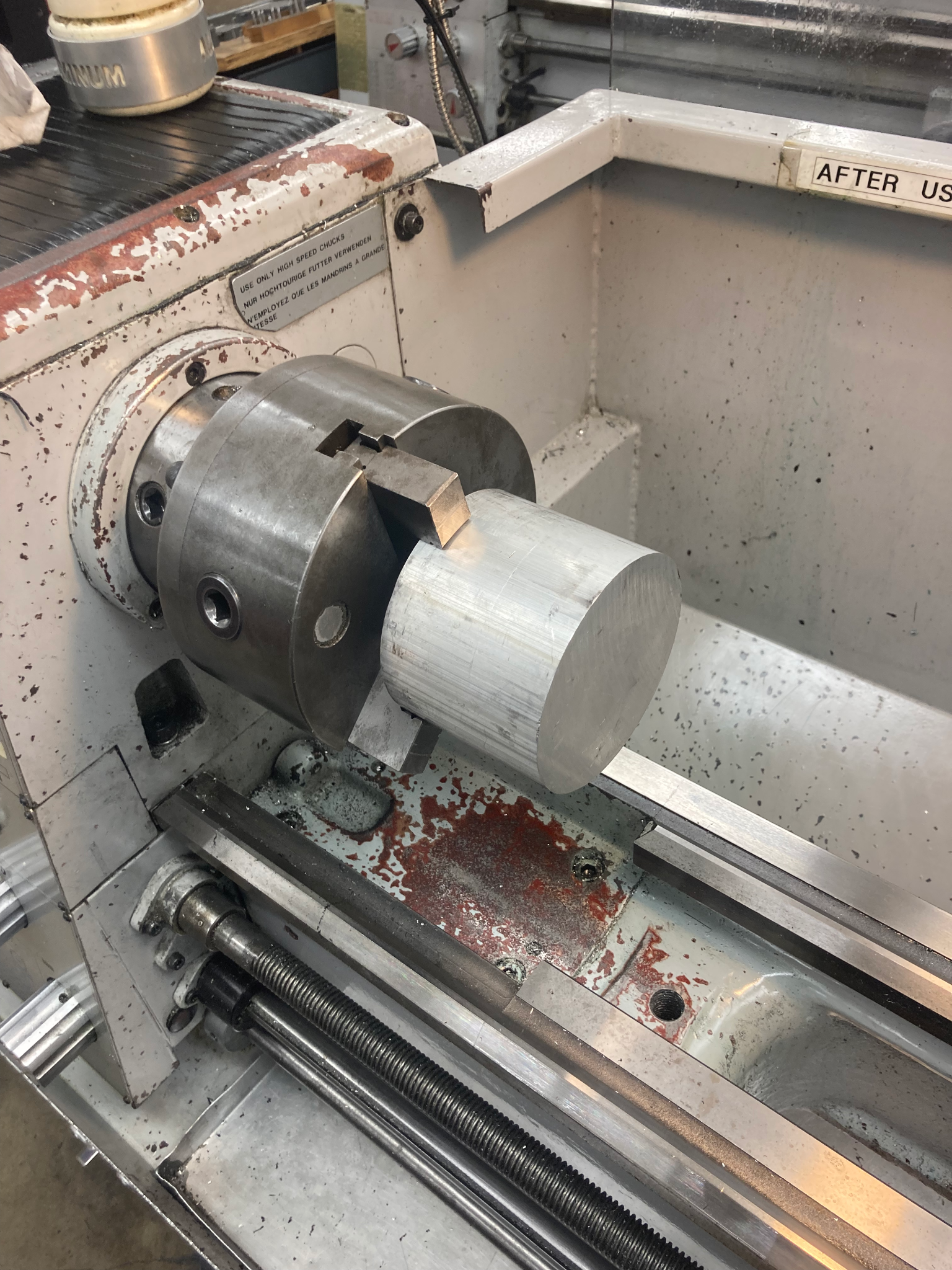
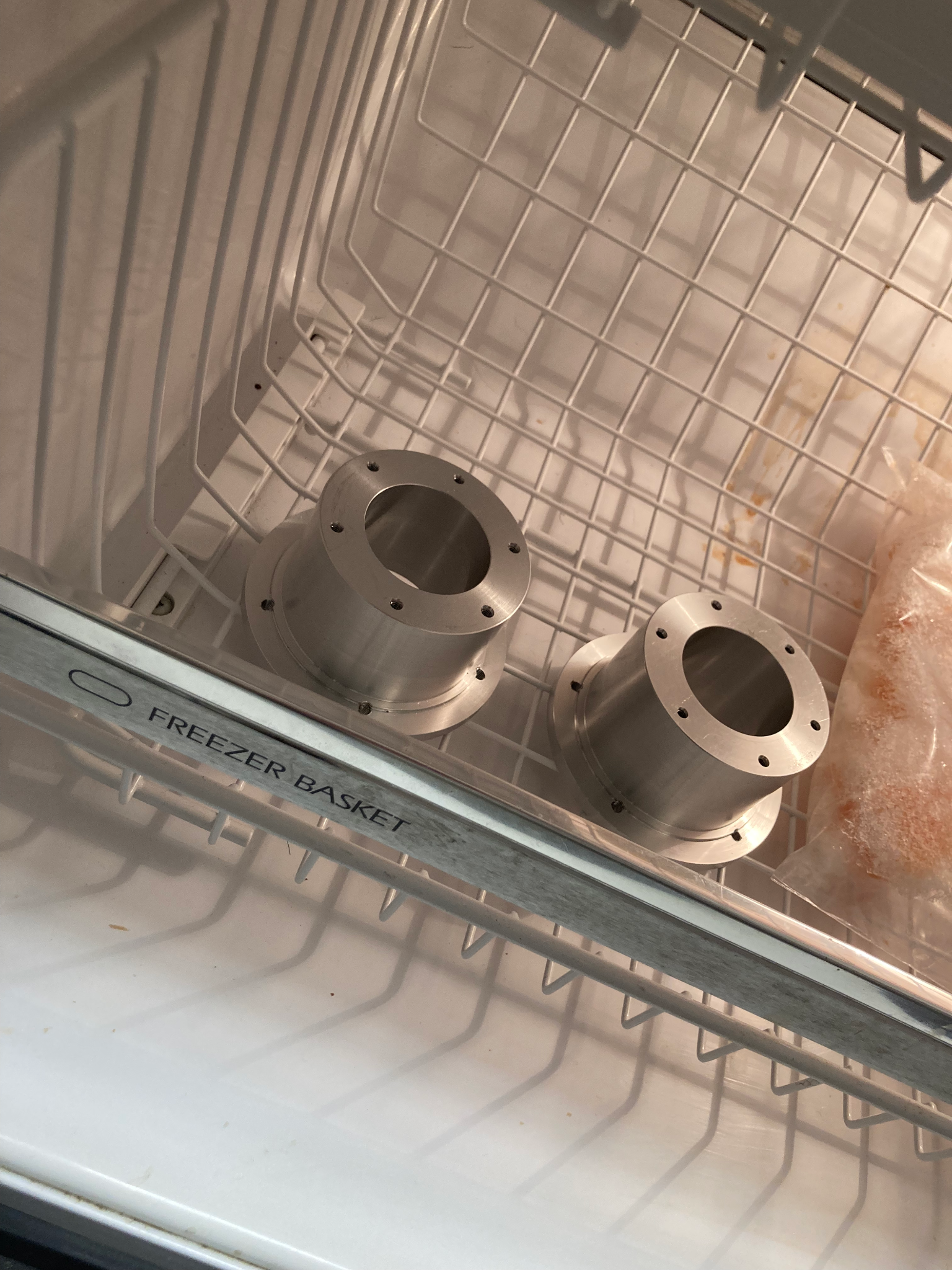
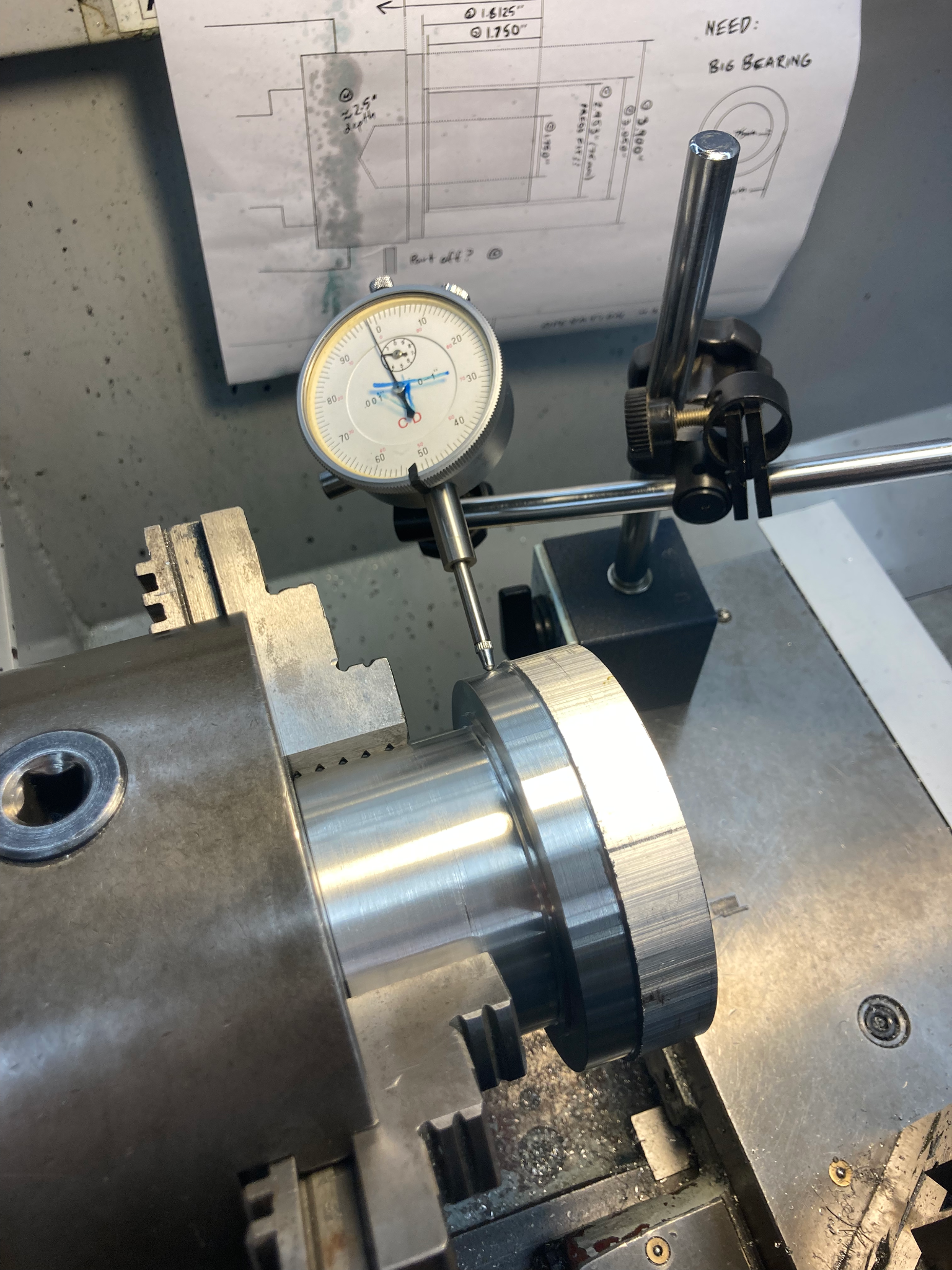
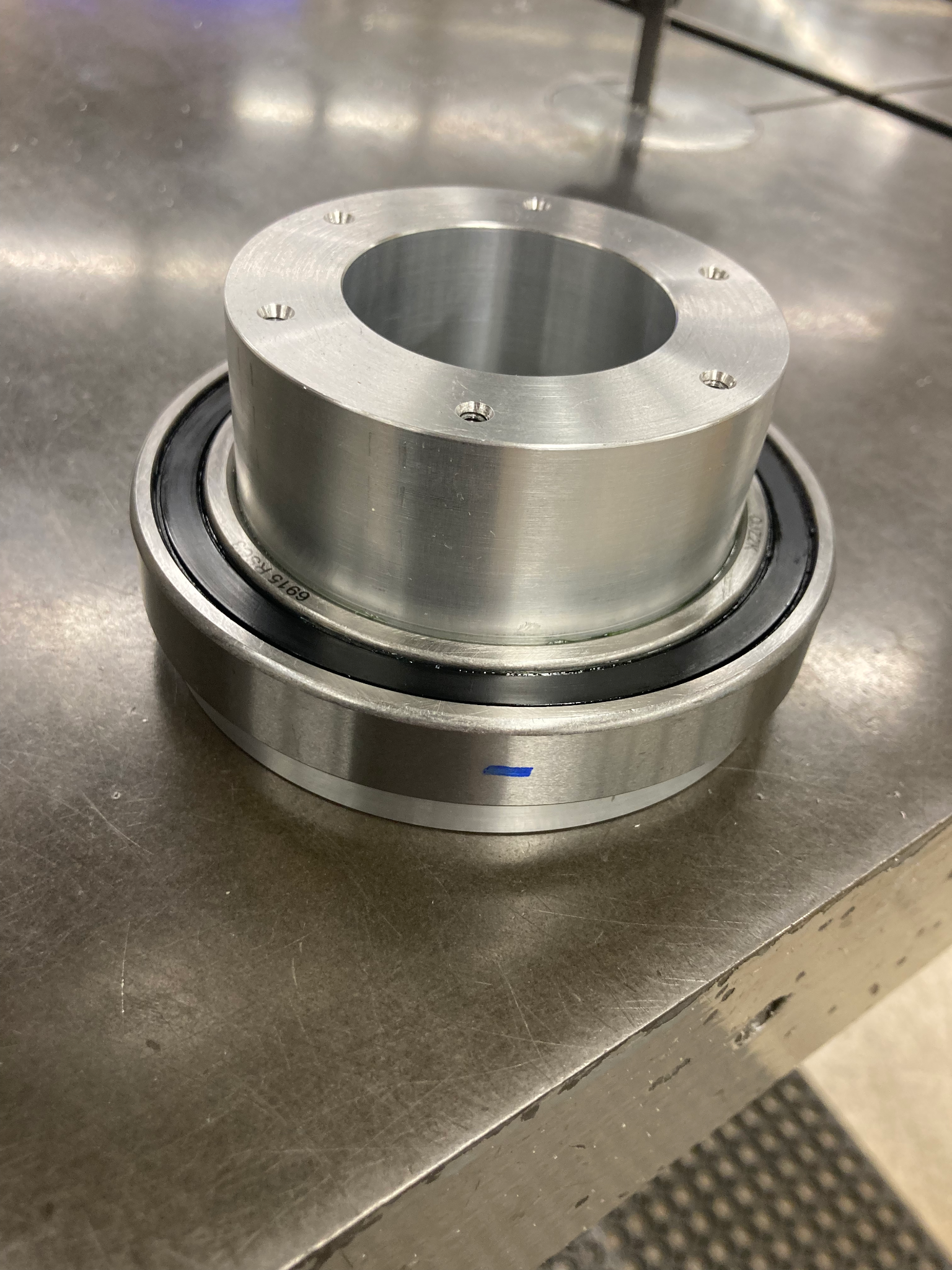
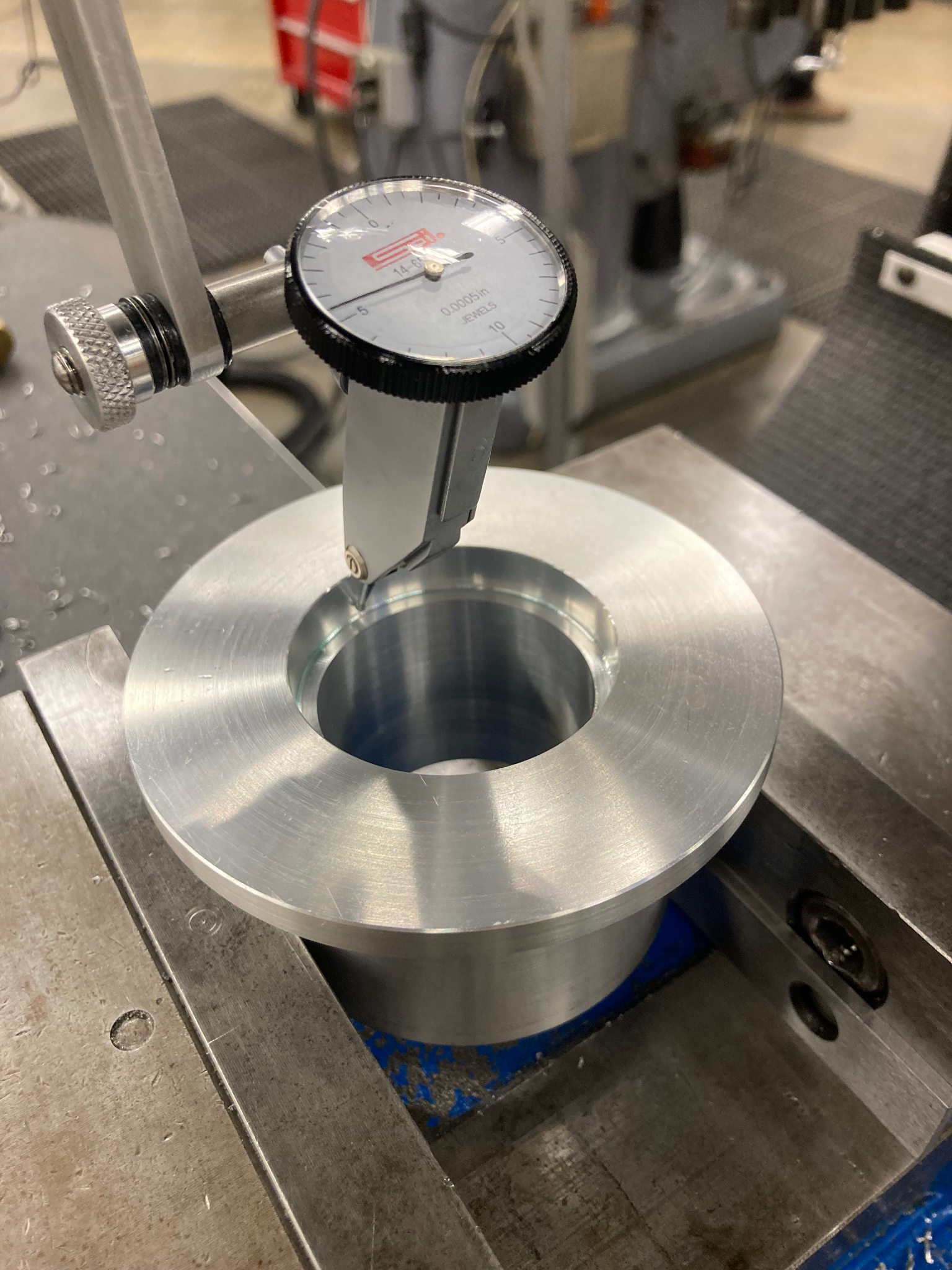
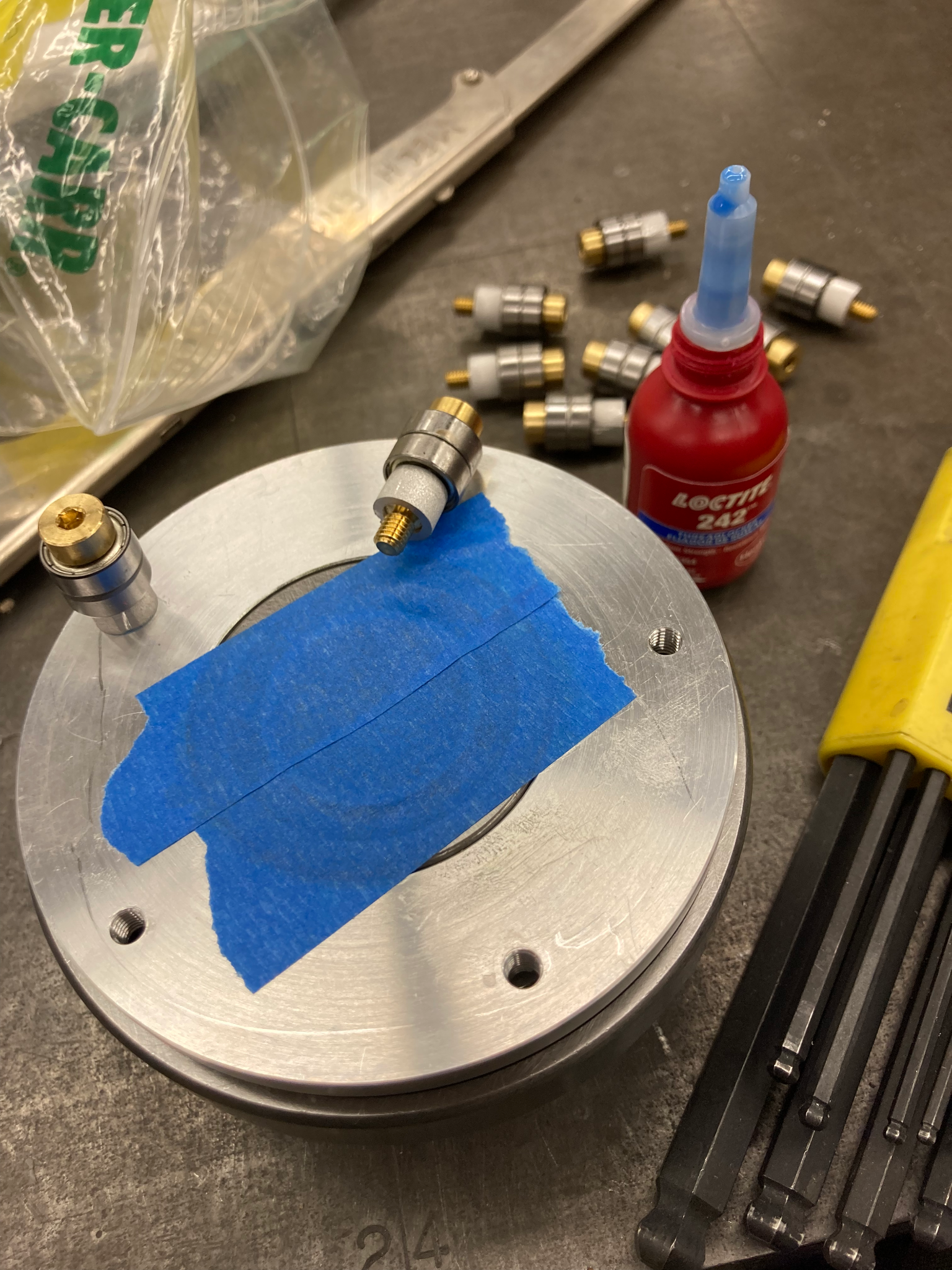
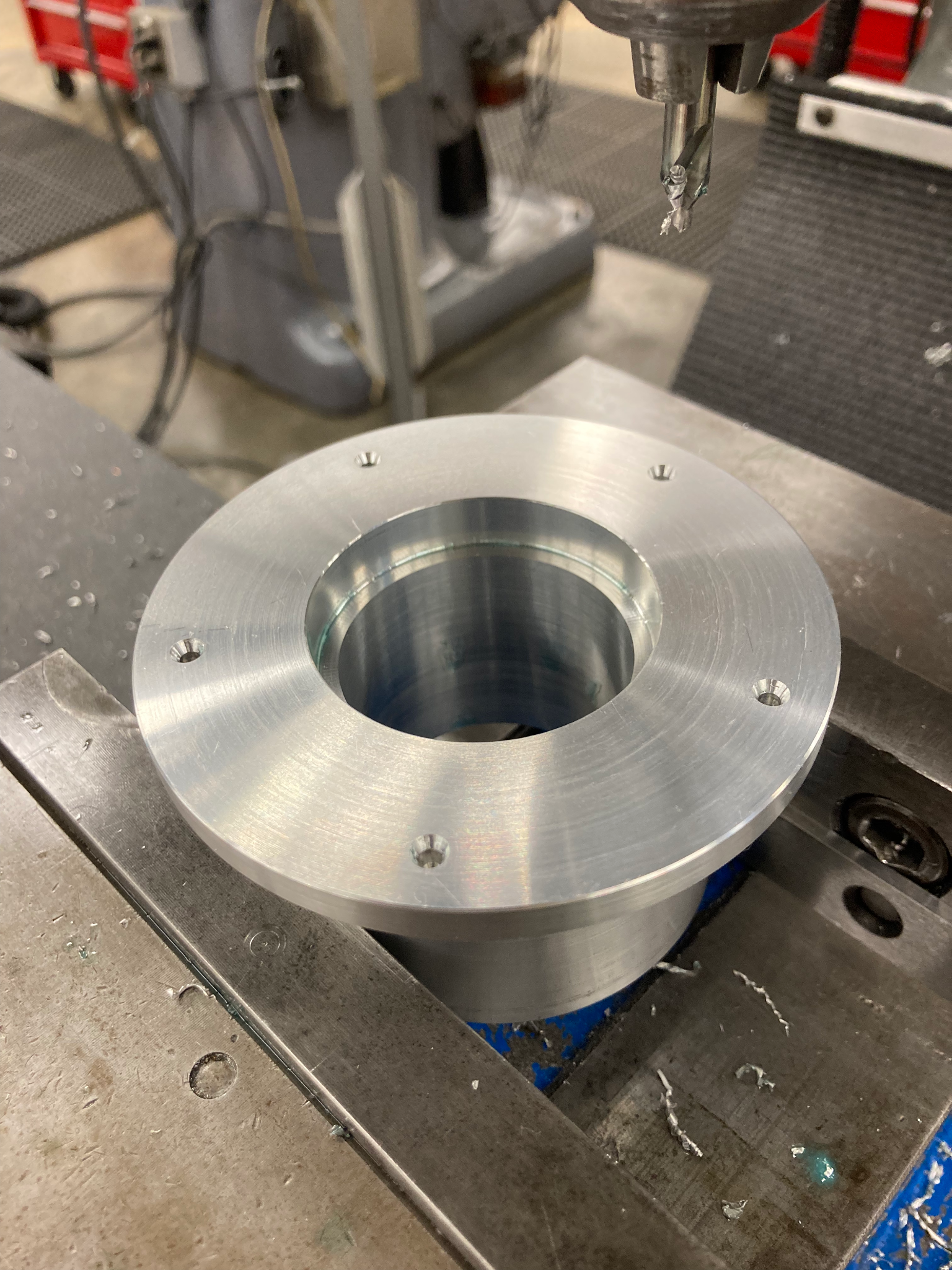
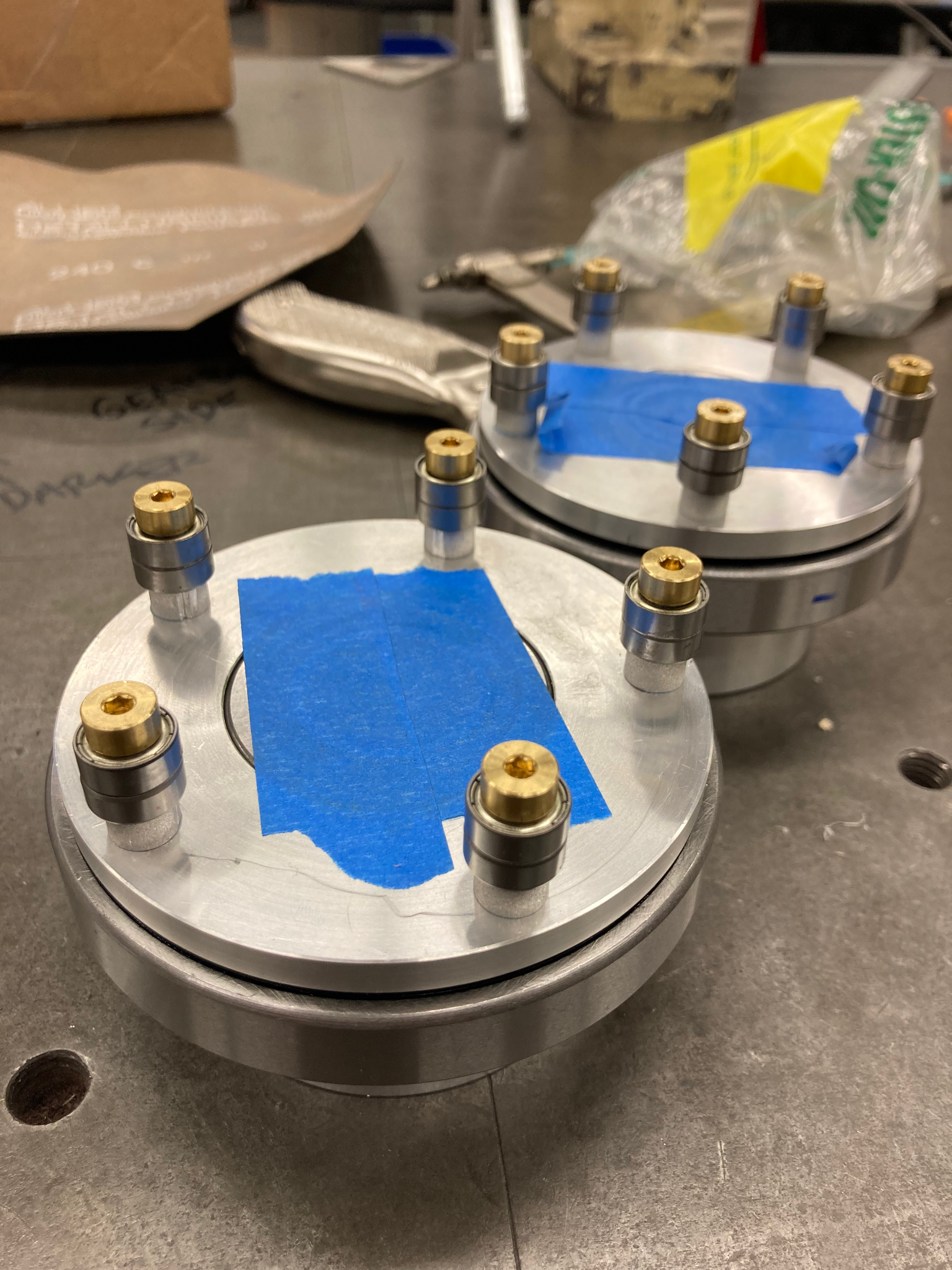
The input shaft component was the most fun to make. It is made of bearings, bolts, 3D-printed shaft components, water-jet cut aluminum brace pieces, and a machined Delrin cycloidal gear. The shaft needed to be a multi-part design and include eccentricity so I chose to 3D print them. I machined the Delrin gear on a CNC-retrofitted mill. I chose Delrin due to its low friction and low wear properties as this cycloidal drive design depends on sliding friction against the pins rather than rolling friction.
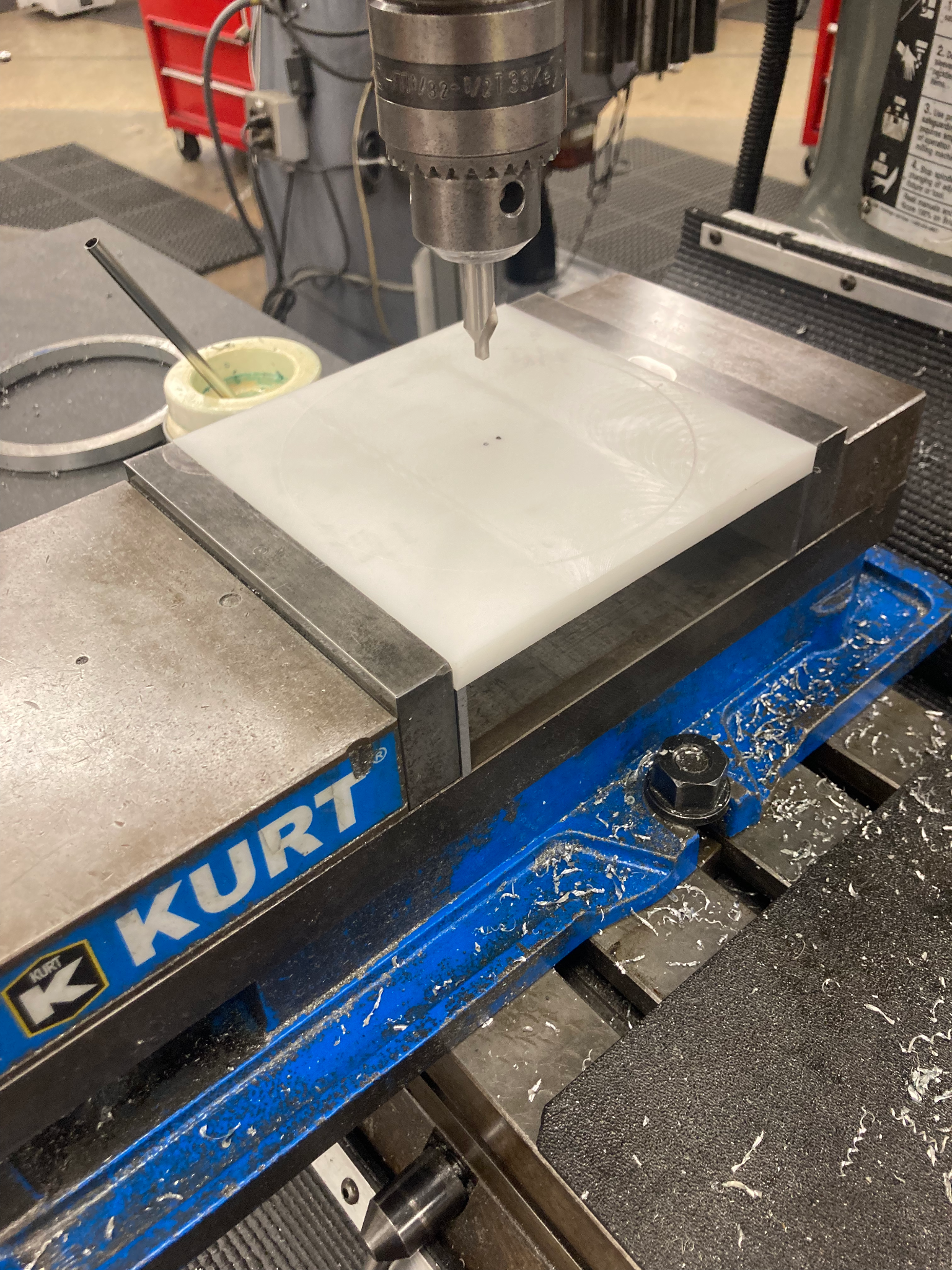
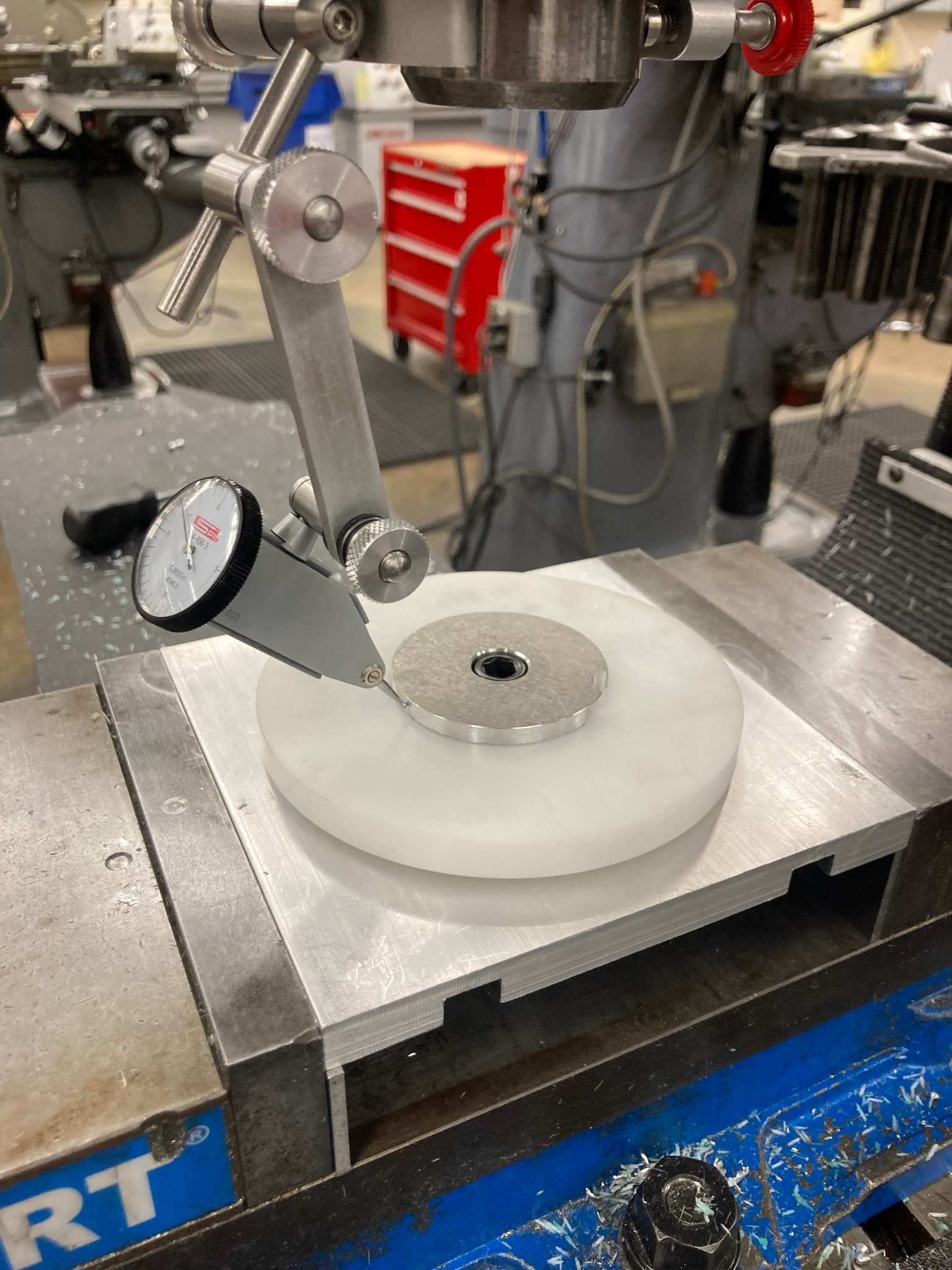
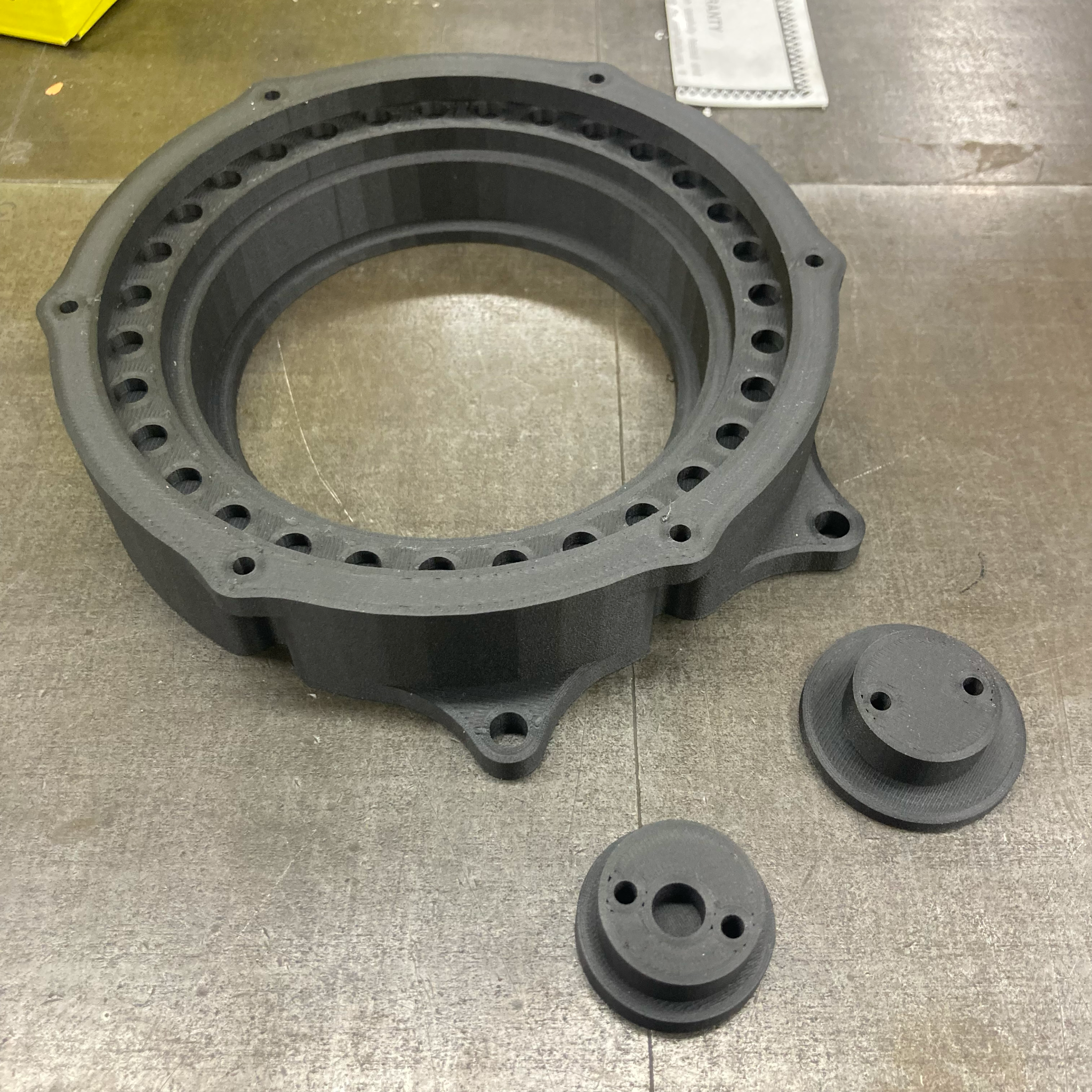
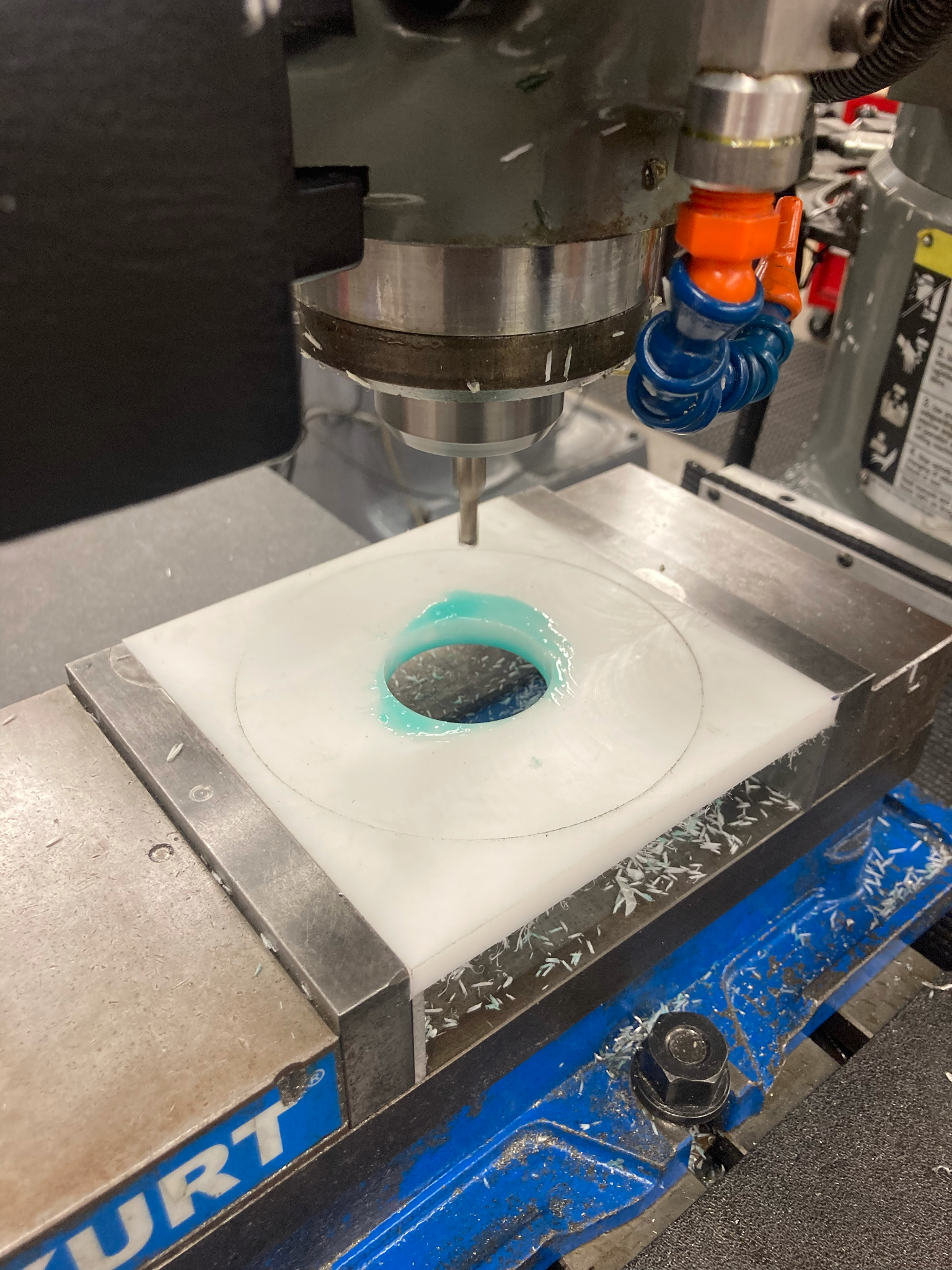
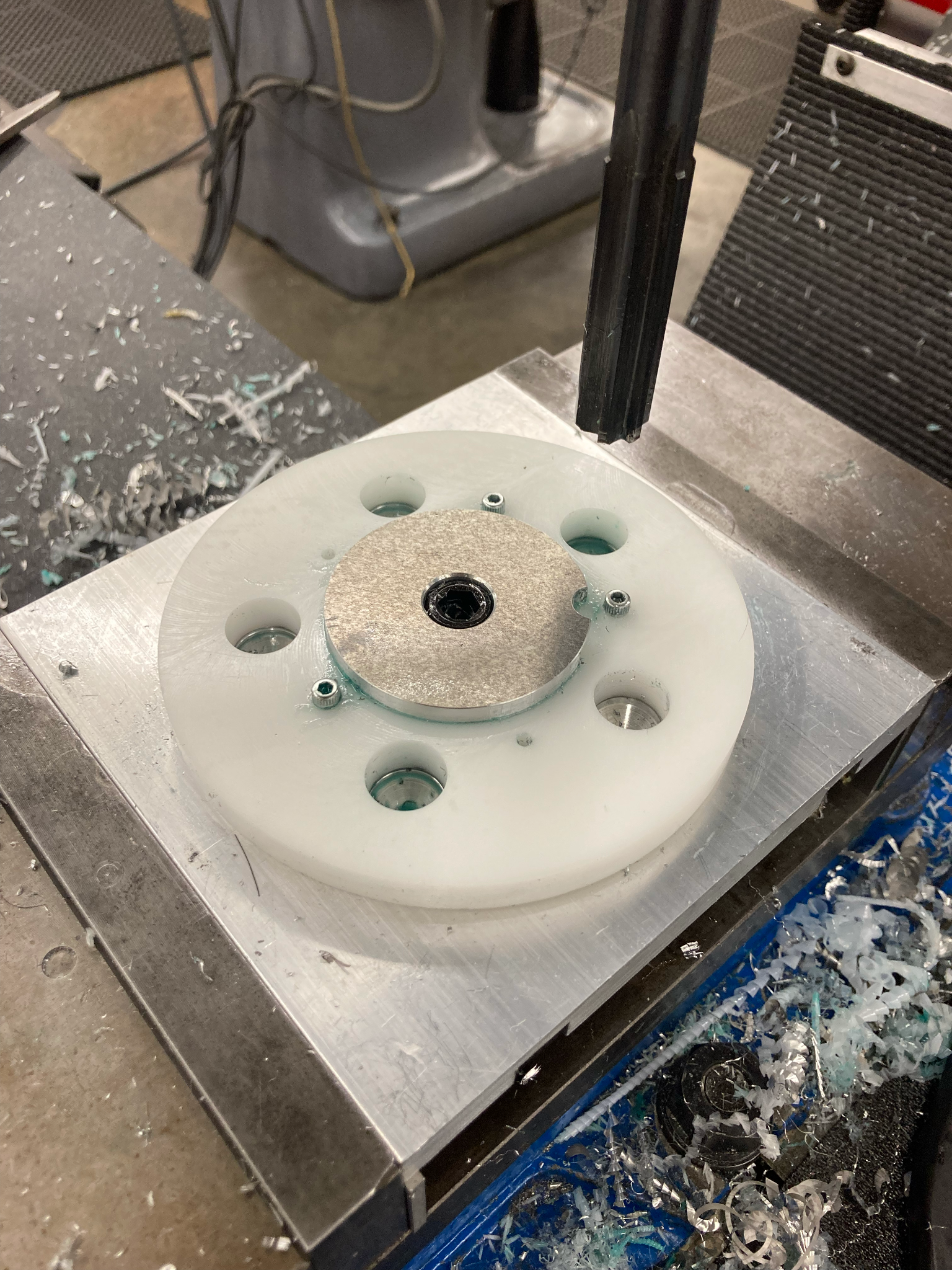
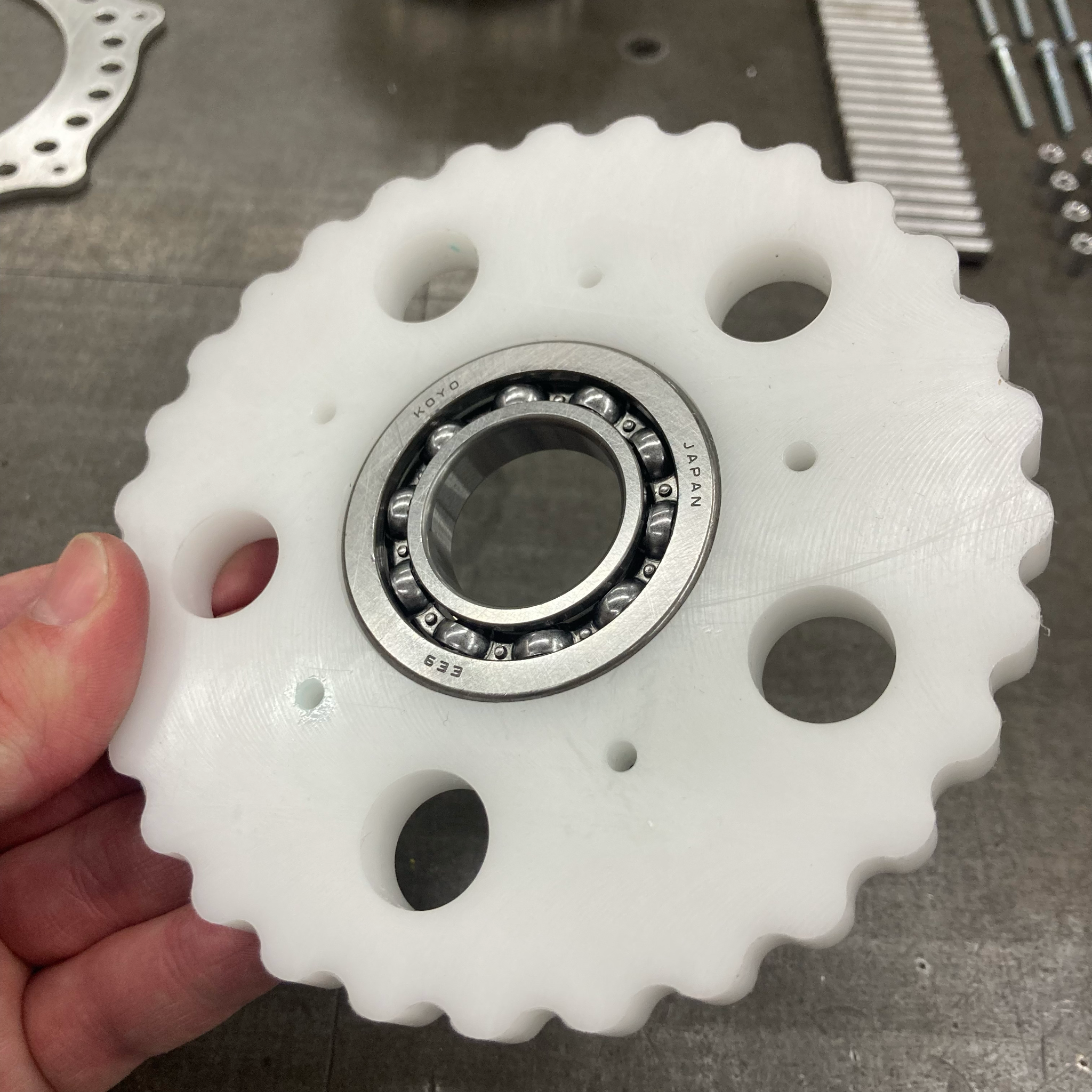

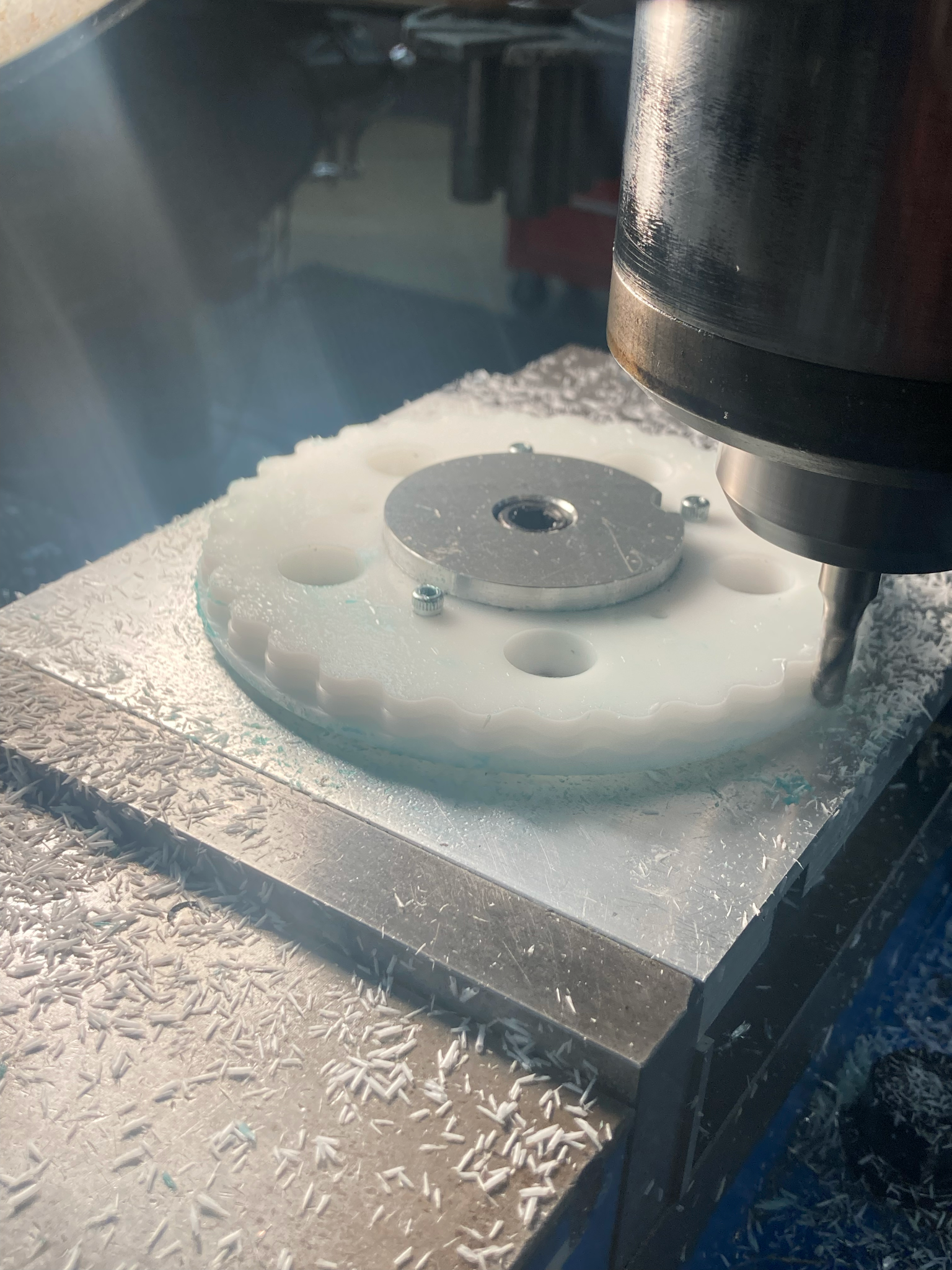
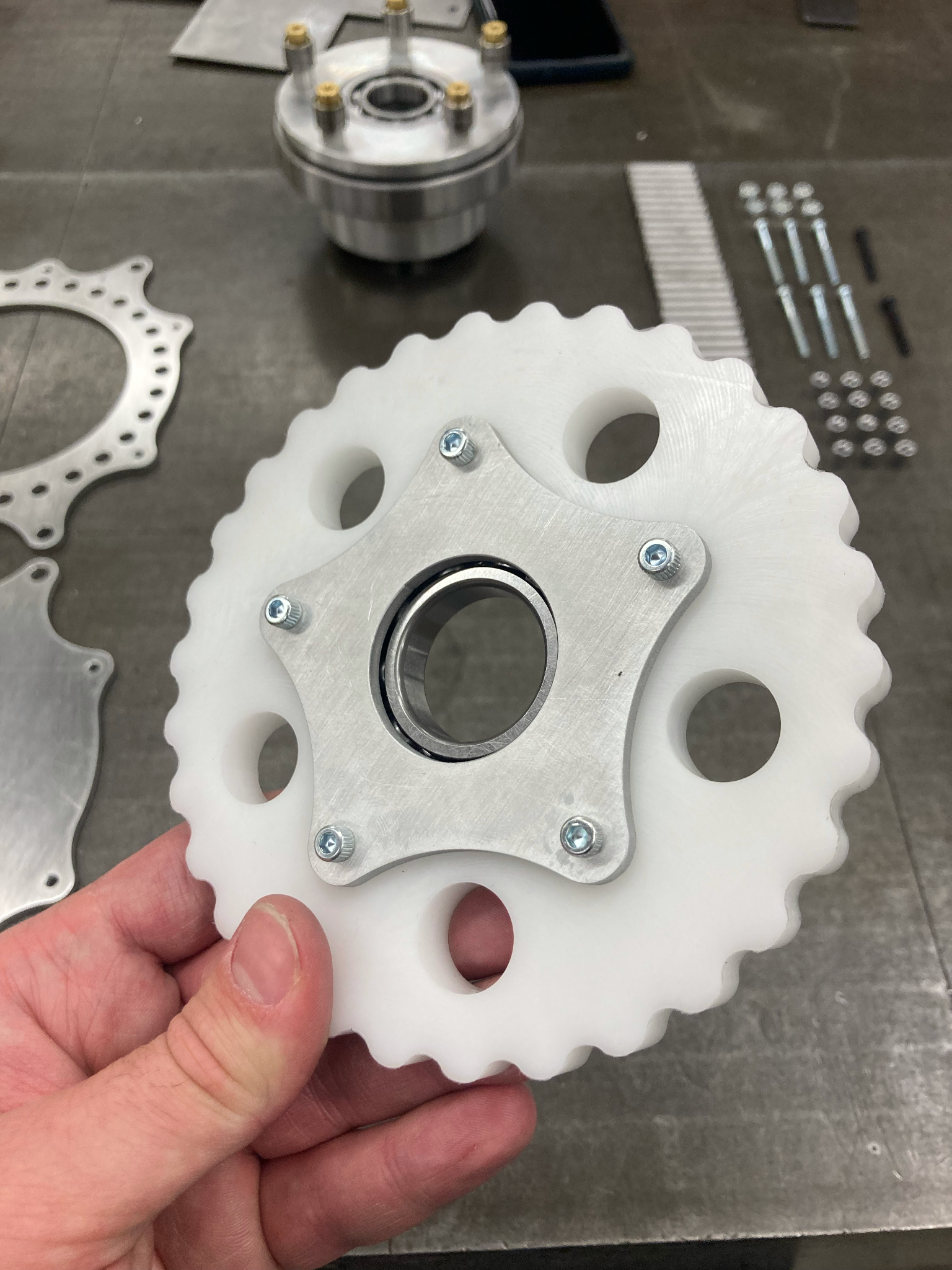
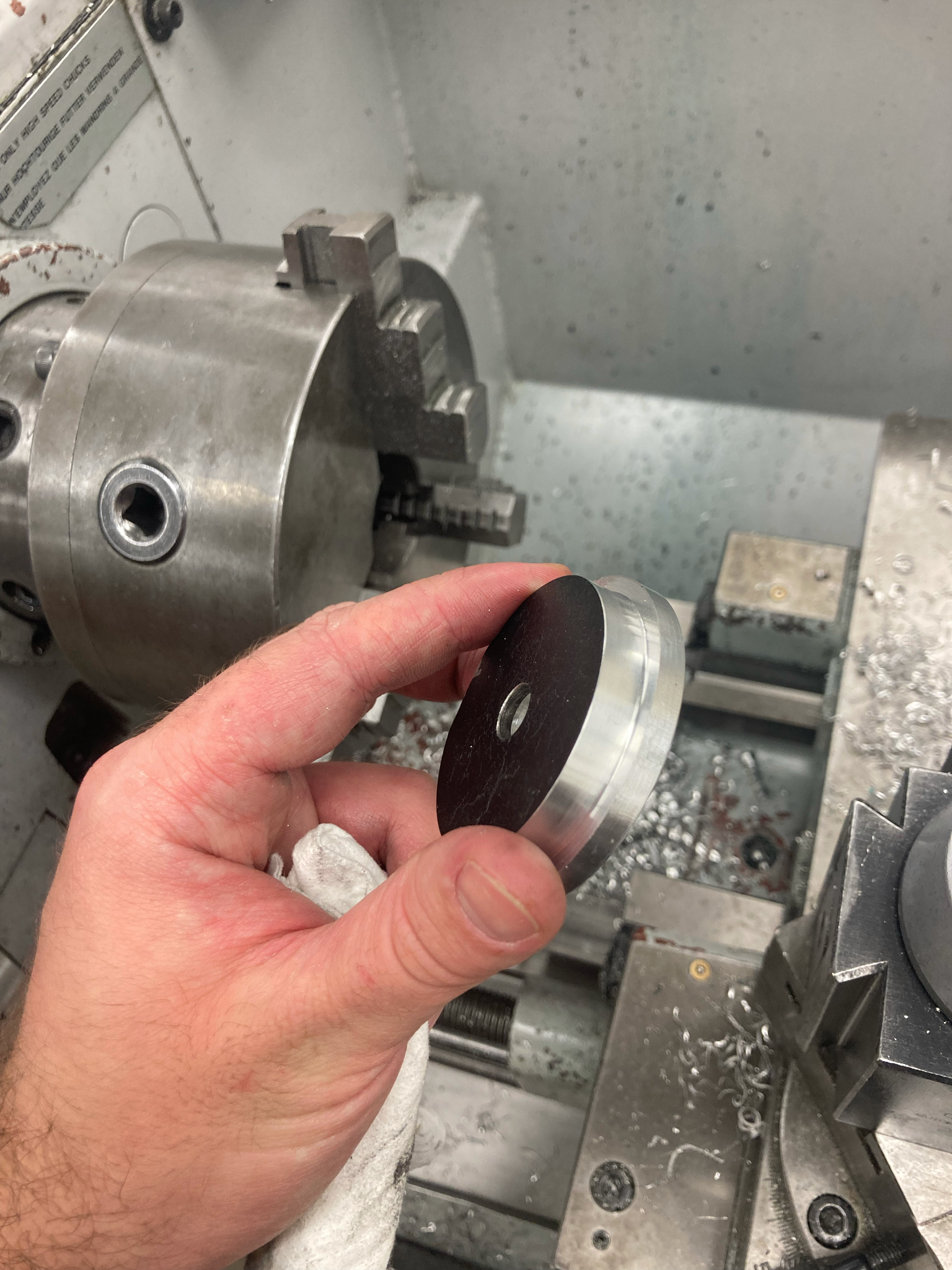
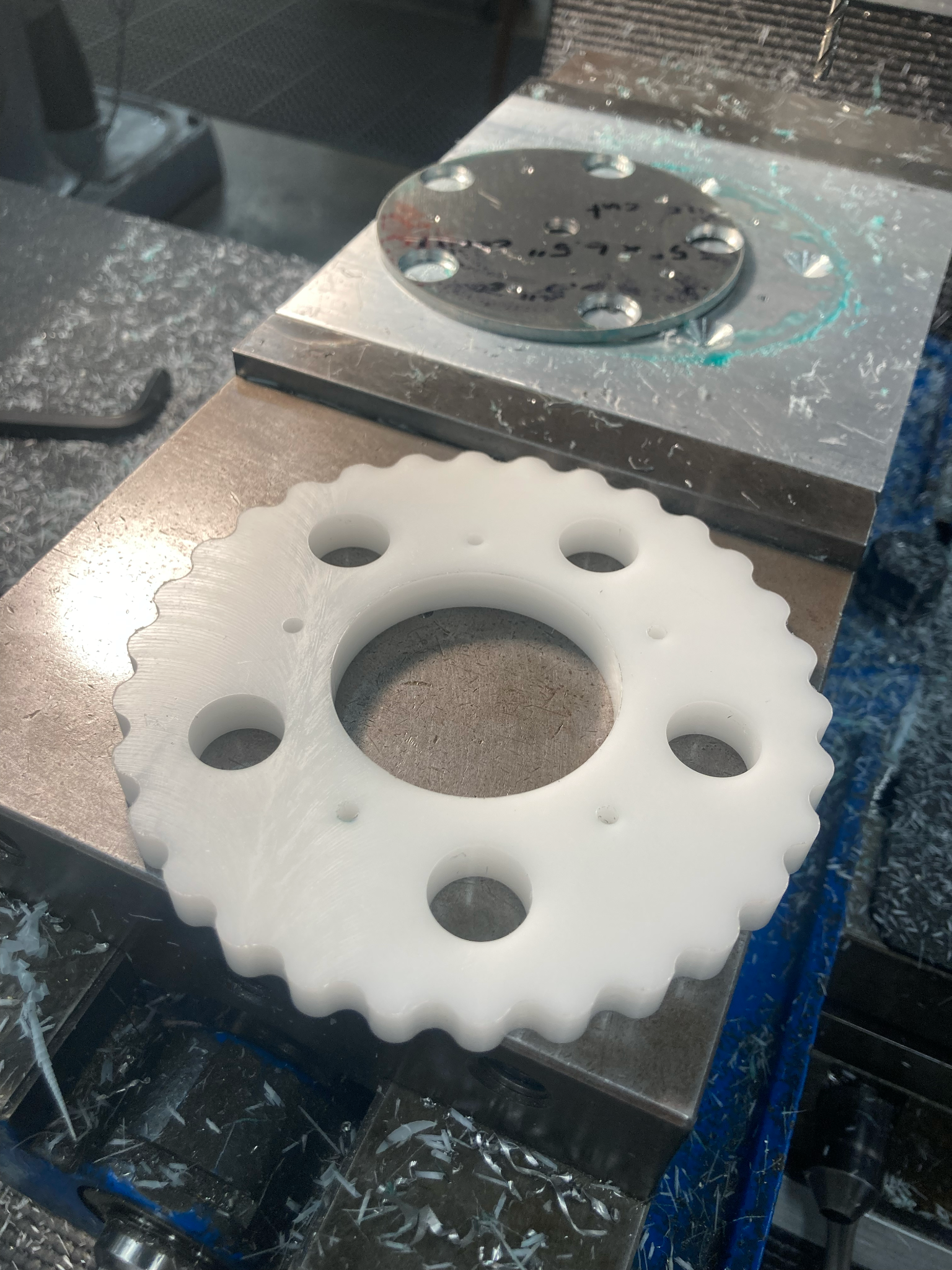
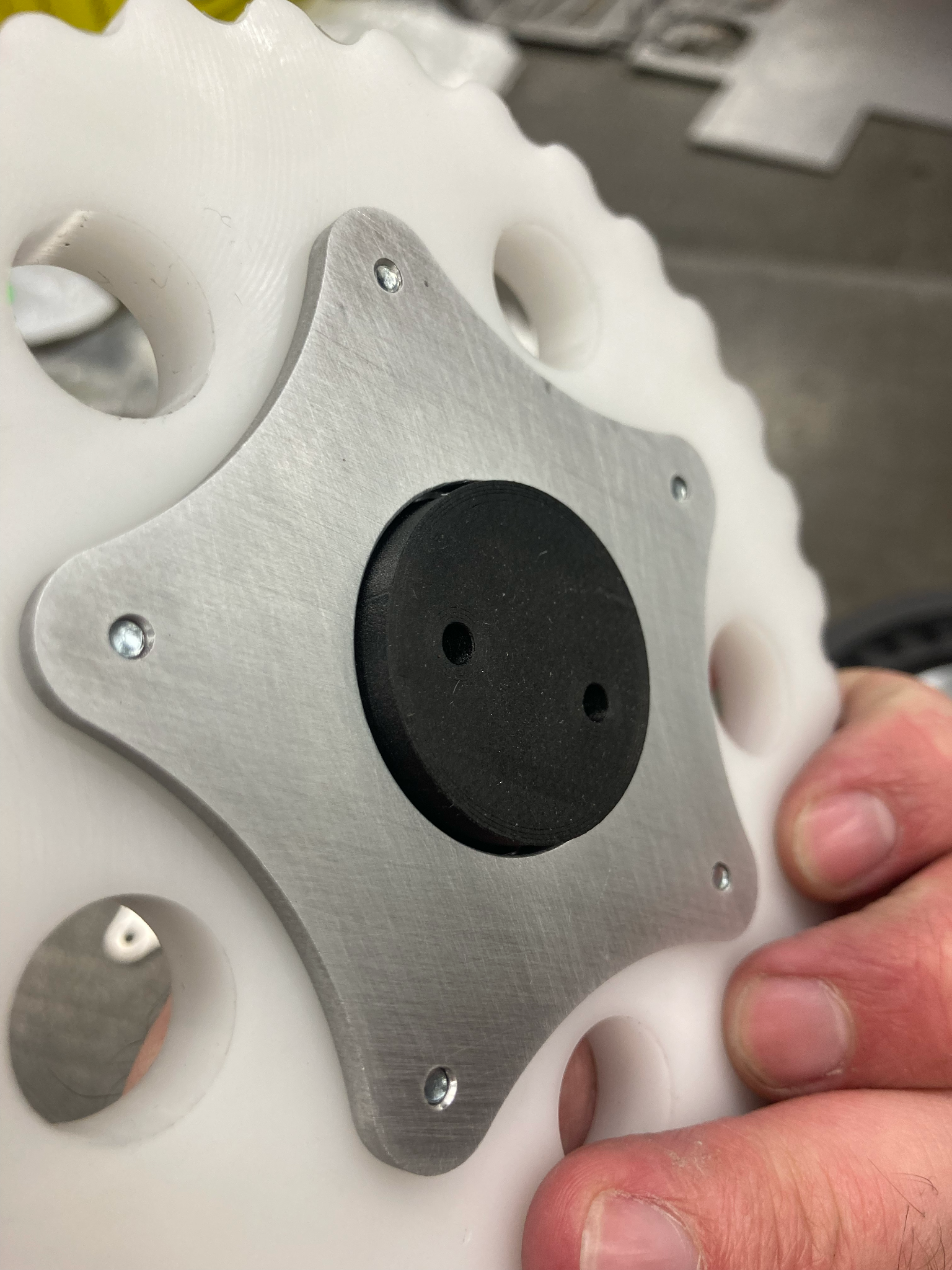
Assembling the two cycloidal drives was more satisfying than any Lego set I've built. It was extremely rewarding to see how well all the parts fit together, especially considering this was my first attempt at fabricating the design.
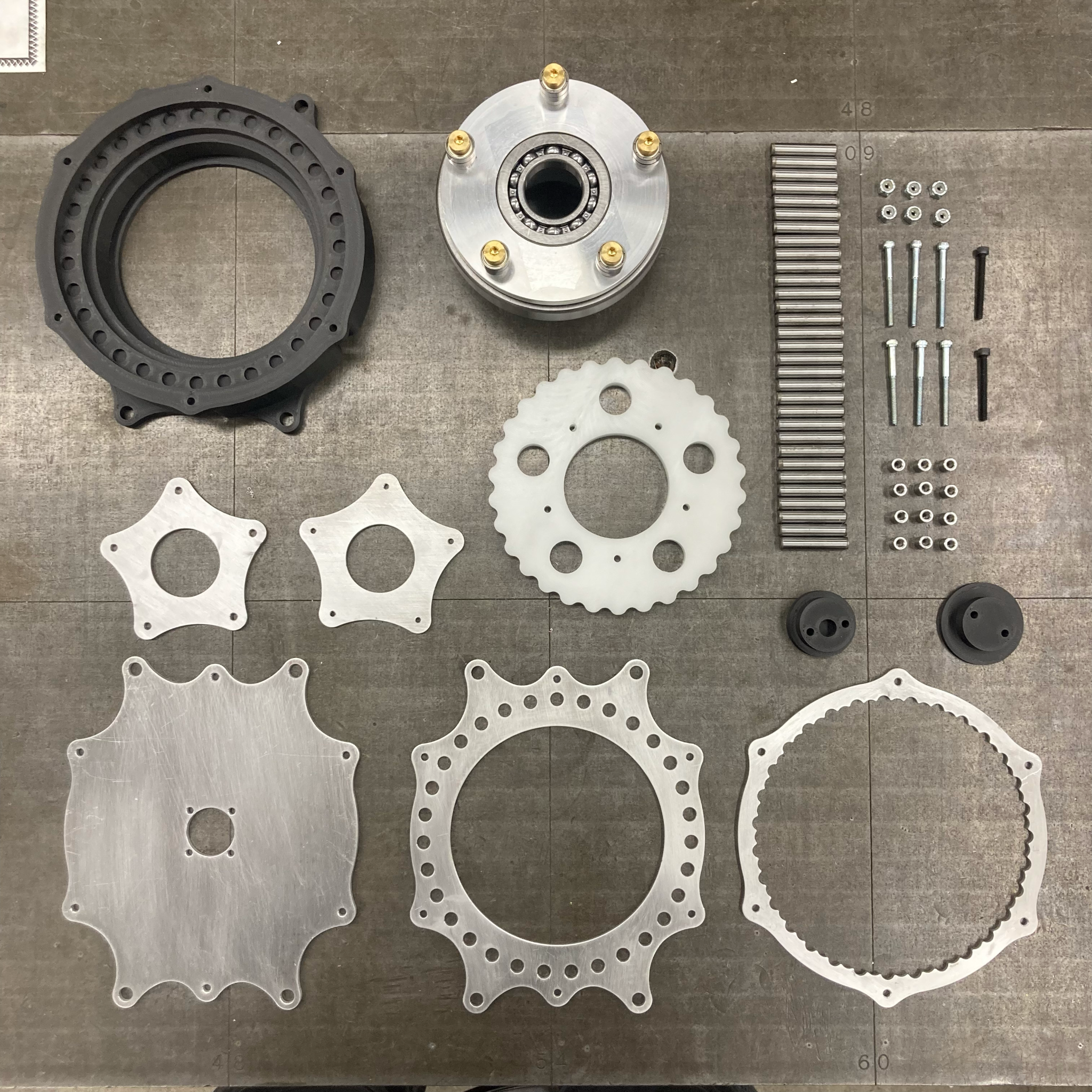
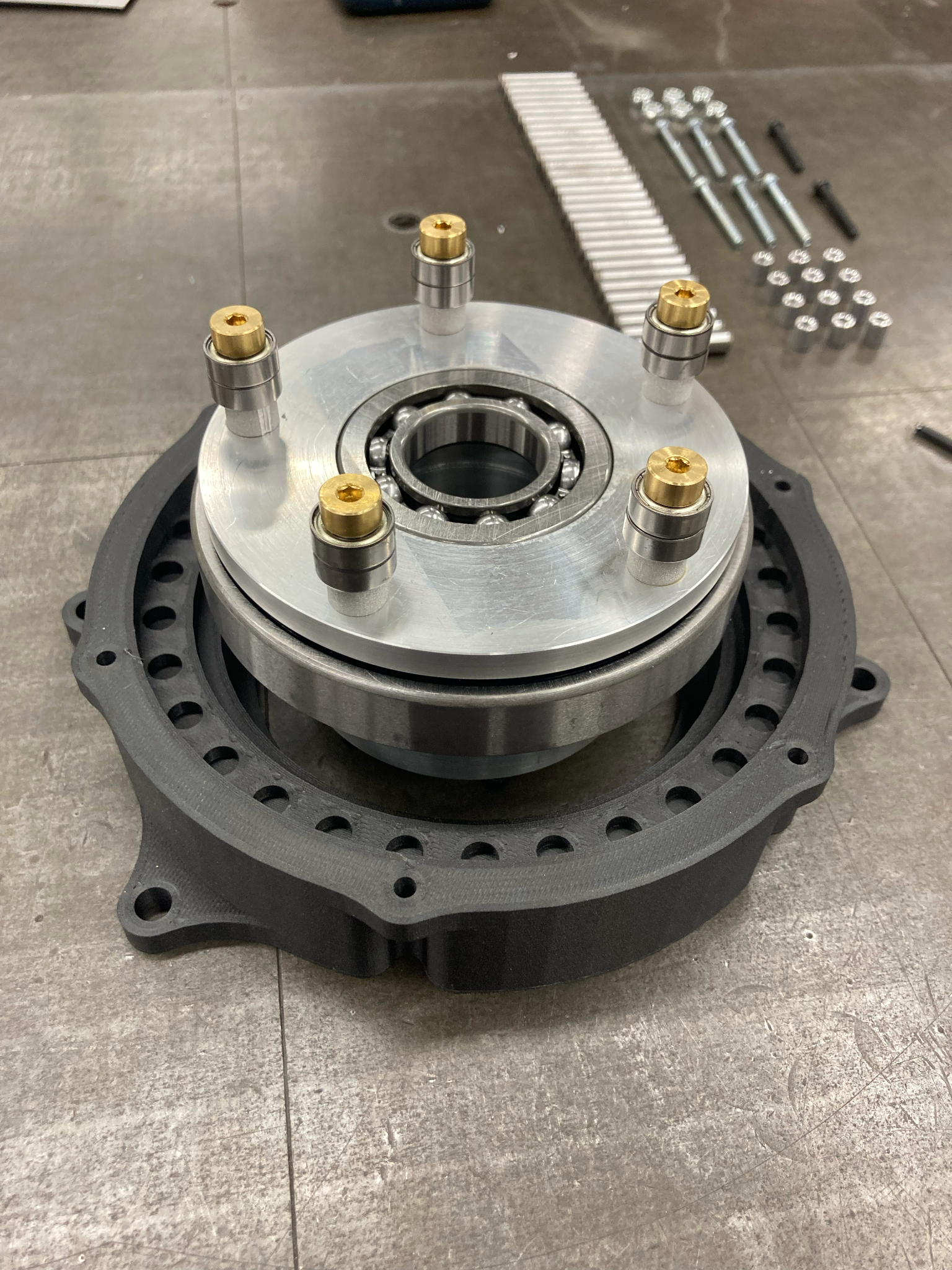
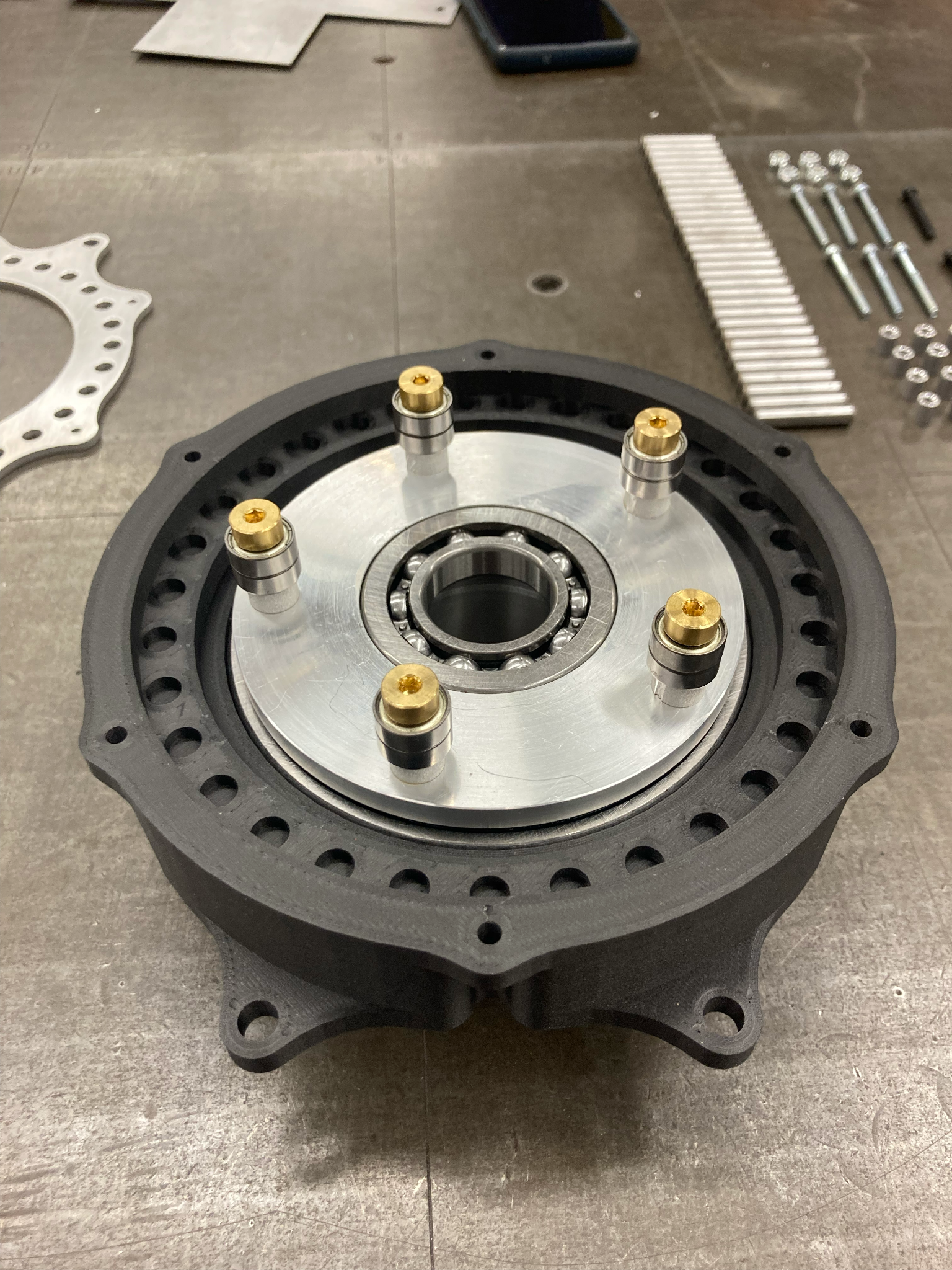
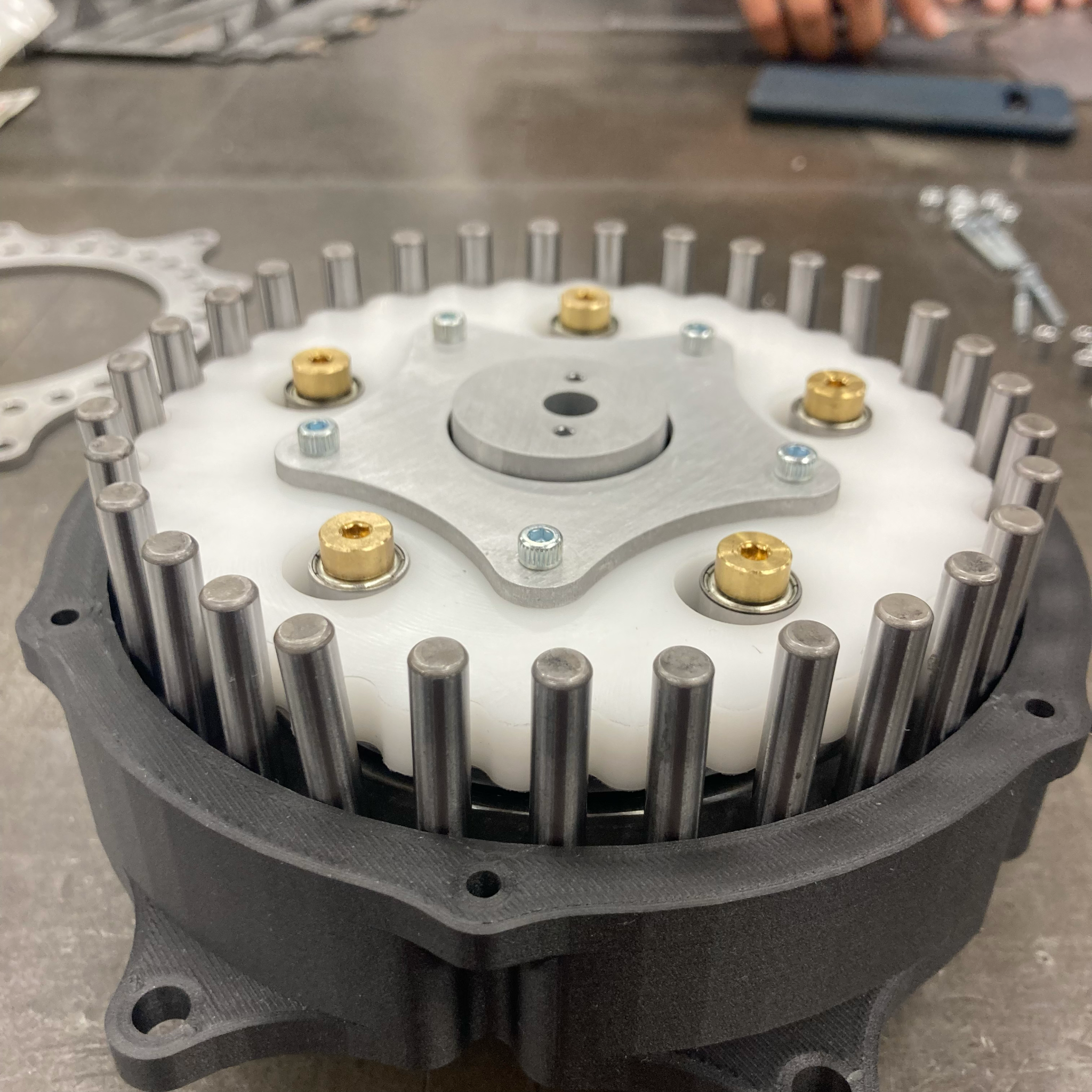
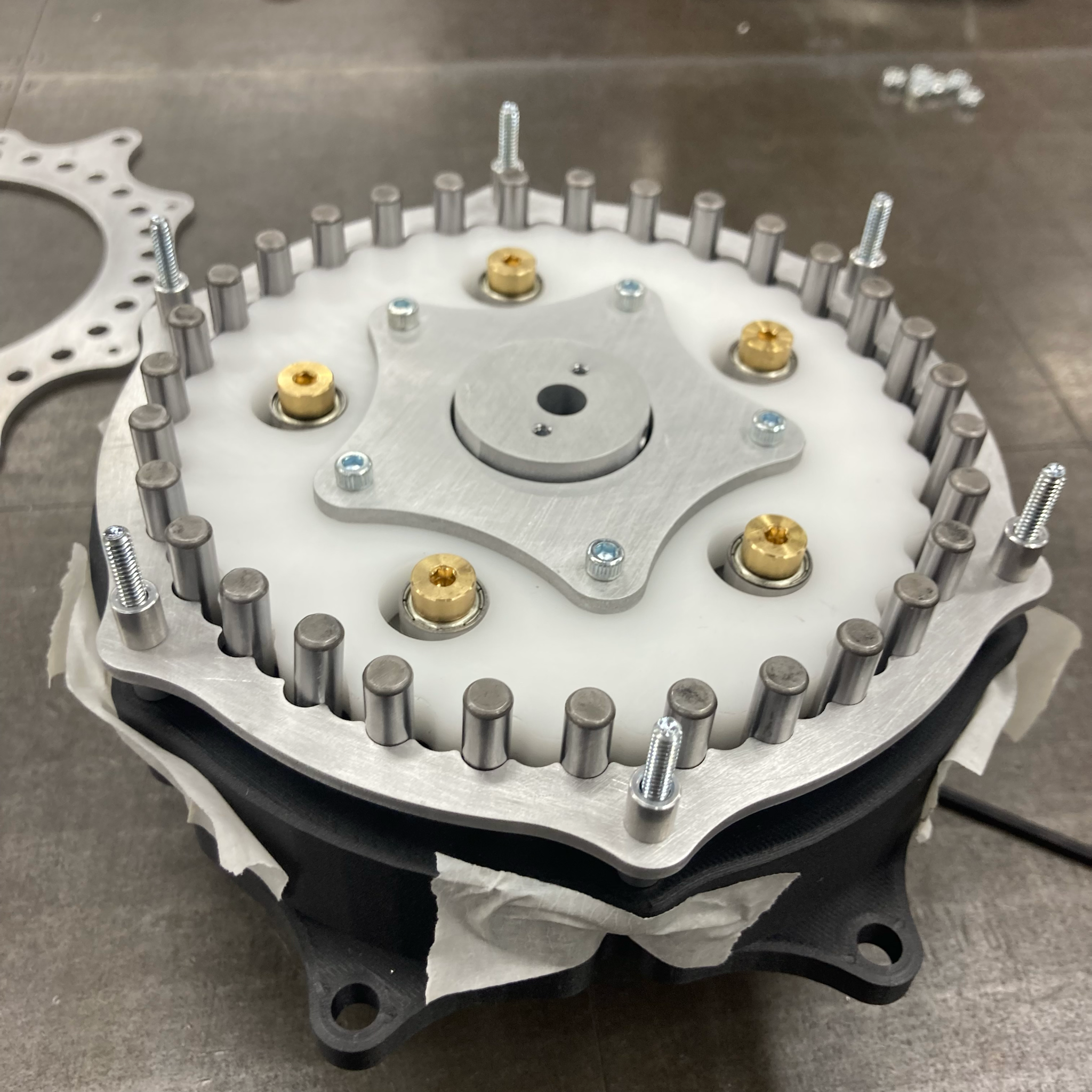
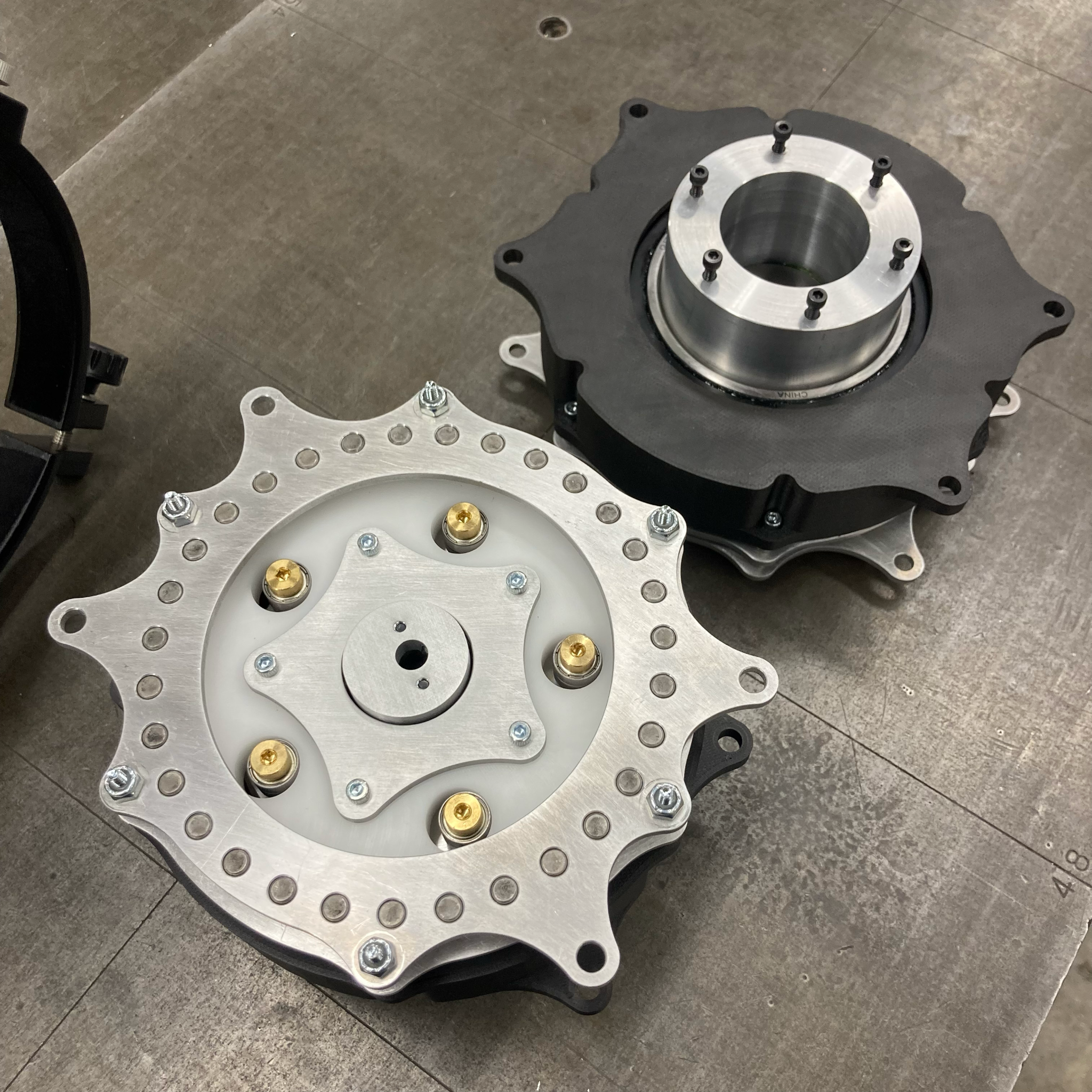
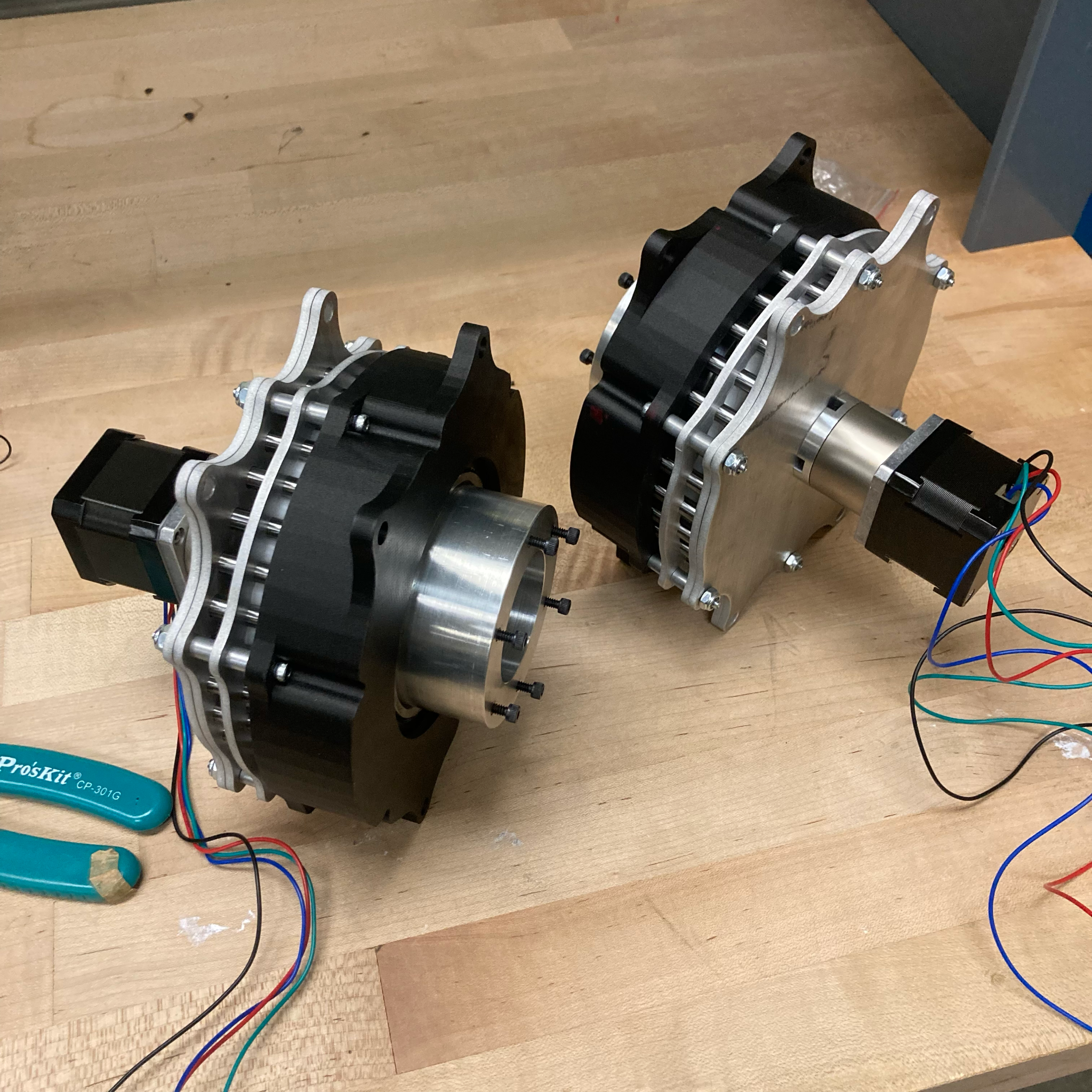
Fabricating the Rest of the Telescope Mount
I fabricated the rest of the parts for the telescope mount which was all of the framing and mounting parts. All of these parts were water-jet cut from 1/4-inch thick aluminum and I decided that the frame needed a nice paint job.
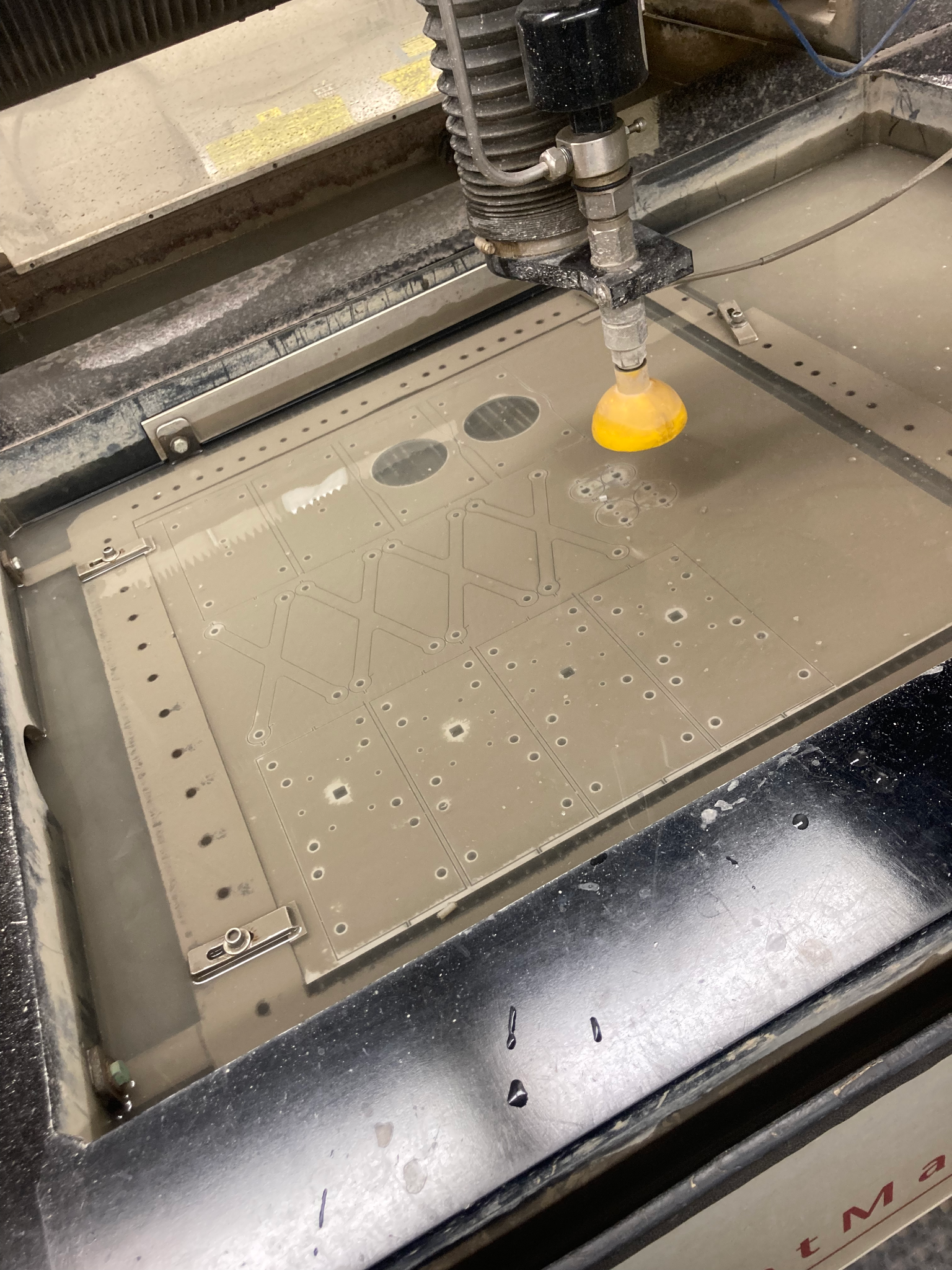
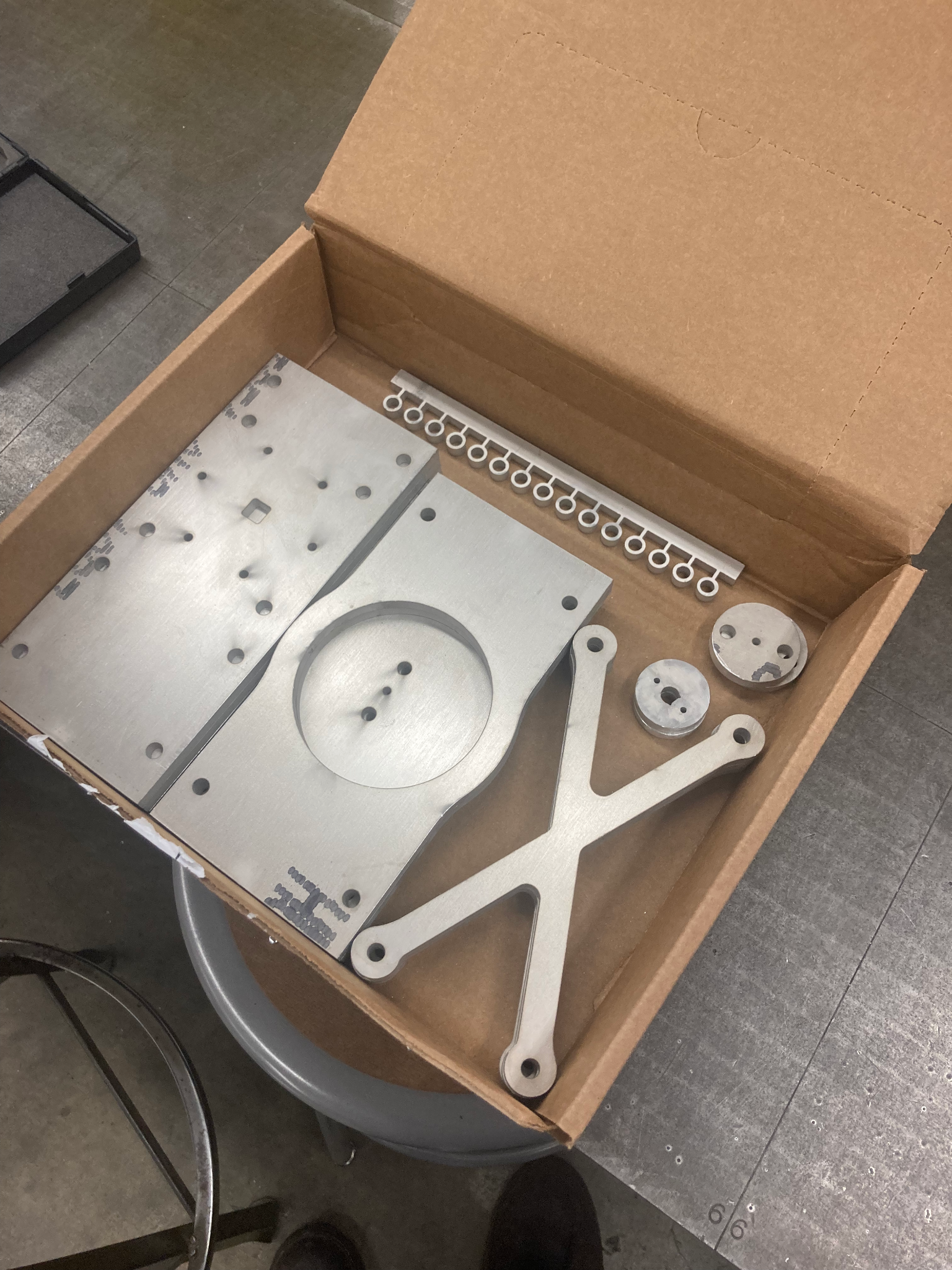
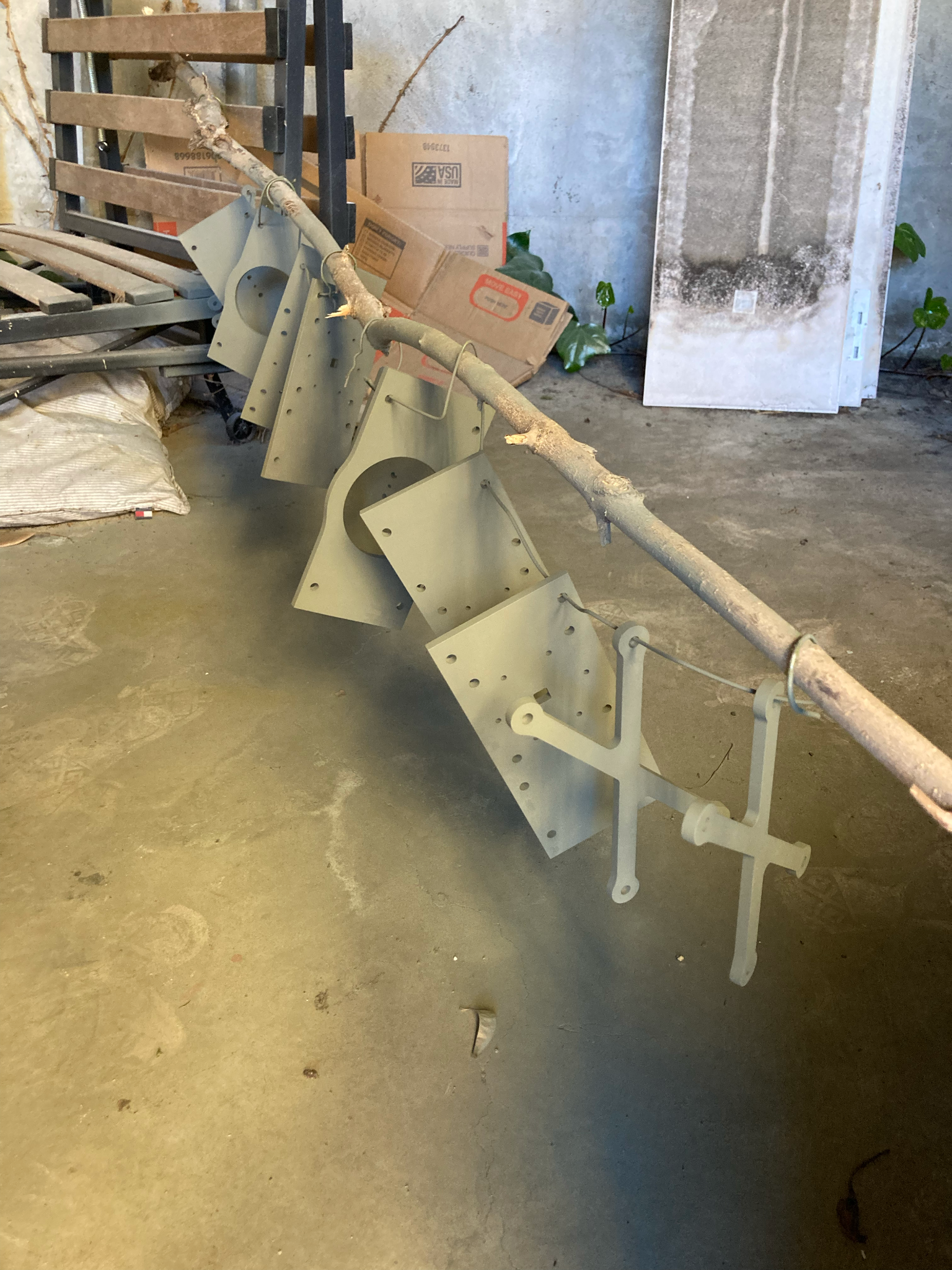
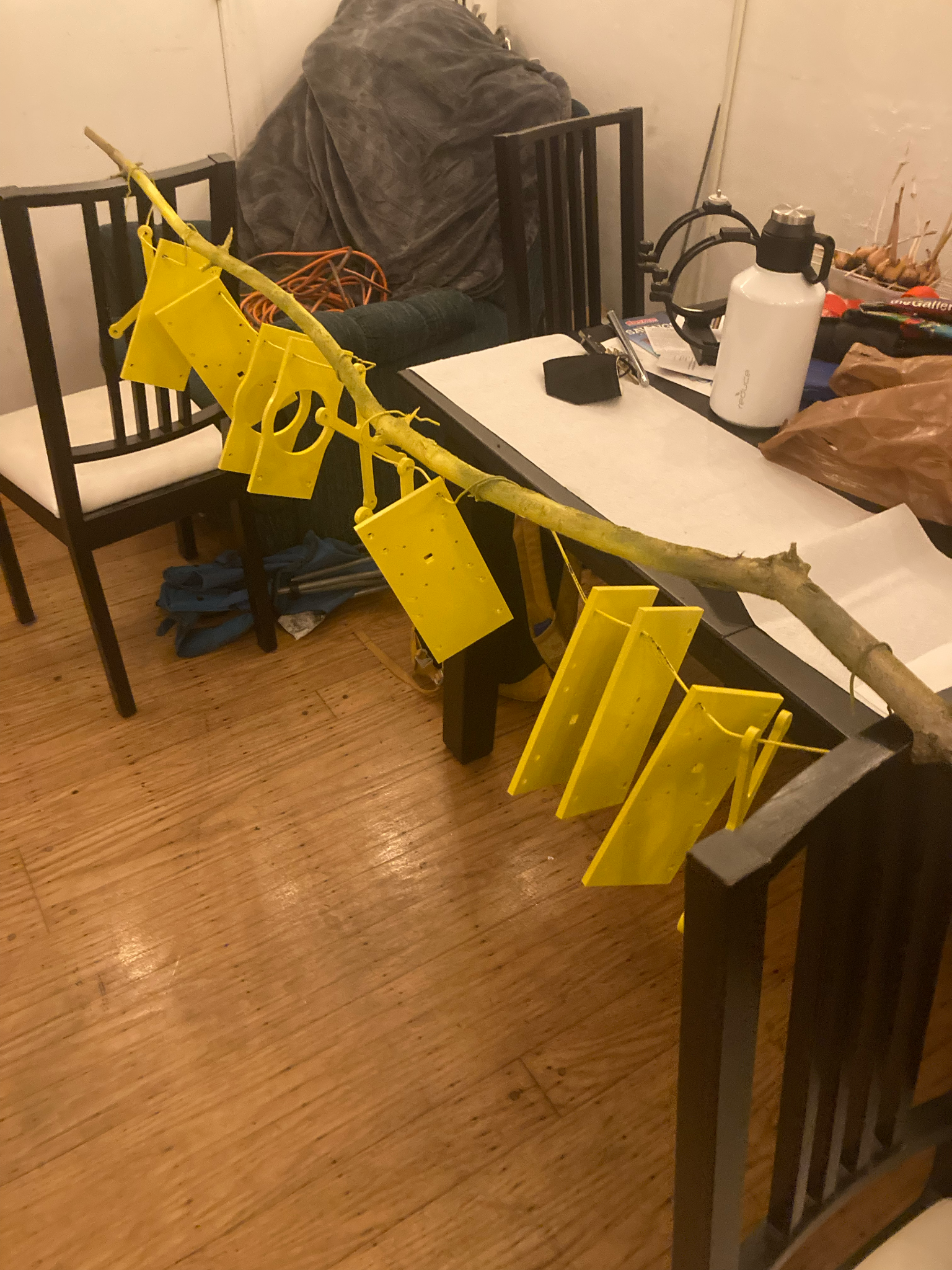
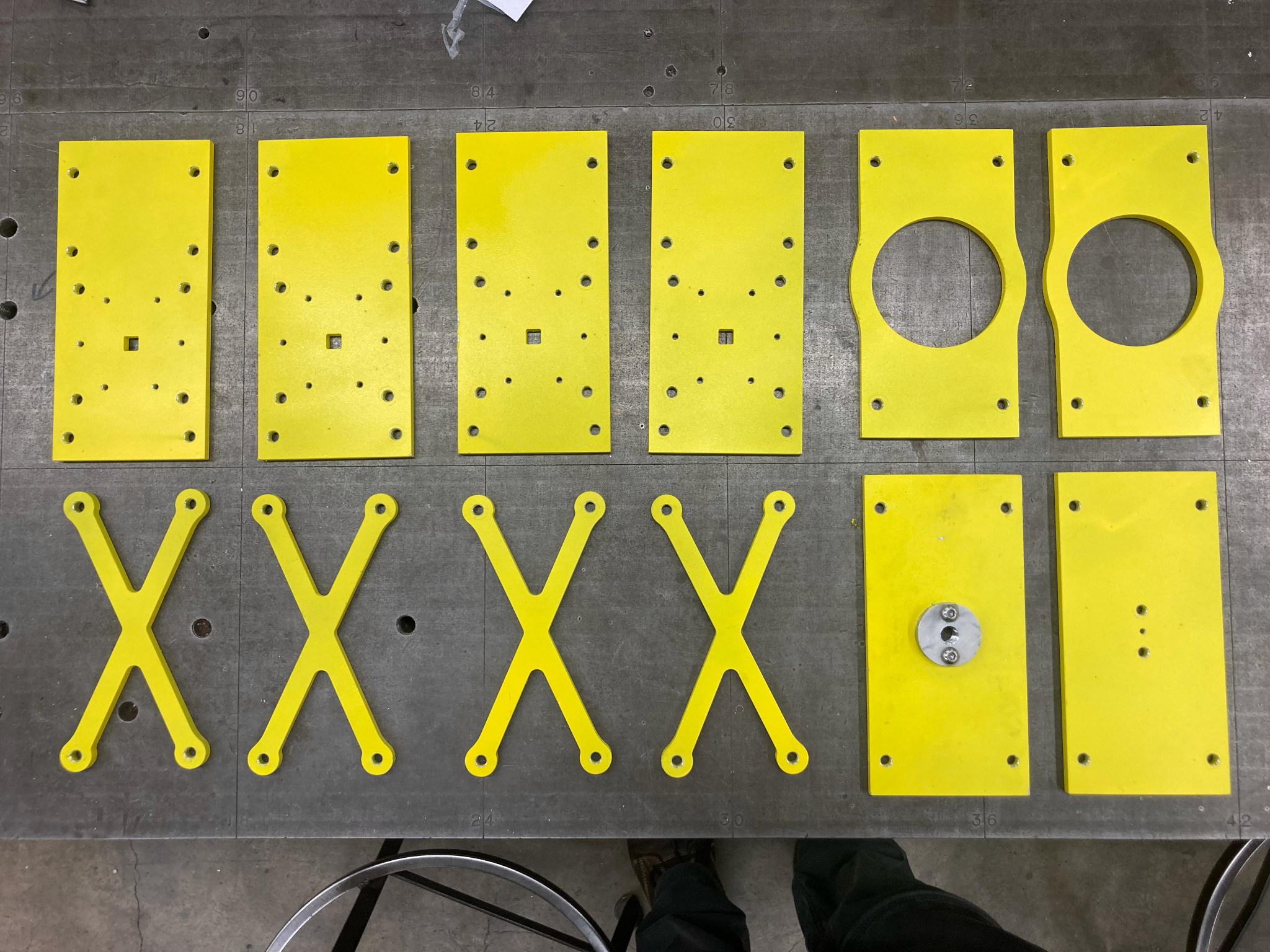
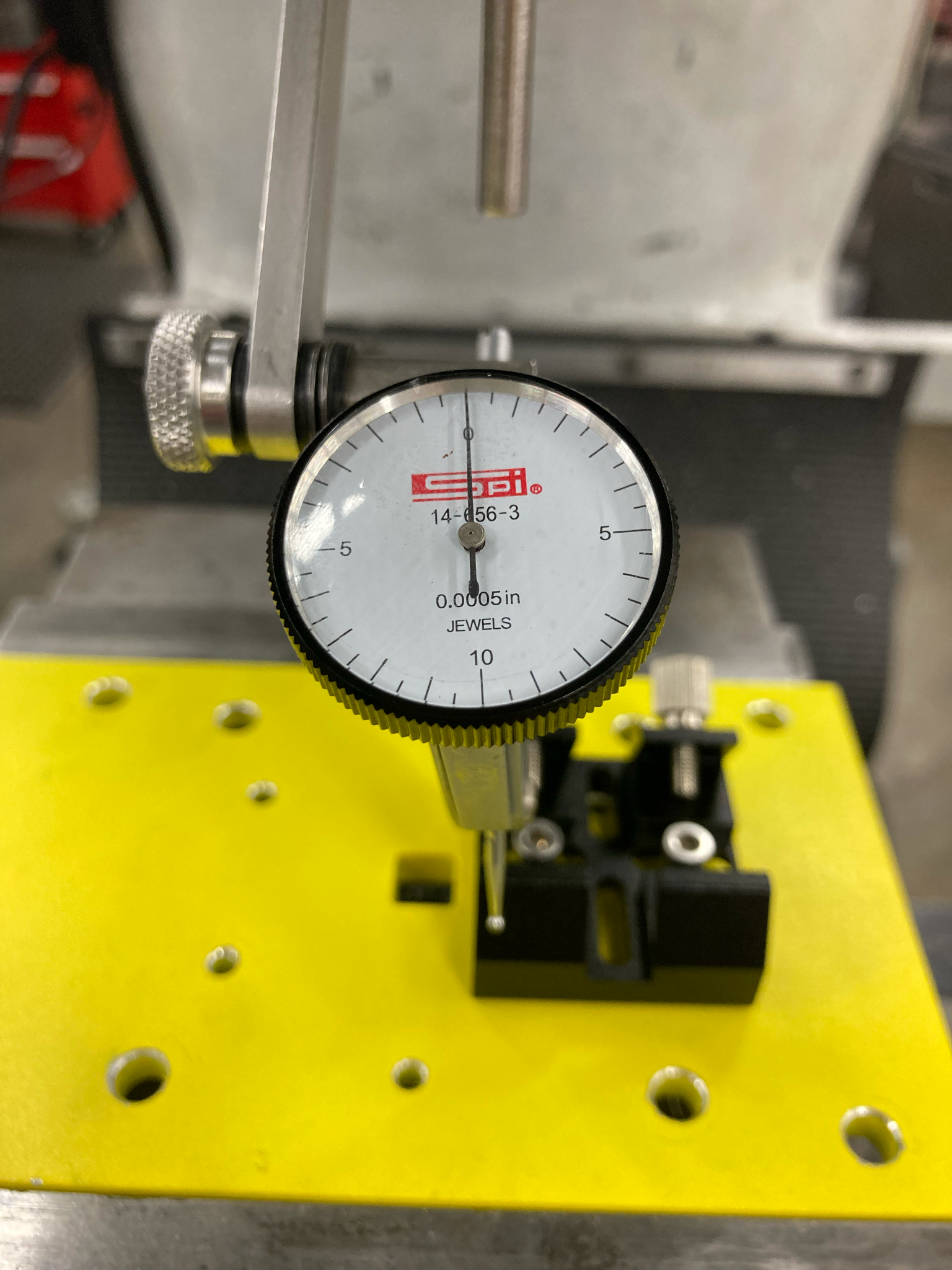
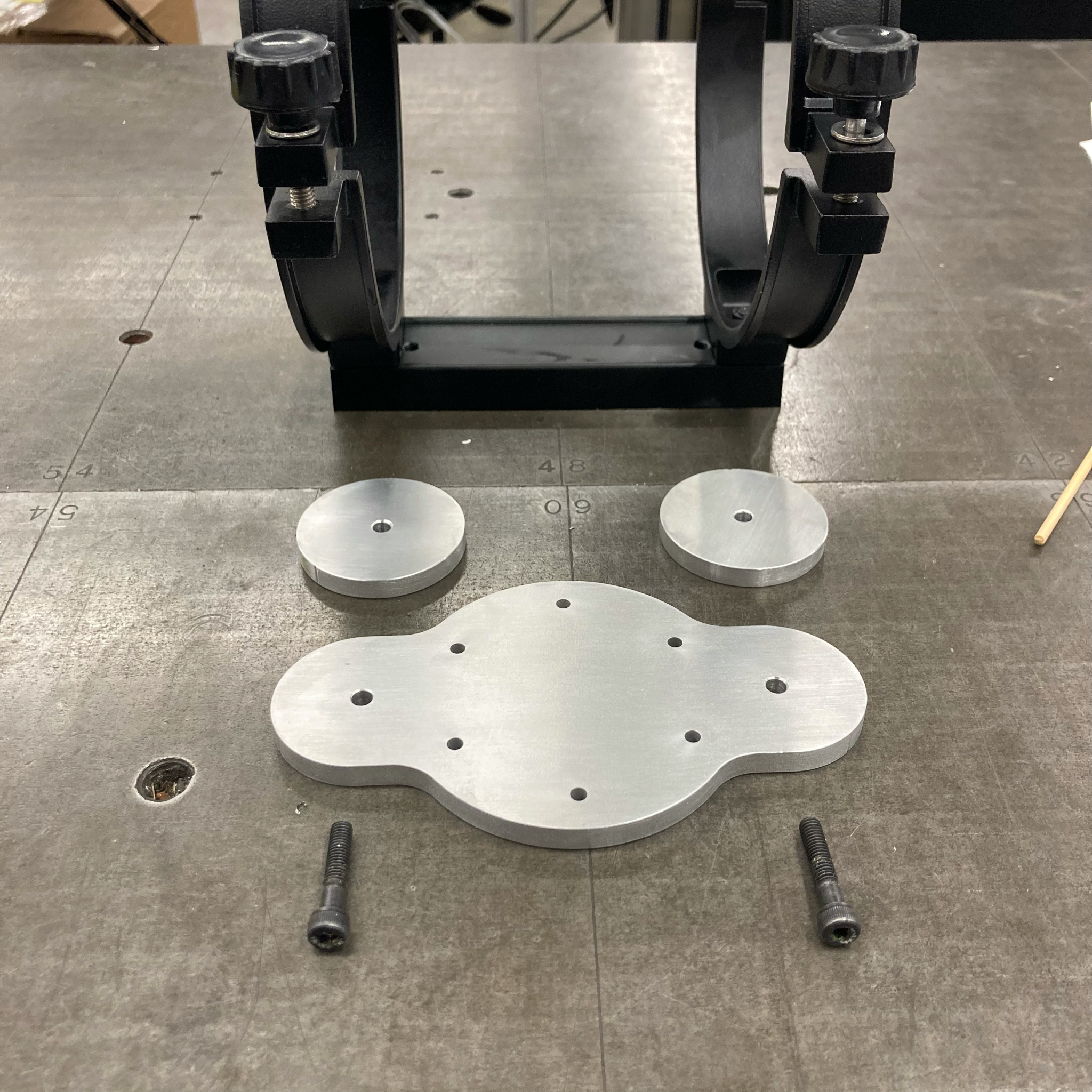
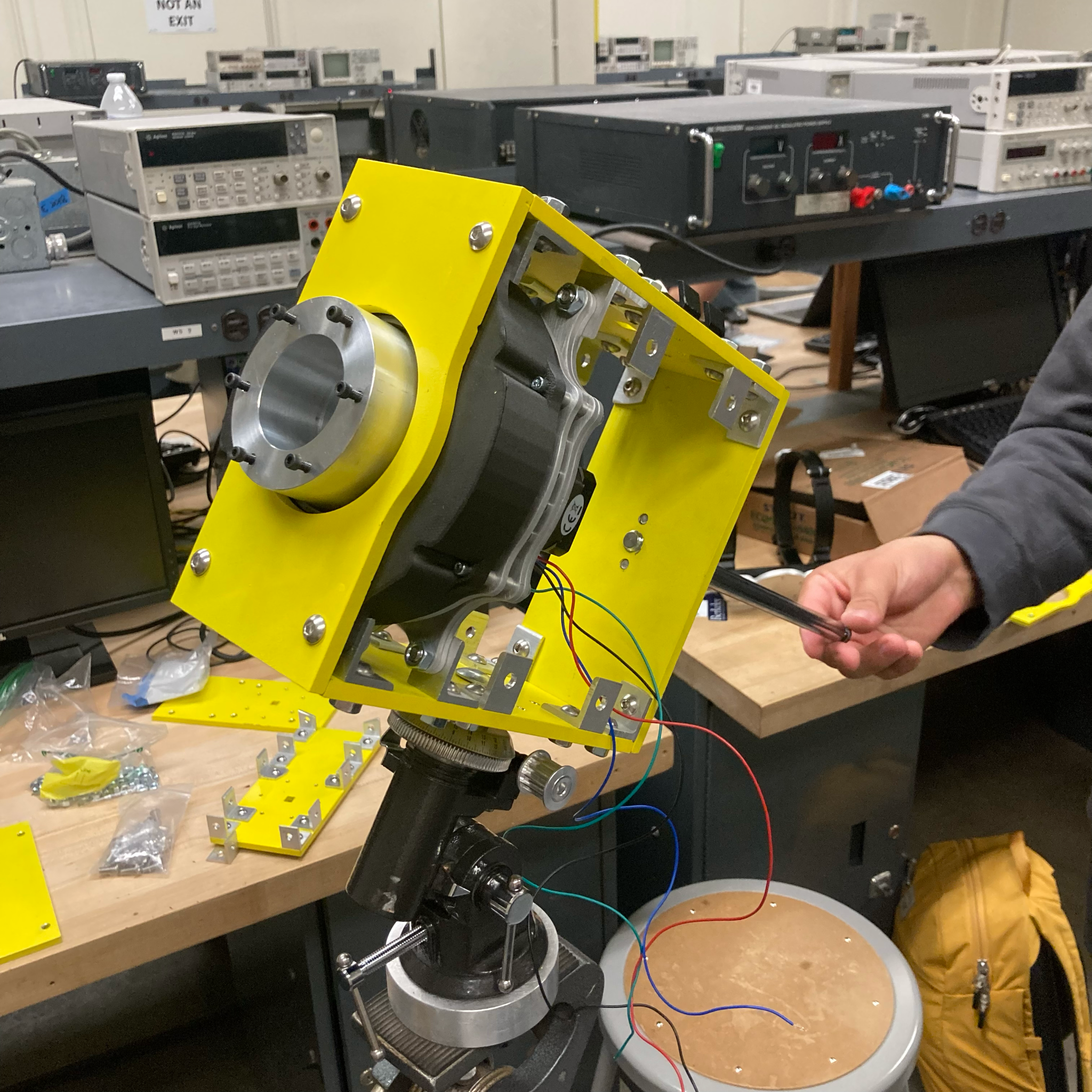
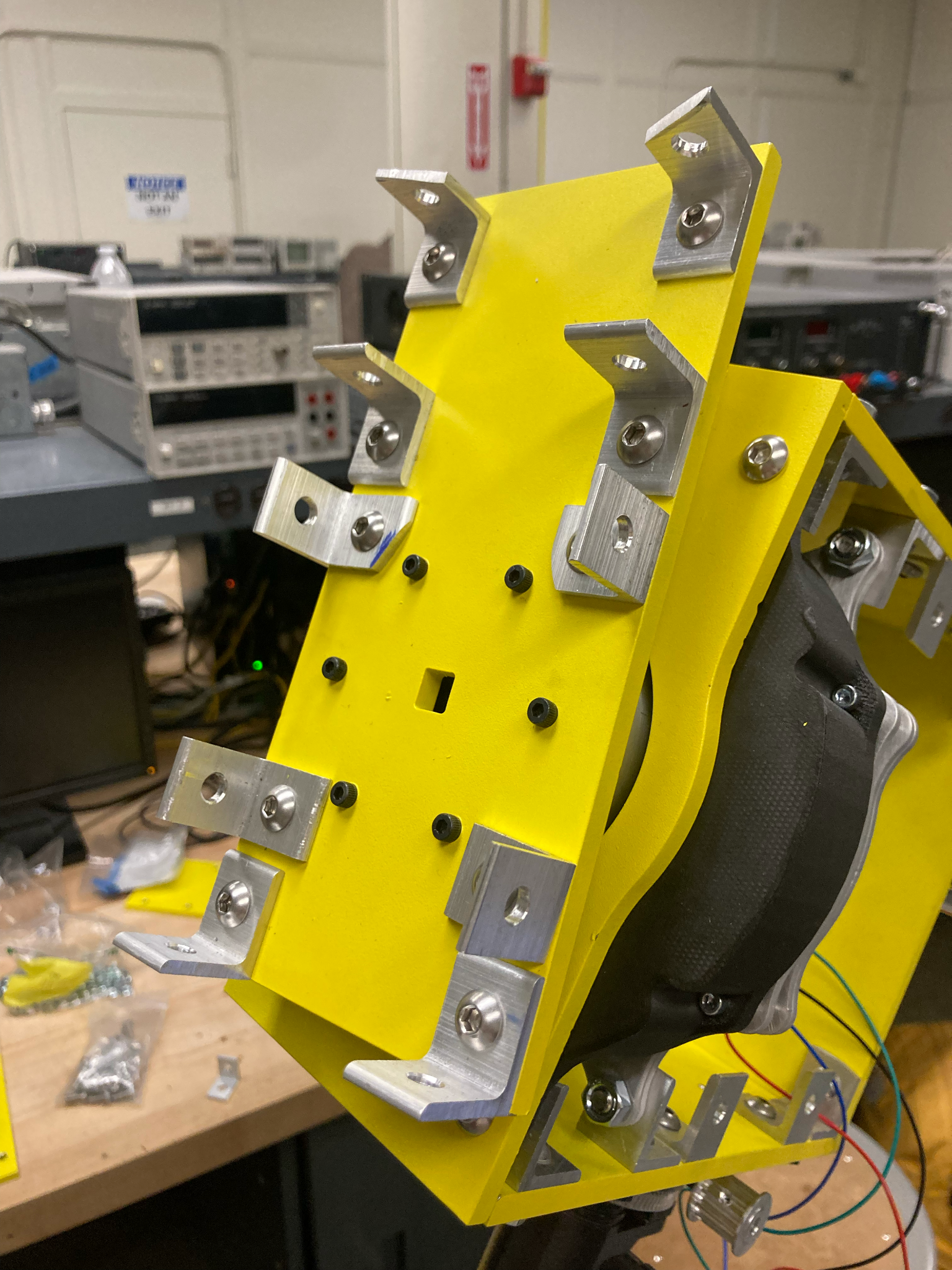
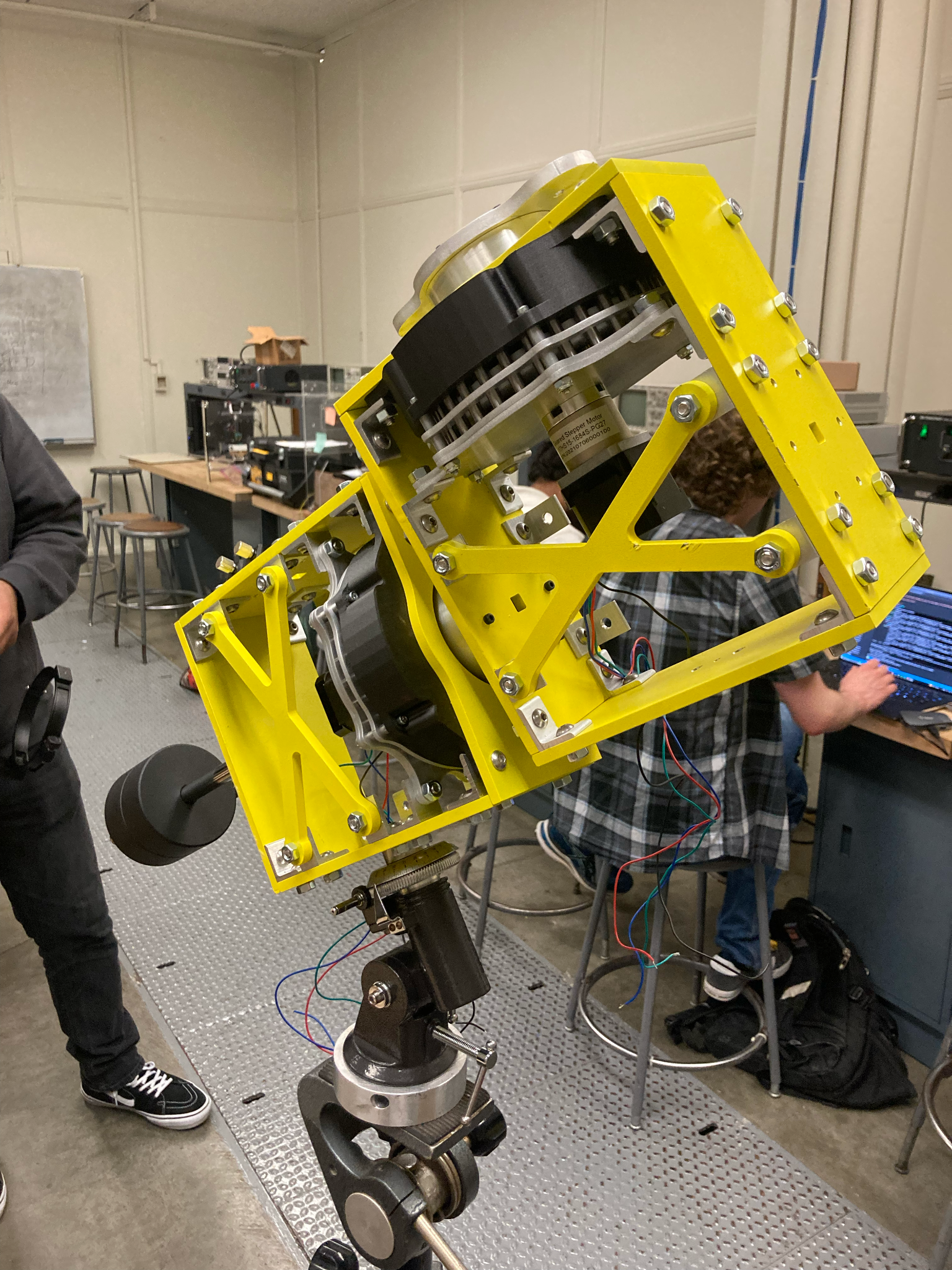
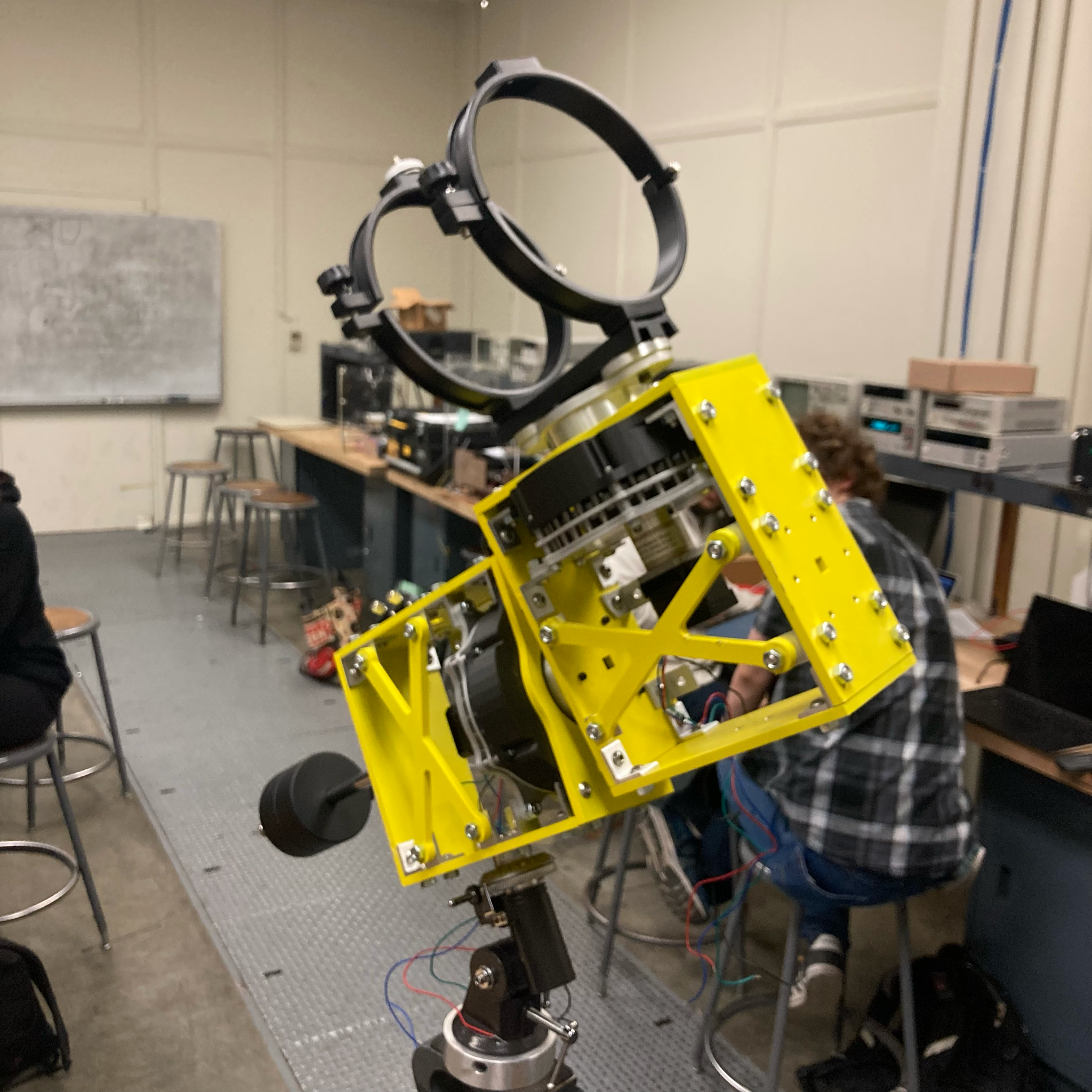
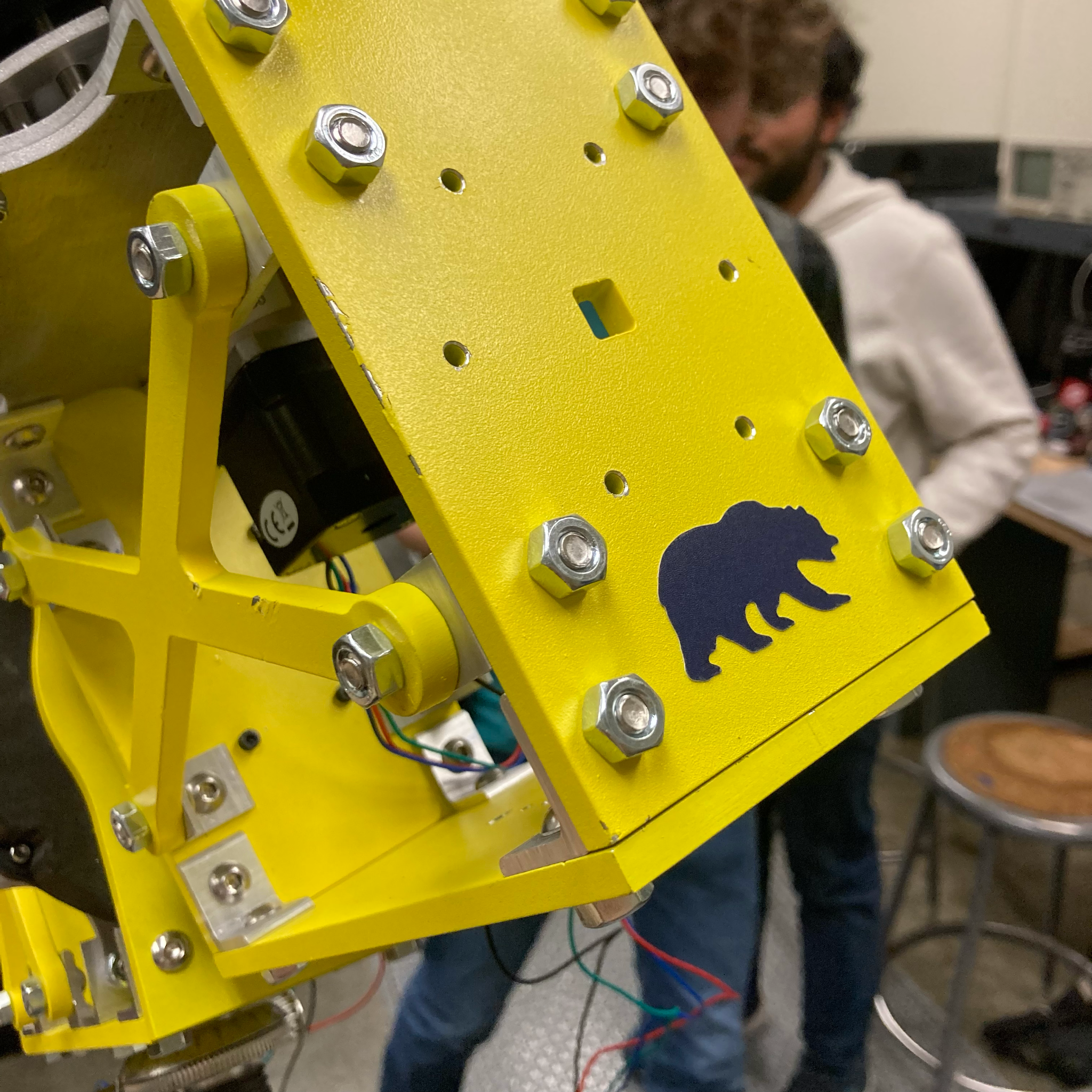
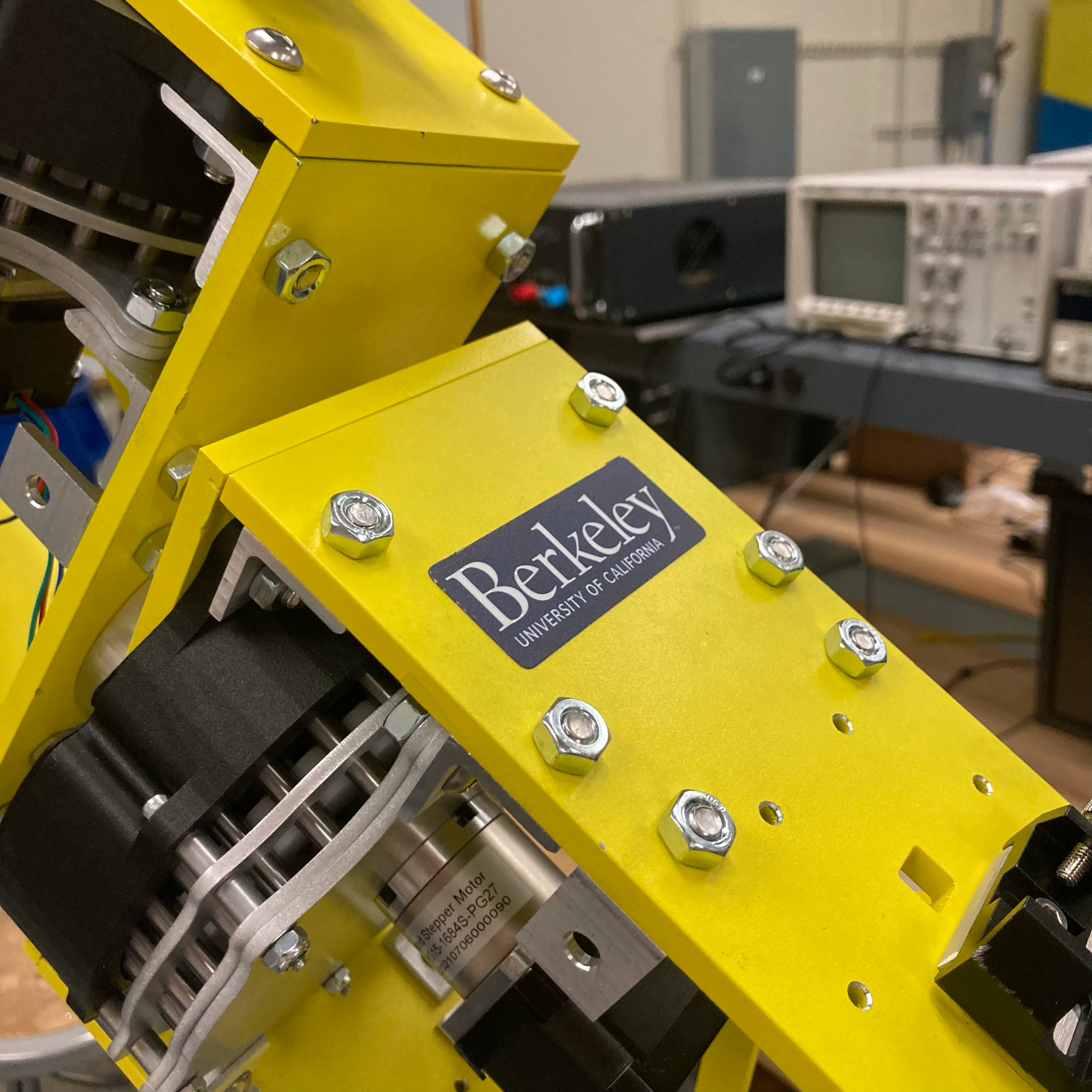
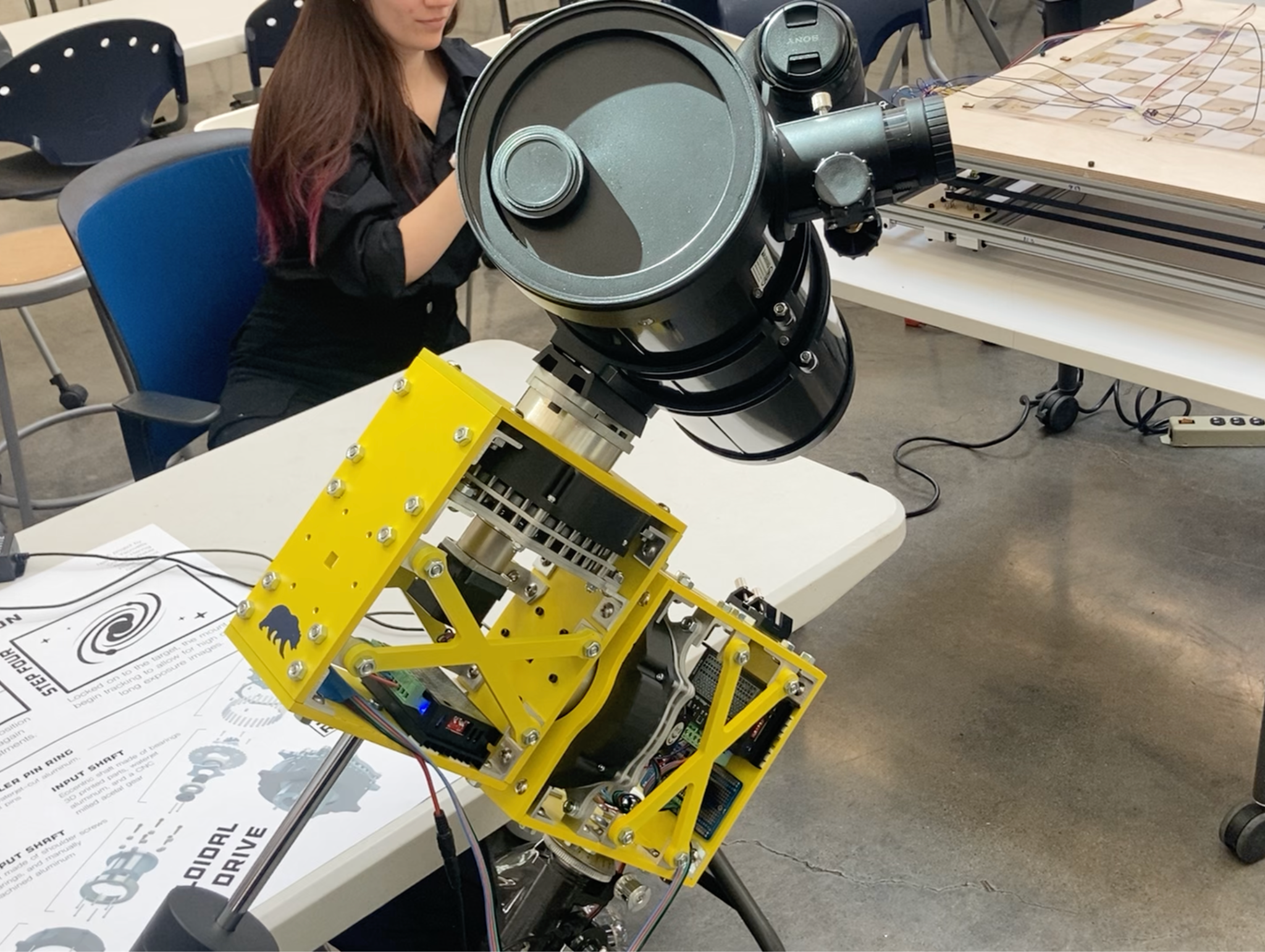
Testing and Results
Unfortunately, we do not have any long-exposure images to show off for all the work we put into this project. To reliably test this telescope we spent multiple nights up until 5 am on the roof of a building near campus and one night three hours outside of campus to remove light pollution from the environment. We quickly learned that astrophotography is a challenging skill of its own even if you have an advanced telescope mount. There is a lot of calibration involved each time the telescope and mount are set up. It is also extremely difficult to debug issues because there is no real way to tell if the problem is mechanical or software-related due to how small the expected movements are. We were also trying to fix these issues while sitting outside in the cold all night. With all that being said, we still had a blast building this project and testing it. It gave us a great excuse to travel to a rural area and see a phenomenal starry sky. Below are some pictures of our nights out testing, the video of the mount functioning, and the poster I made for presenting.
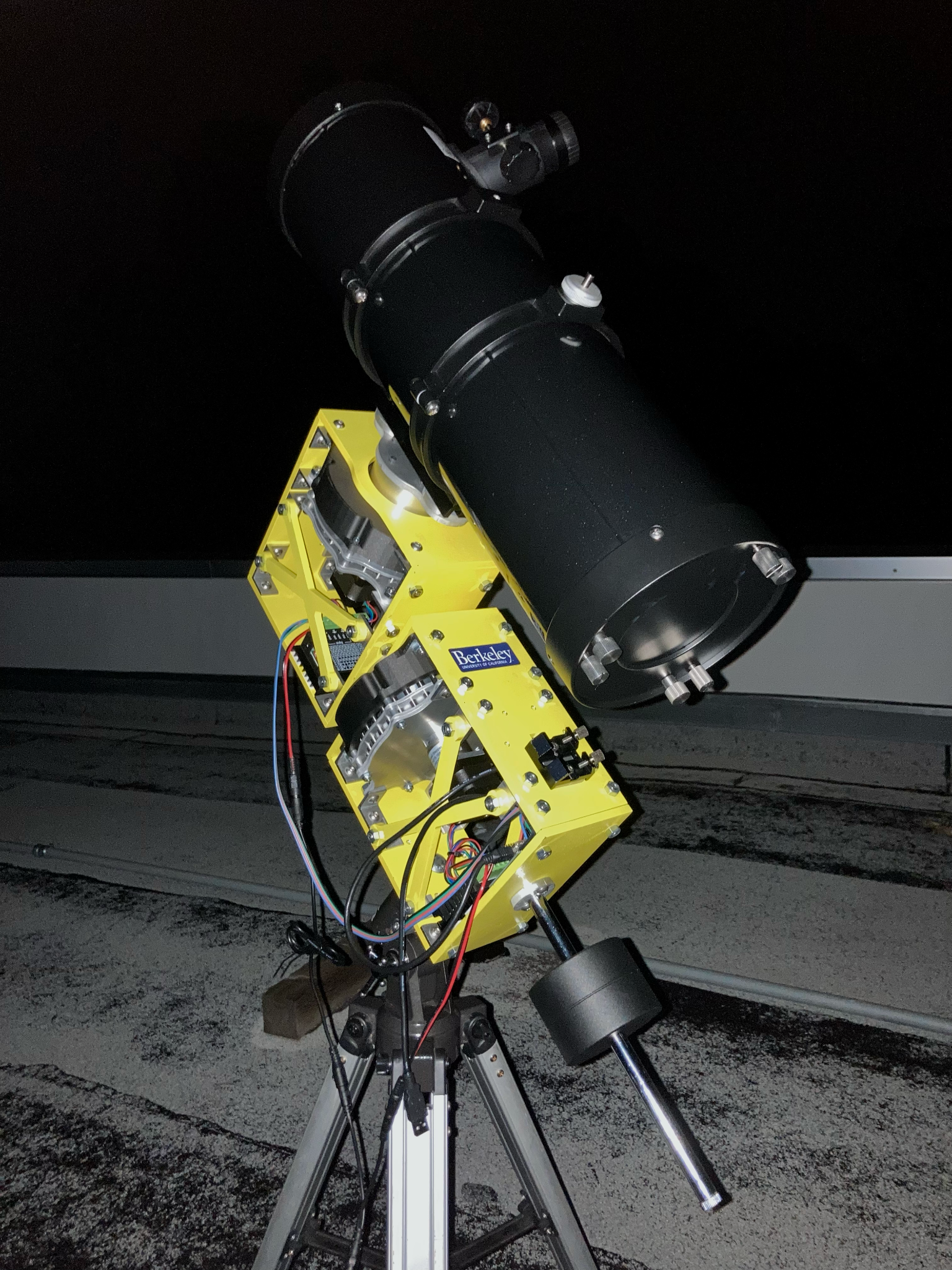
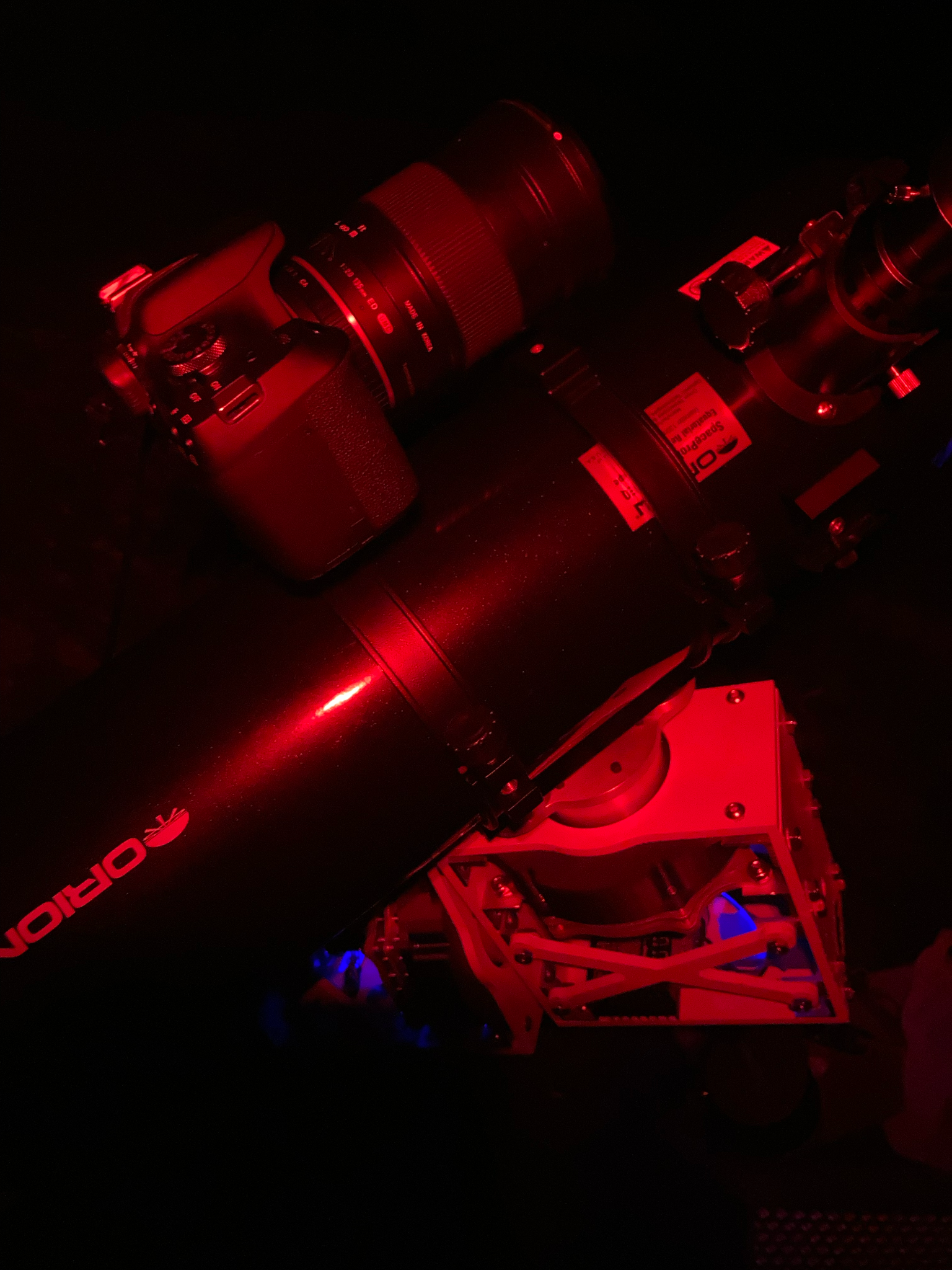
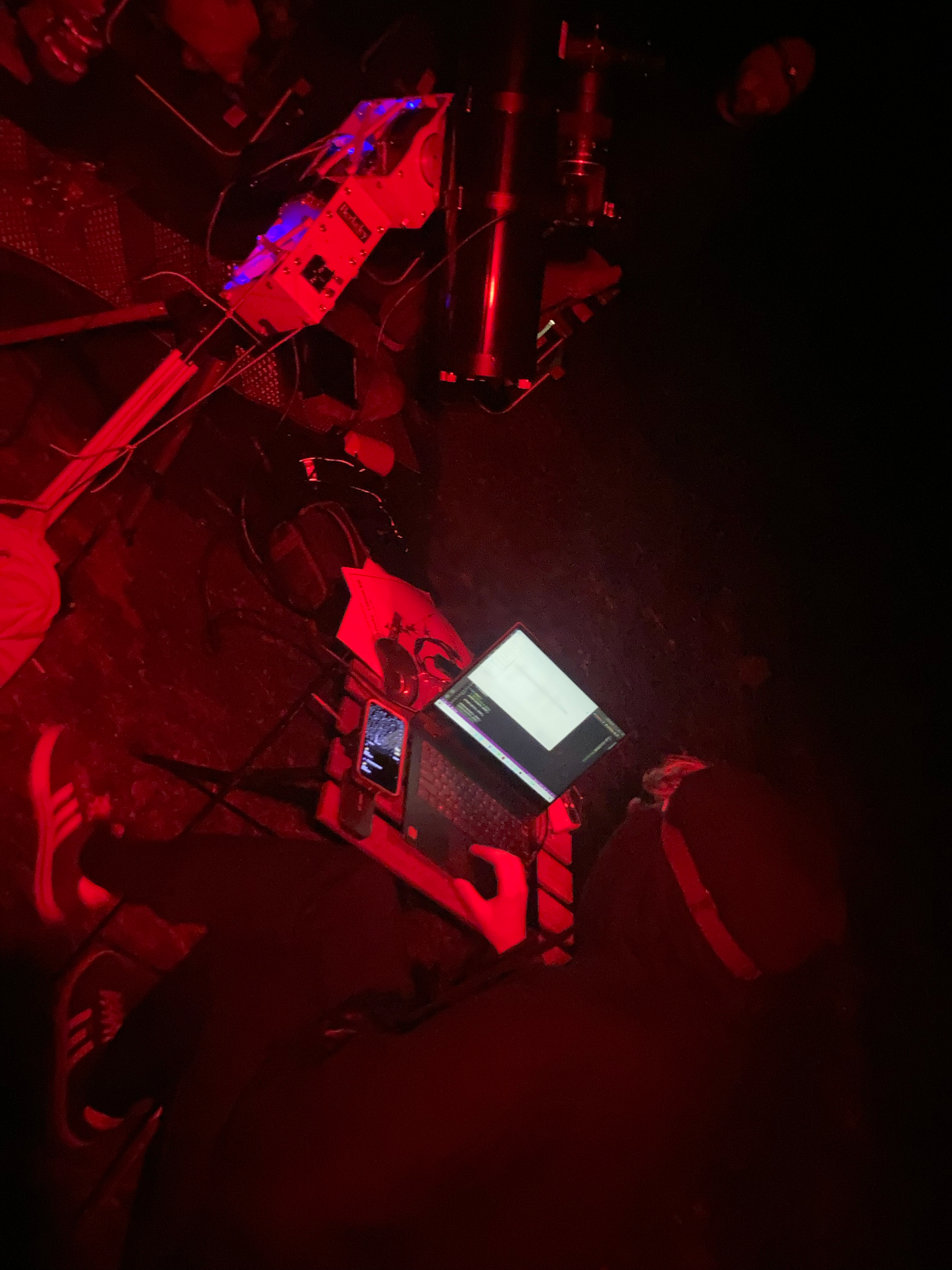

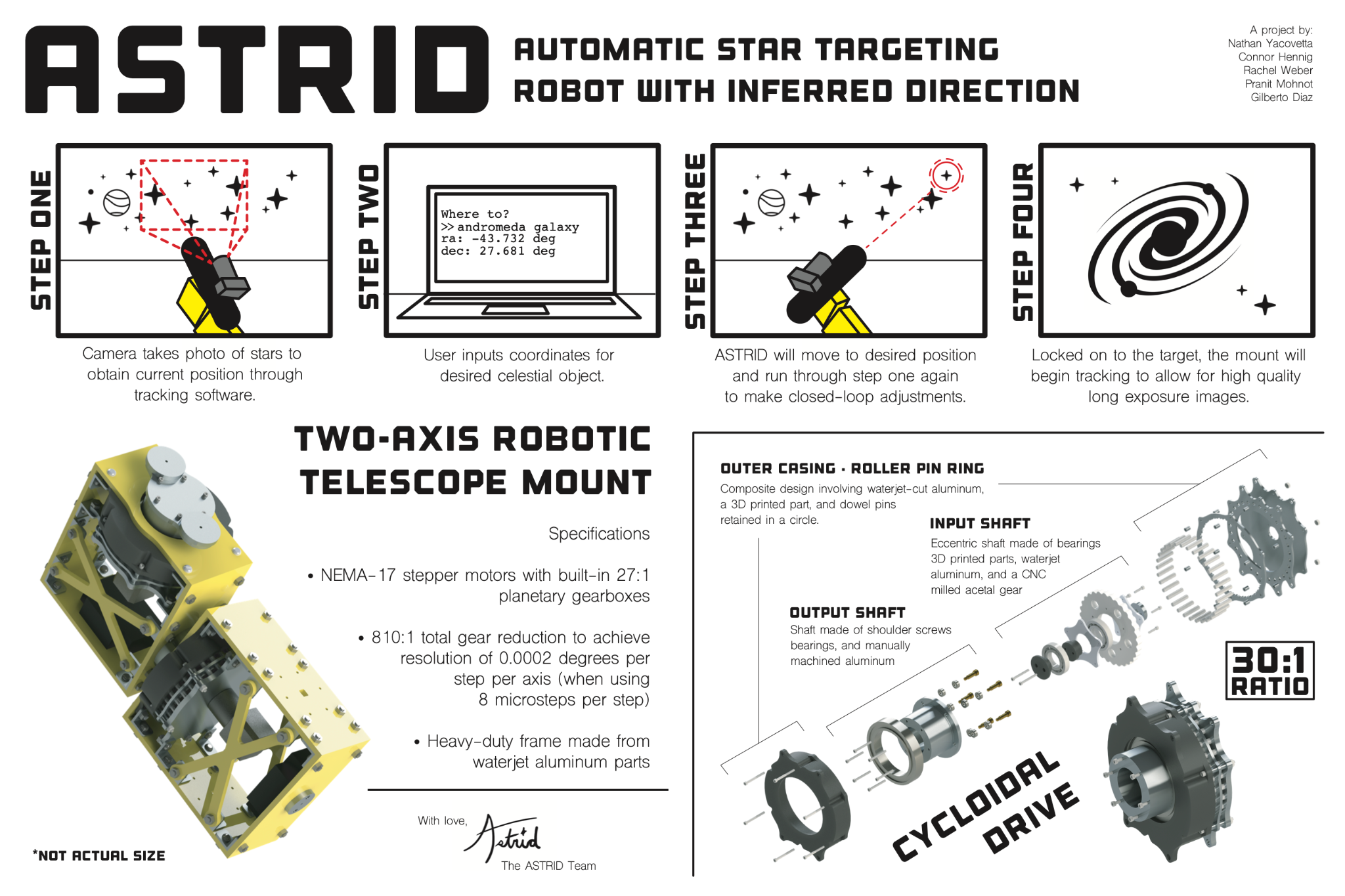