Personal Fitness Cable System
At-home personal fitness cable machines on the market are either expensive, bulky, or use elastic bands. In my product development course, my team decided to change that. We designed and built a cable system that could be temporarily secured to a door frame, offer resistance from 5-45 lbs at 5 lb increments, and provide "free weight" resistance accomplished with constant force springs, all in one small package. An additional bar with a pulley is added to achieve different cable angles.
In this project, my role was fabricating the entire cable system and helping in the design.
Below are some sketches of initial brainstorming, initial CAD designs, and our final CAD design.
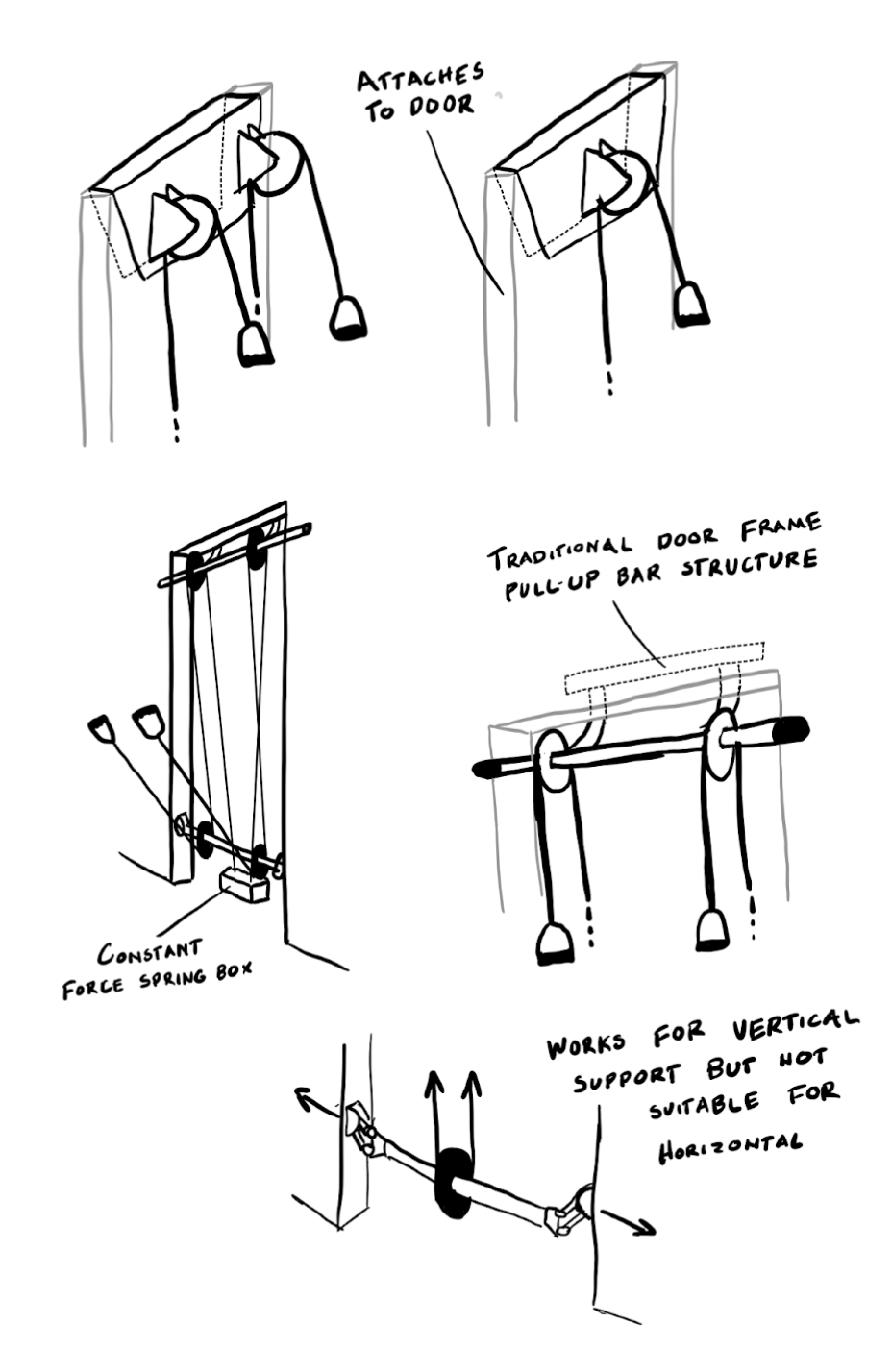

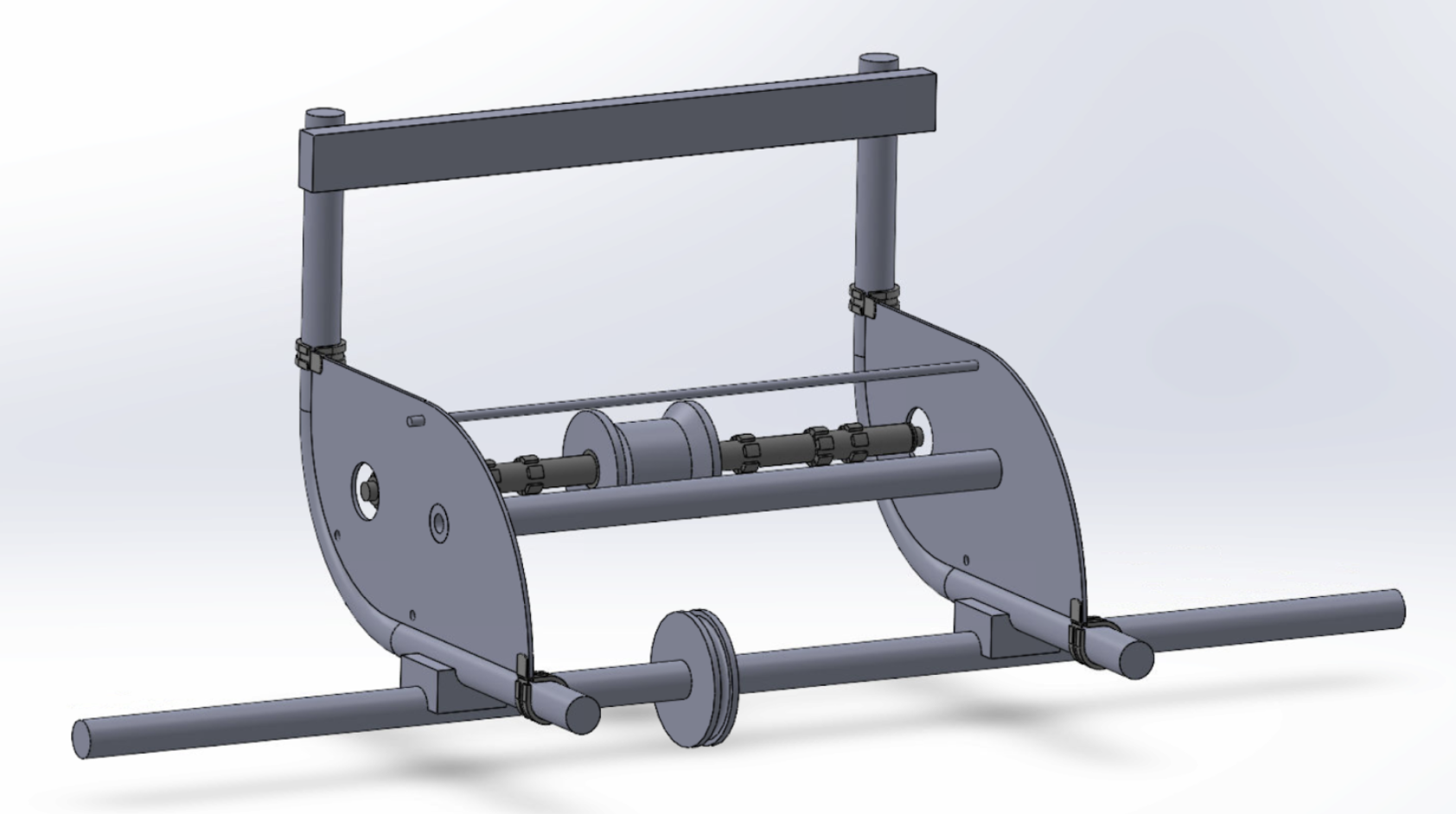
Below you can see four constant force springs (the steel band spools), one is 5 lbs of resistance, two are 10 lbs, and the last is 20 lbs. Each constant force spring is attached to a drum, which has internal teeth that interface with external teeth on the shaft connected to the cable. These drums can slide laterally to be engaged or disengaged with teeth on the shaft to either apply or disengage the spring force. Different combinations of these constant force springs can be chosen to achieve the desired weight.
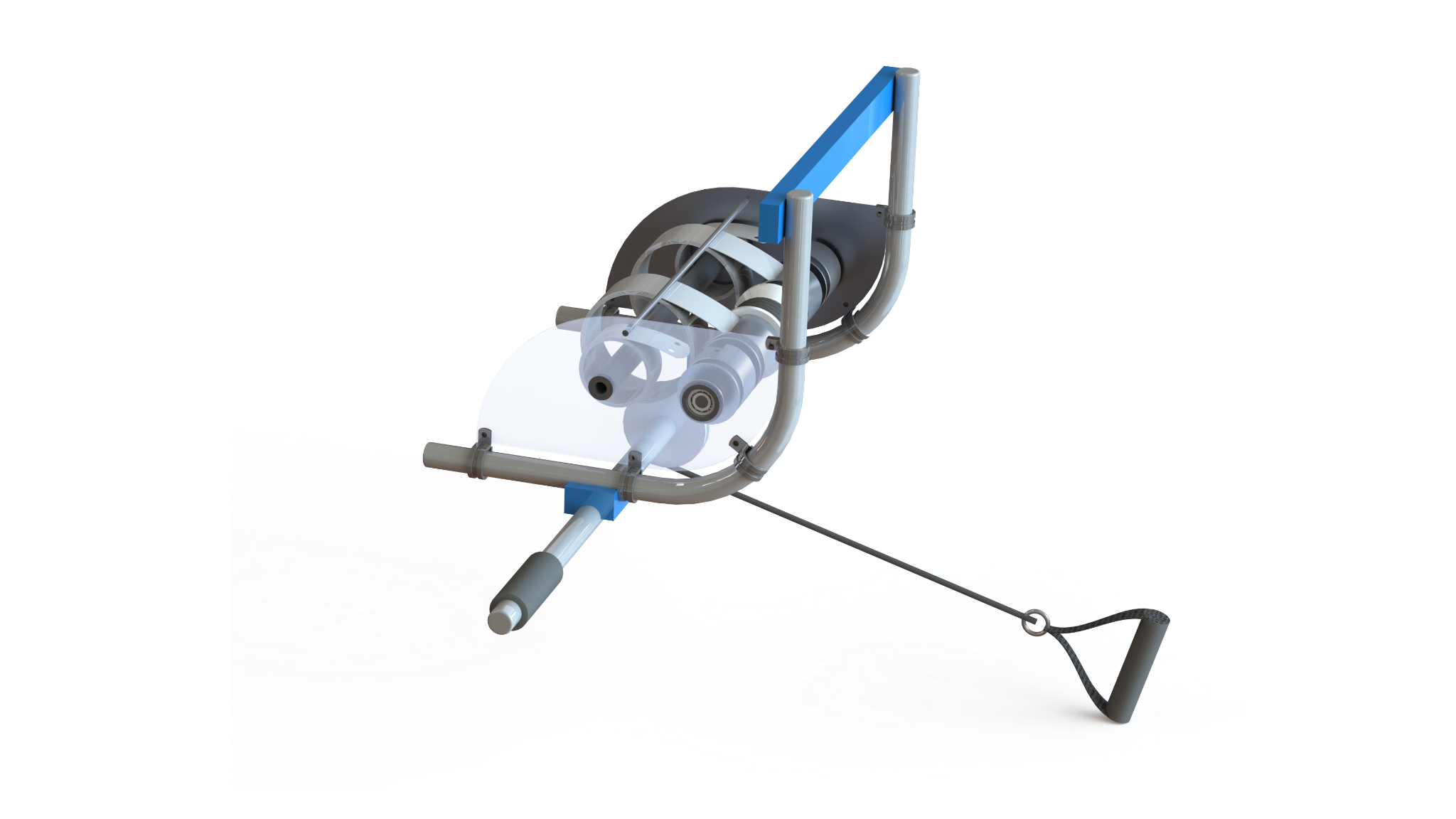
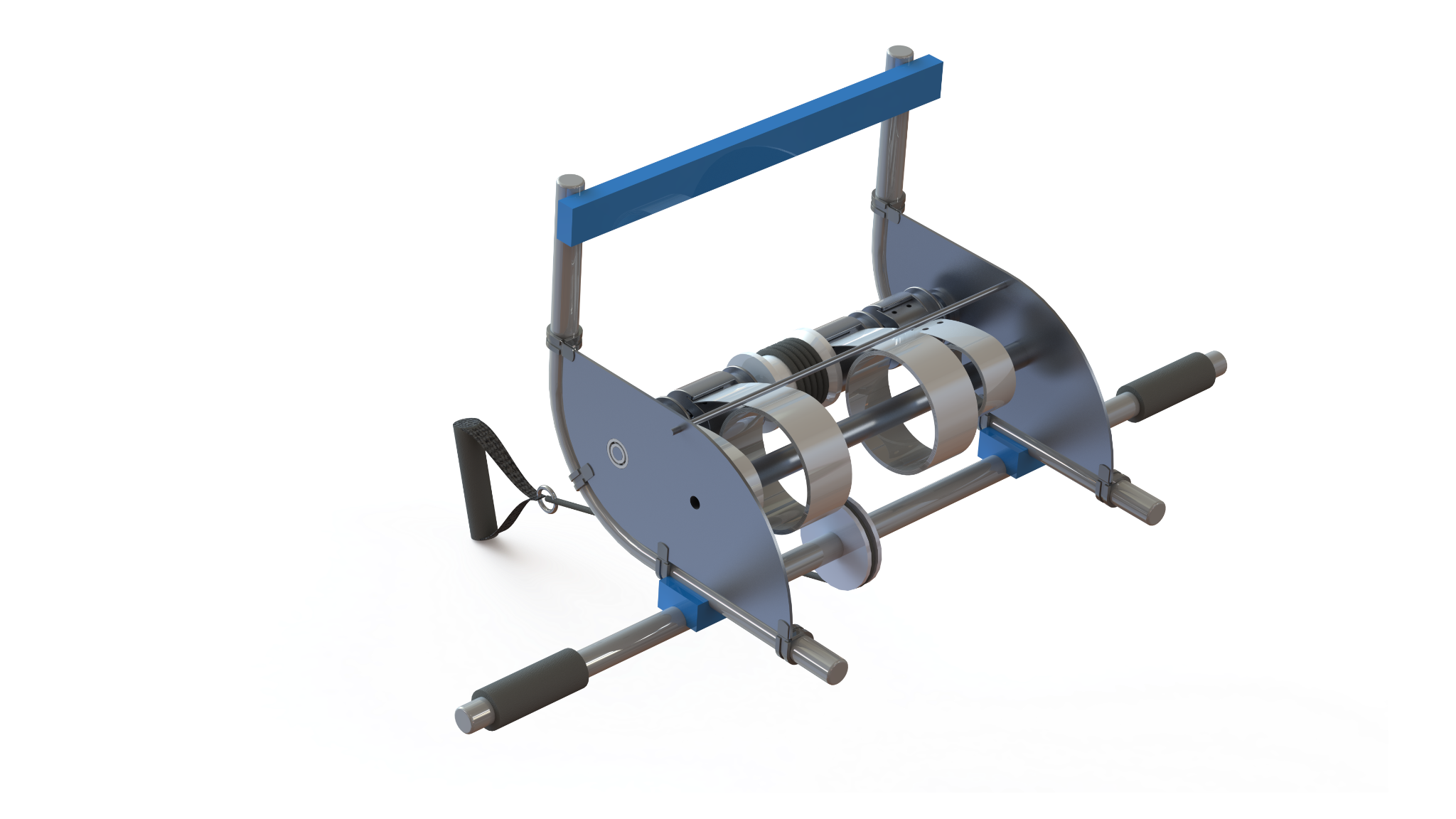
The base structure of this prototype was designed around a standard door-mounted pull-up bar. We were able to find a pull-up bar at a thrift store which also had perfect brackets for mounting the bottom pulley bar.
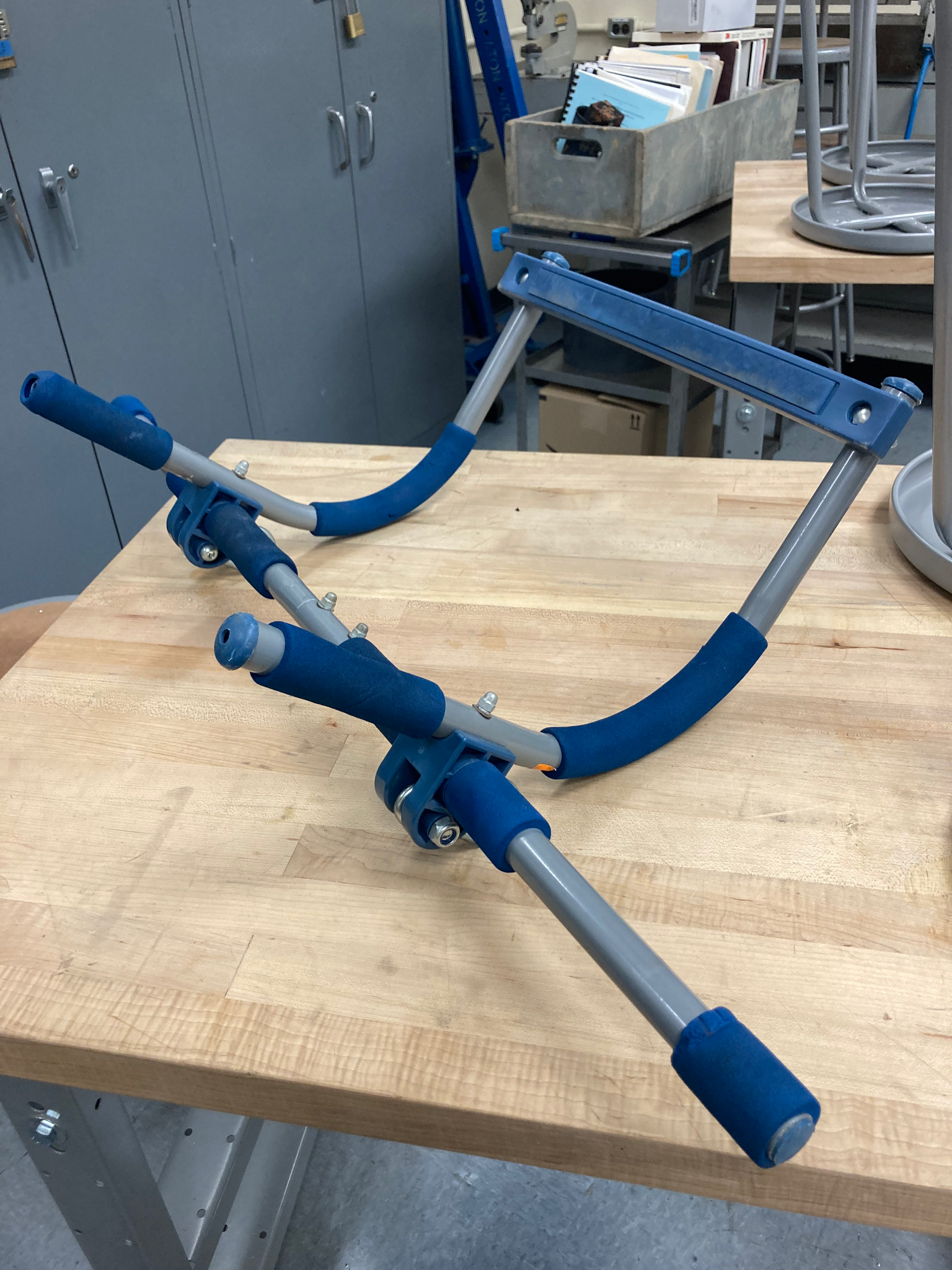
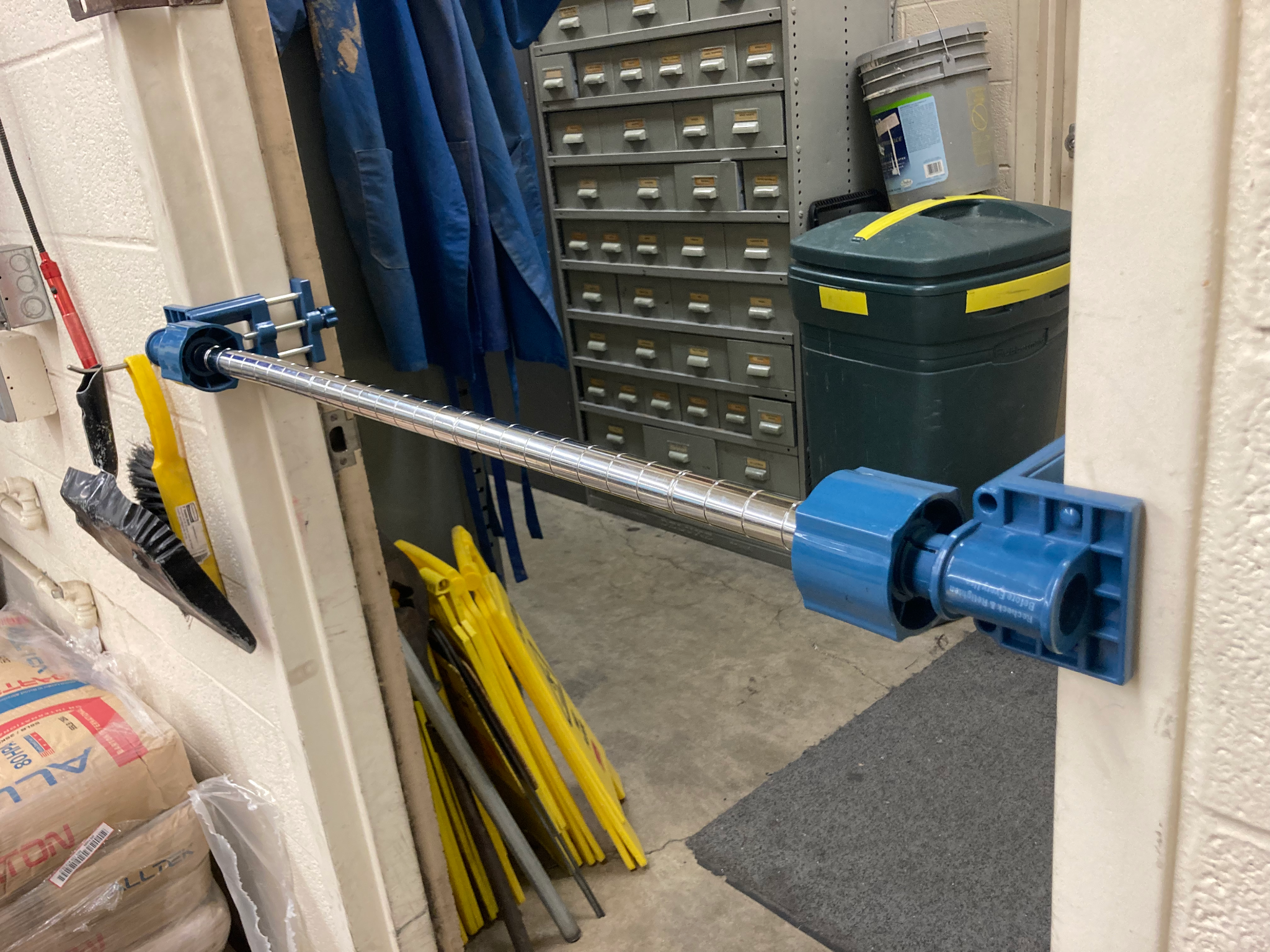
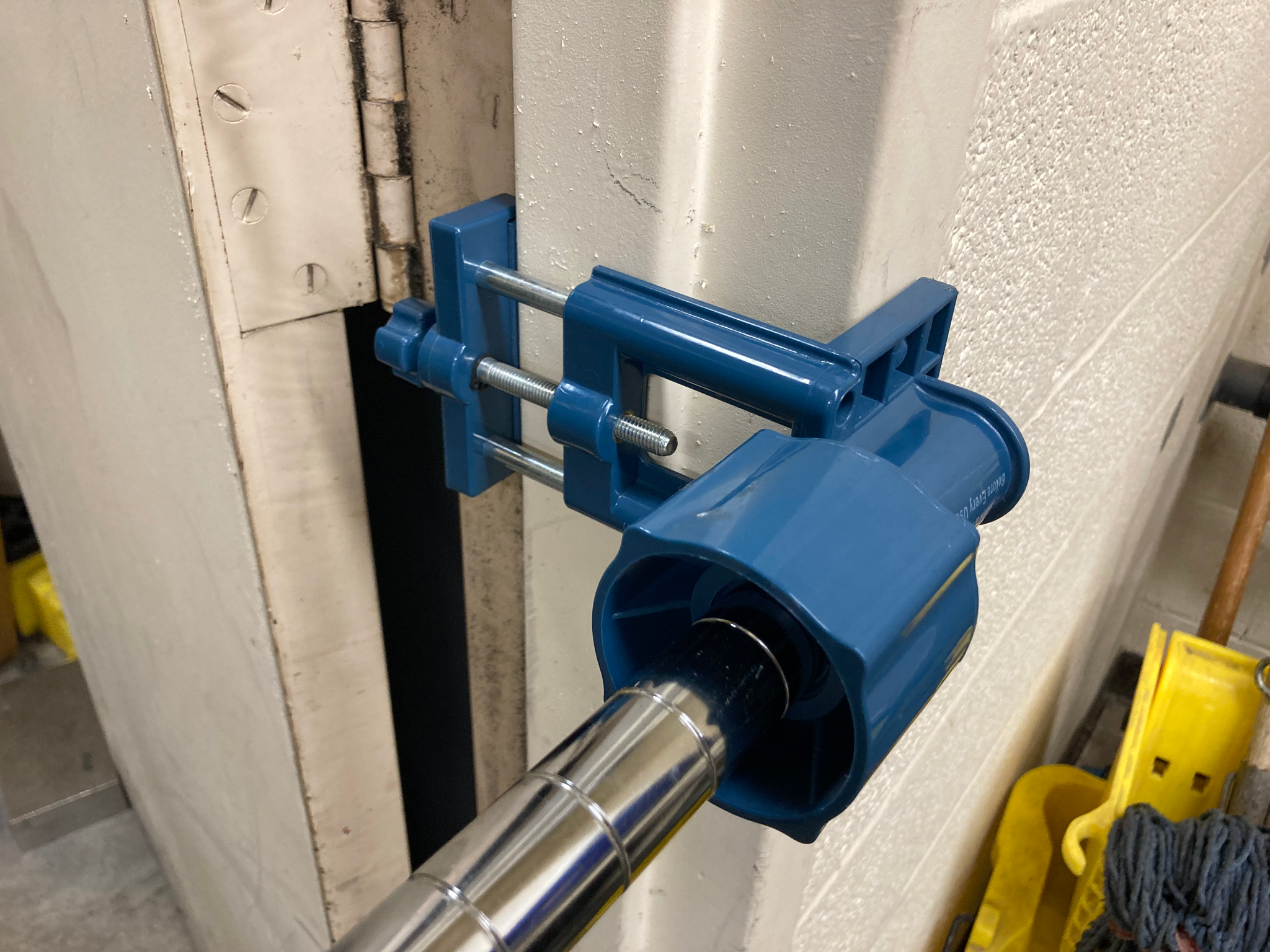
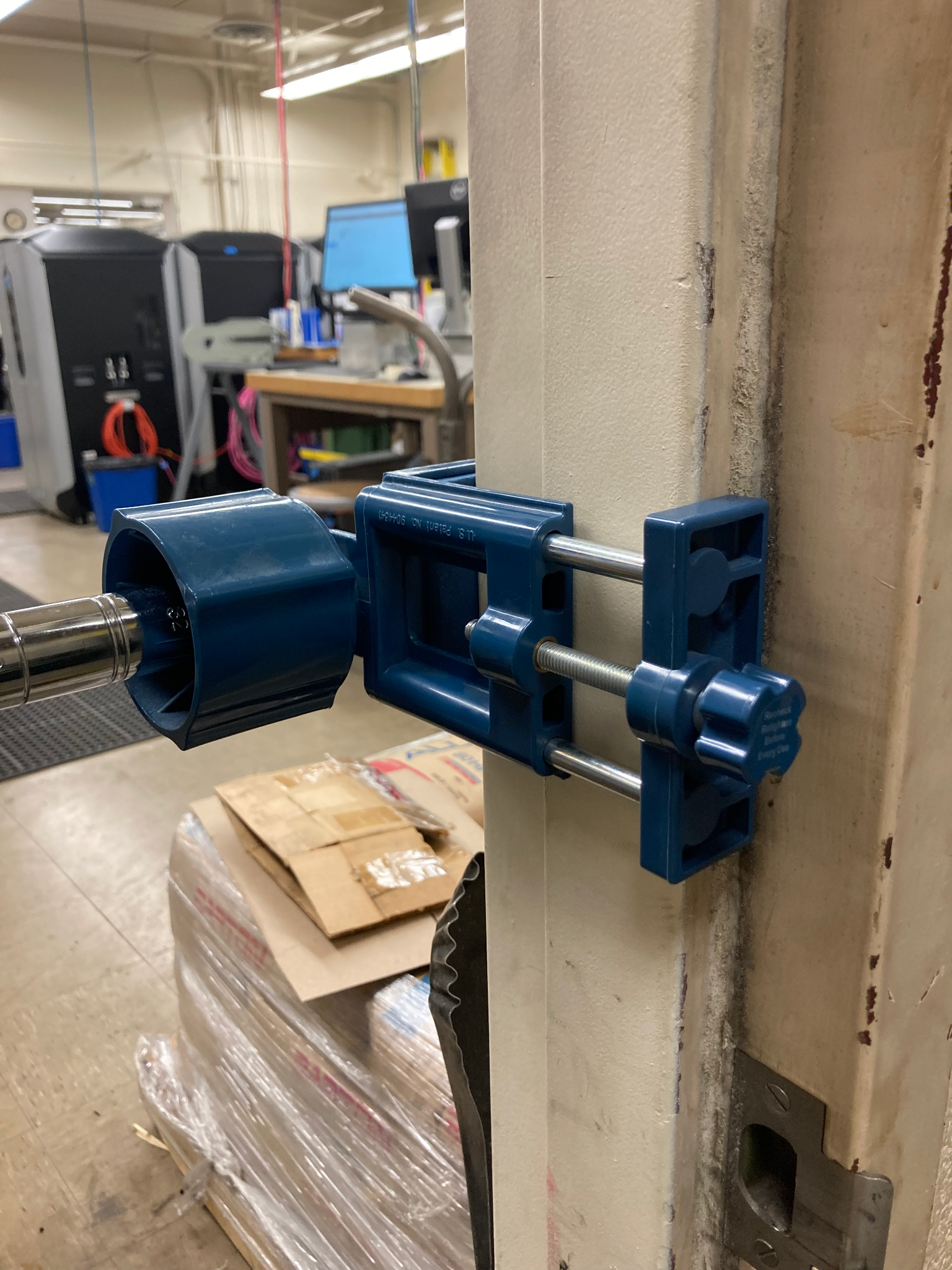
With the design made and the base of the build found, we can start fabrication. Because this was one of my first fabrication projects, I did not think to take more pictures of my manufacturing processes, but here are some of the parts. The cable spool was machined from acetal, the spring drums with internal teeth were 3D printed, and the pulleys, toothed shaft, and other miscellaneous parts were machined from aluminum.
Machined Acetal Spool for Cable
3D Printed Internal-toothed Drum for Springs
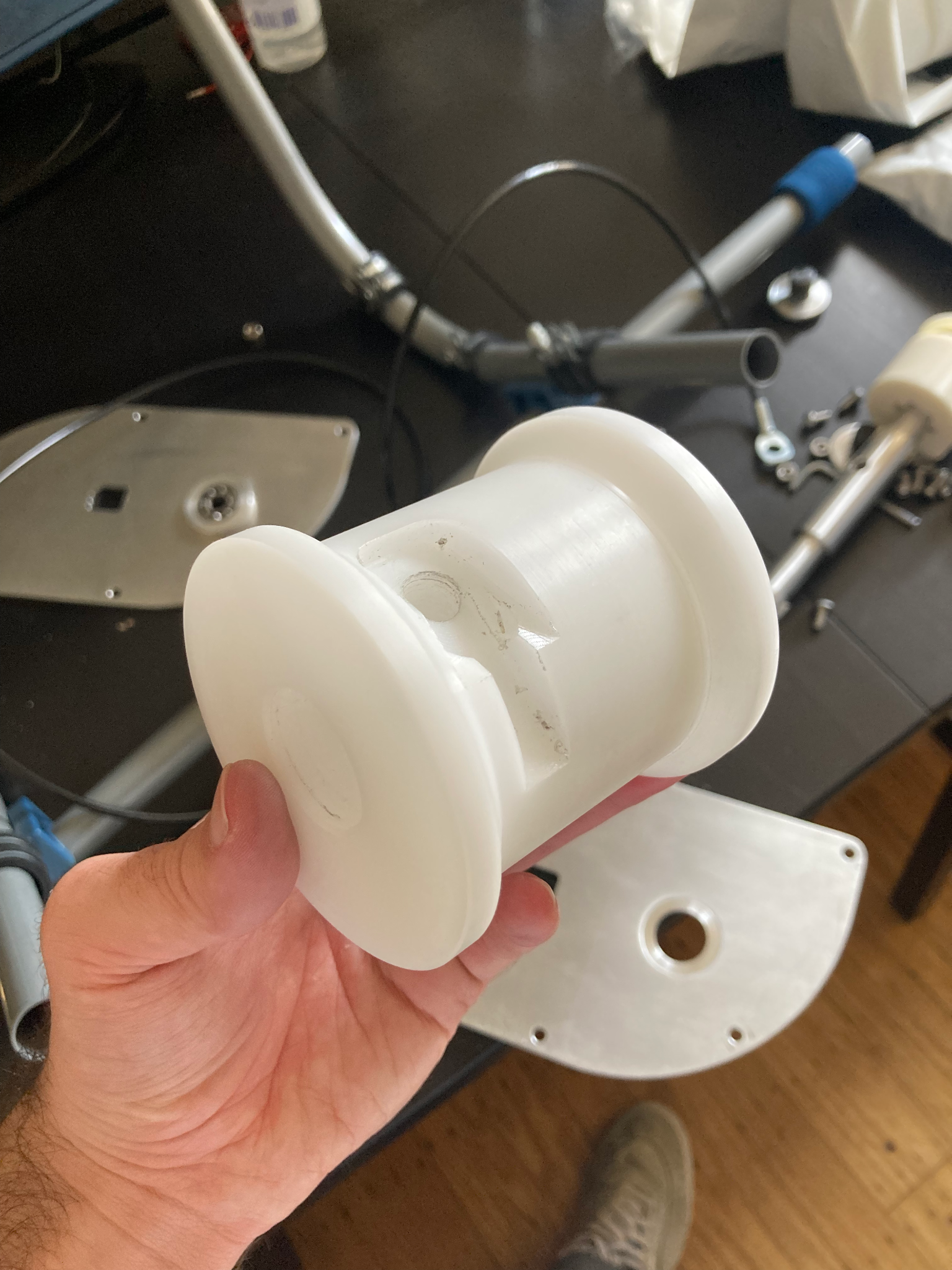
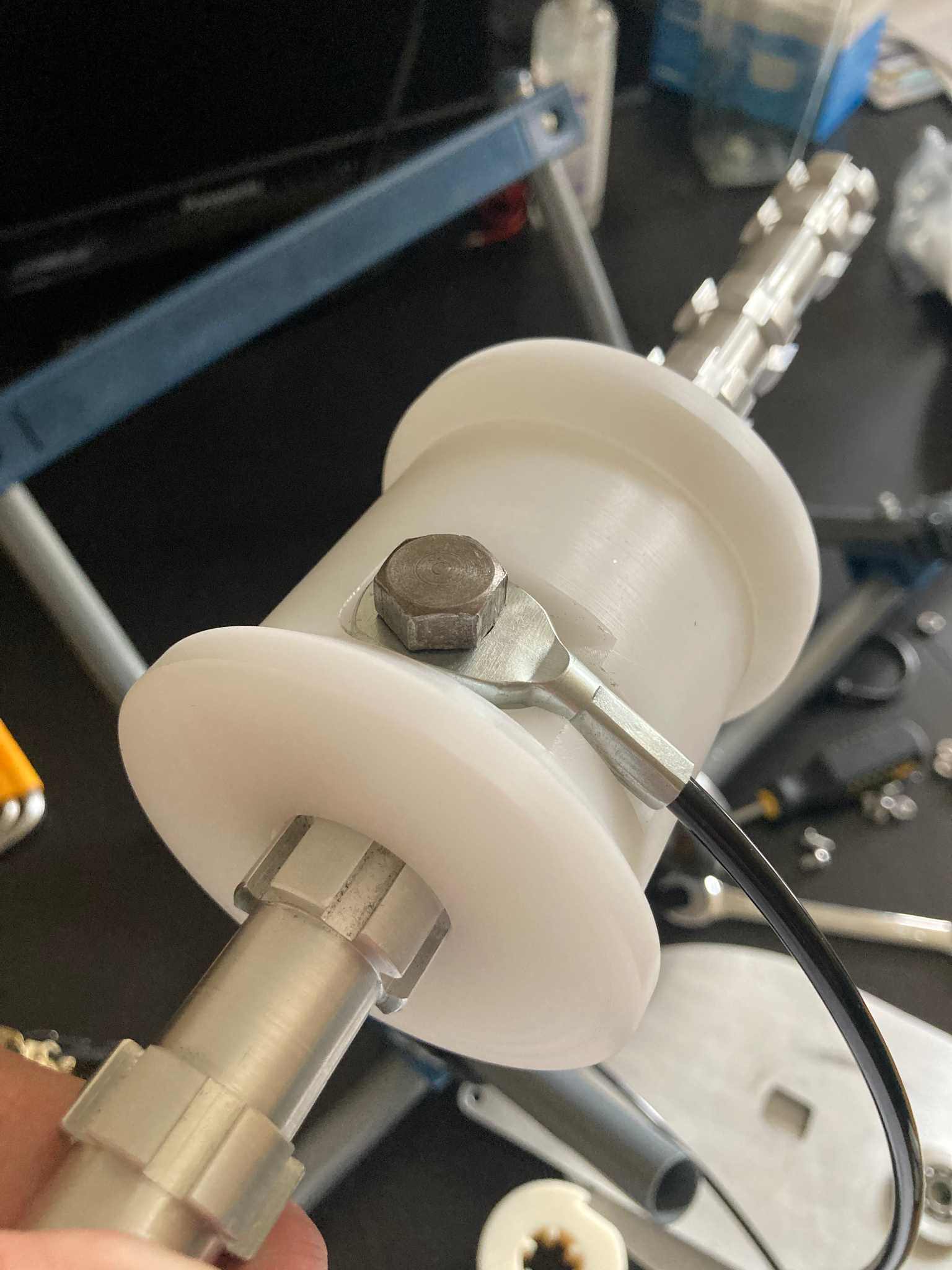
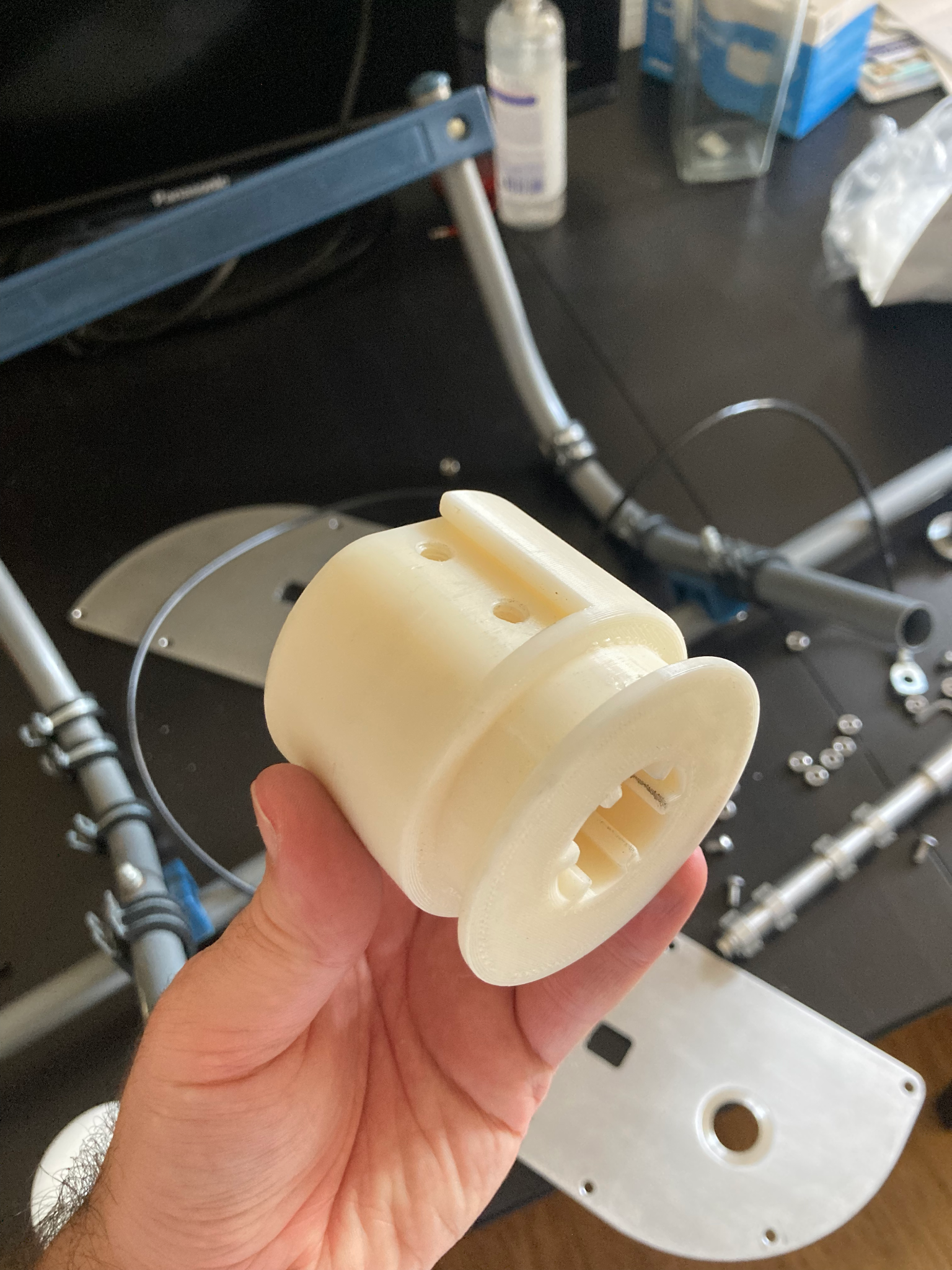
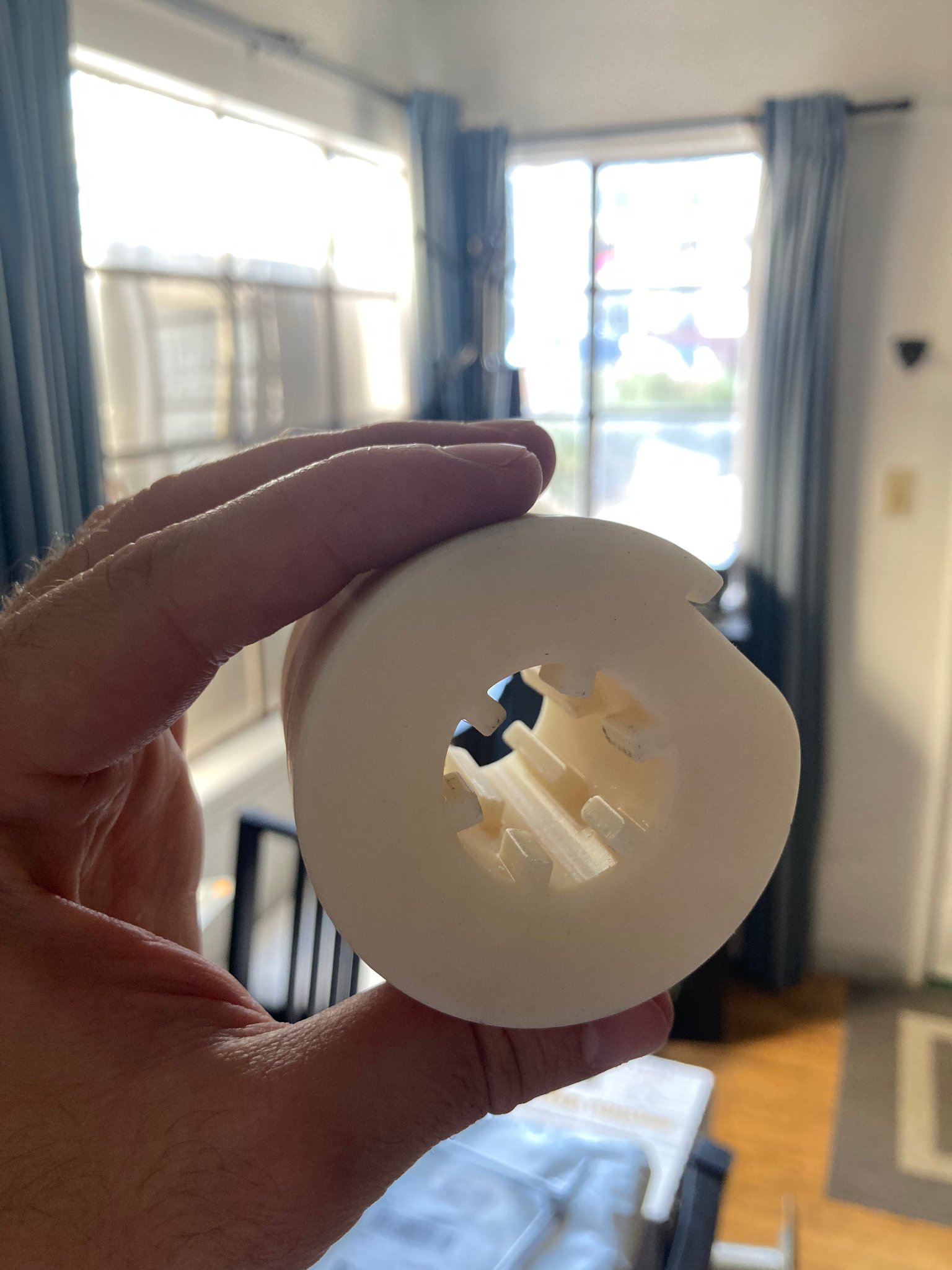
Milled Aluminum Slotted Brackets
Turned Aluminum Pulleys
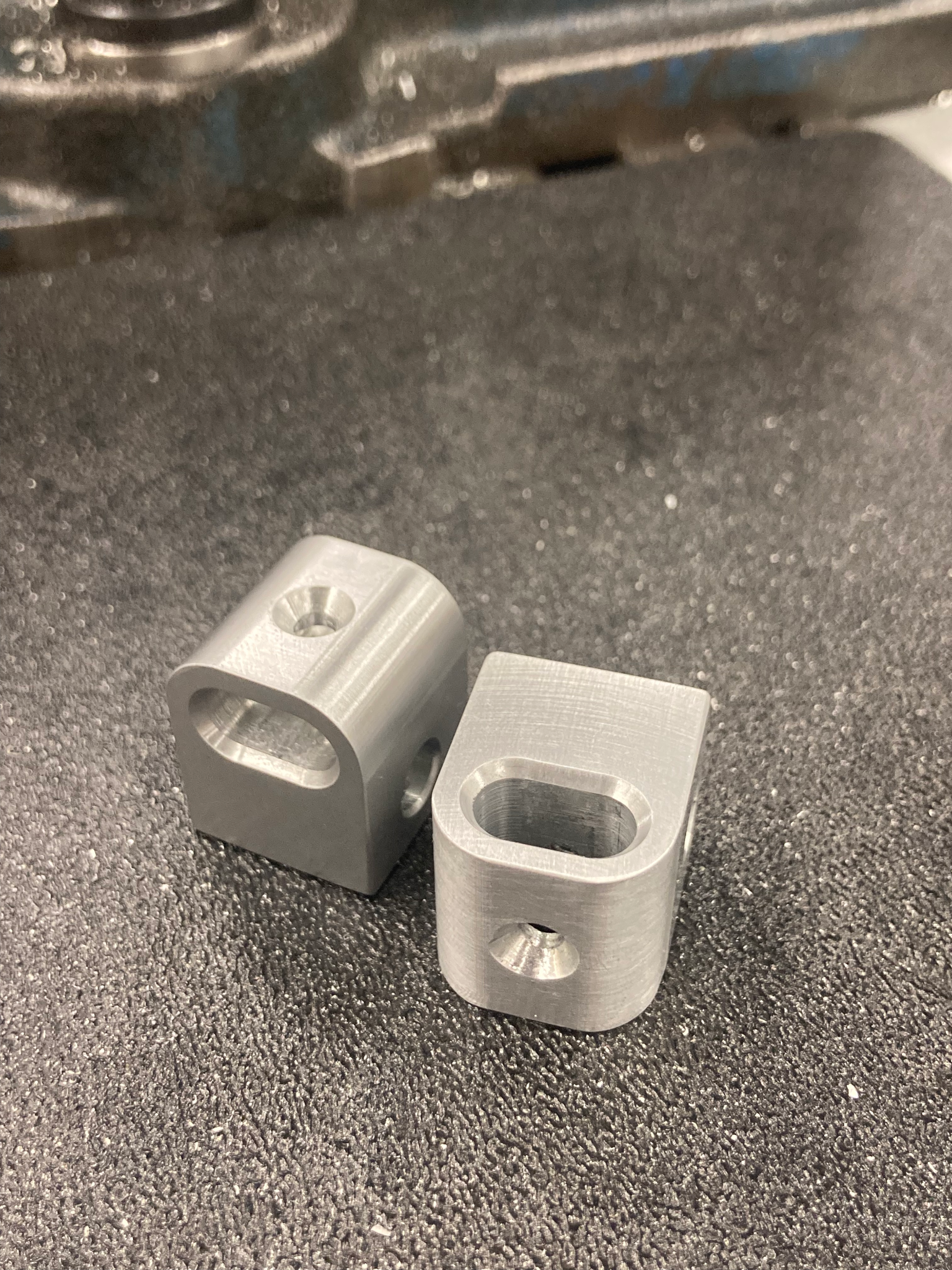
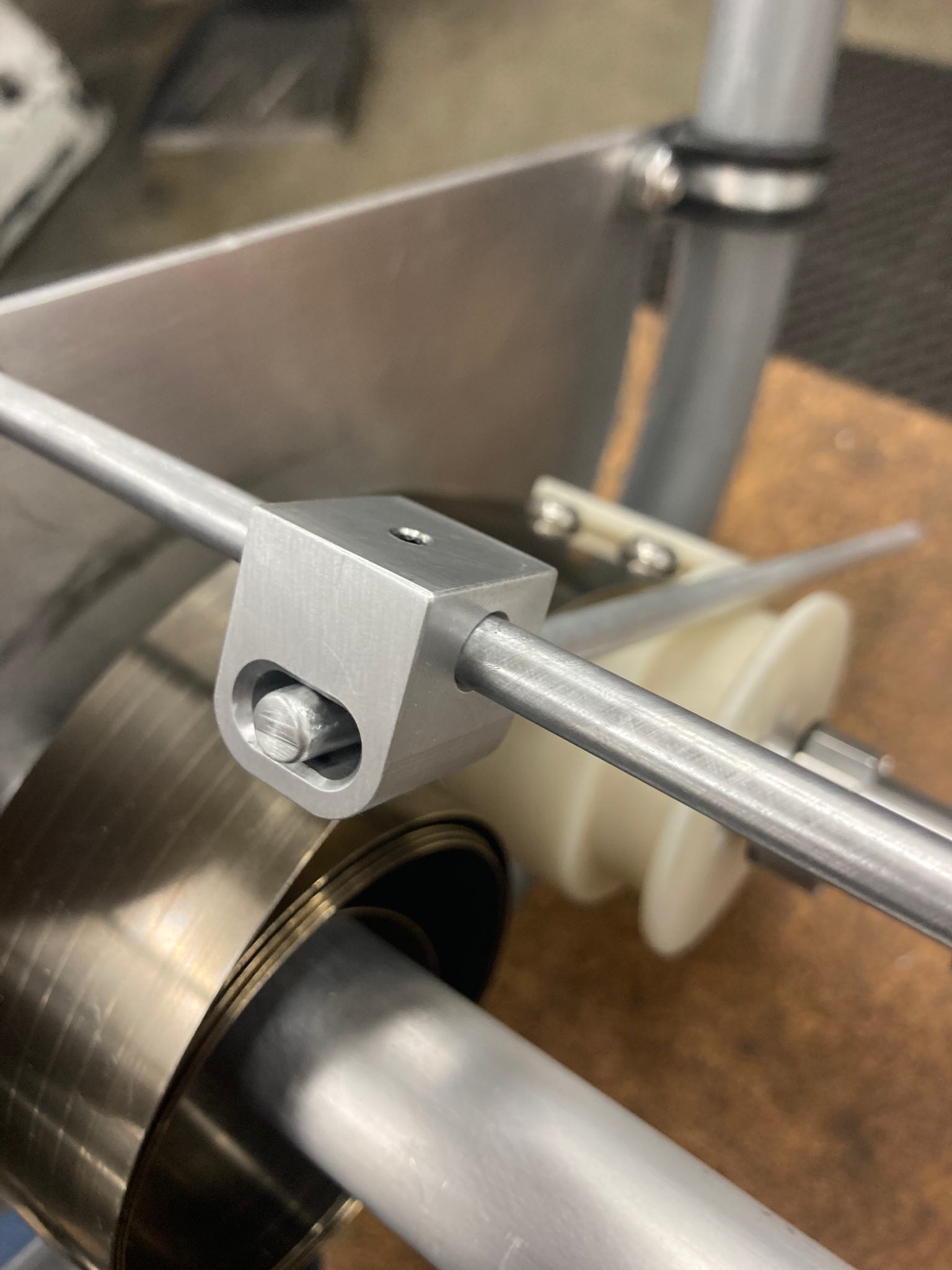
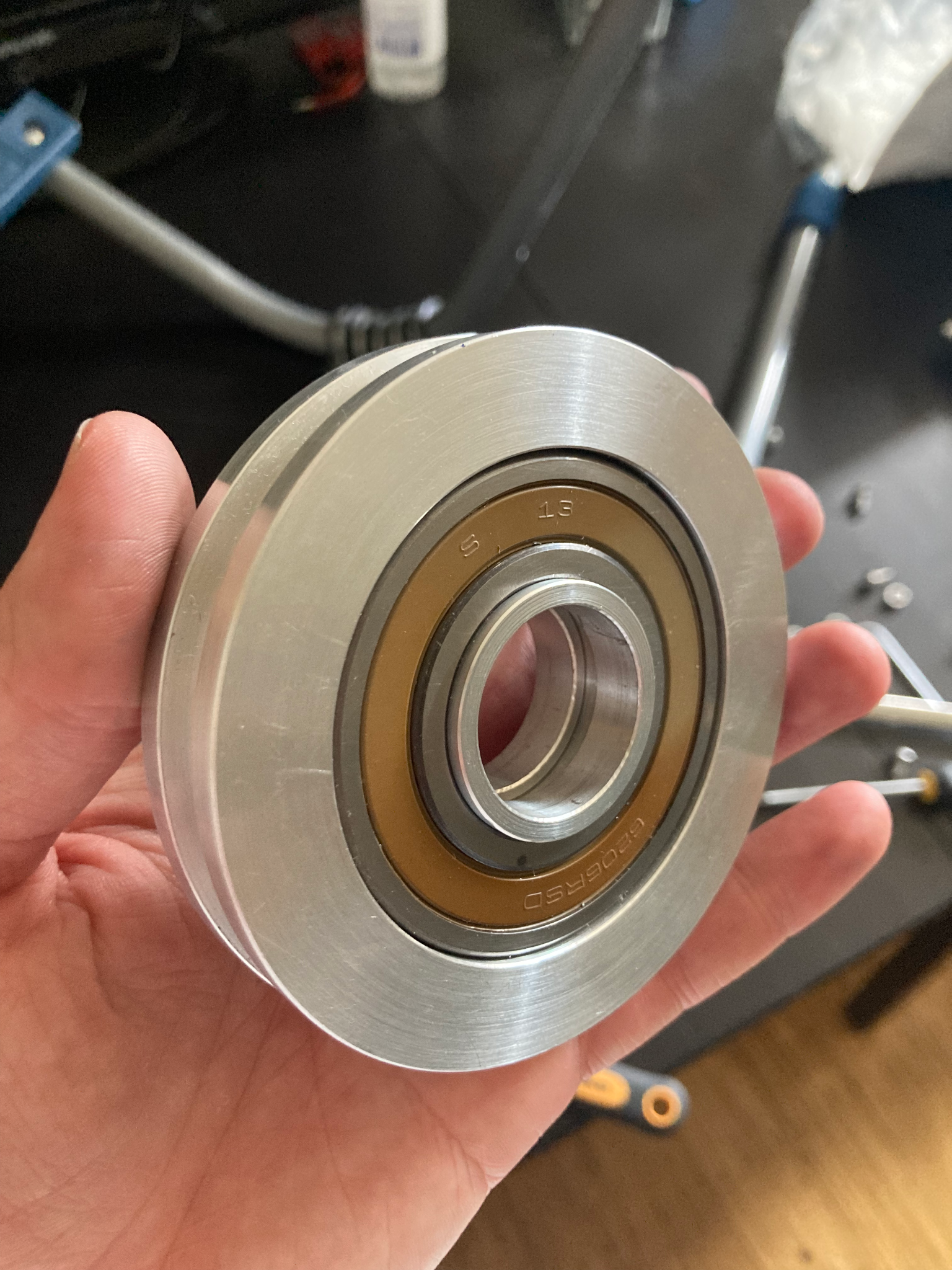
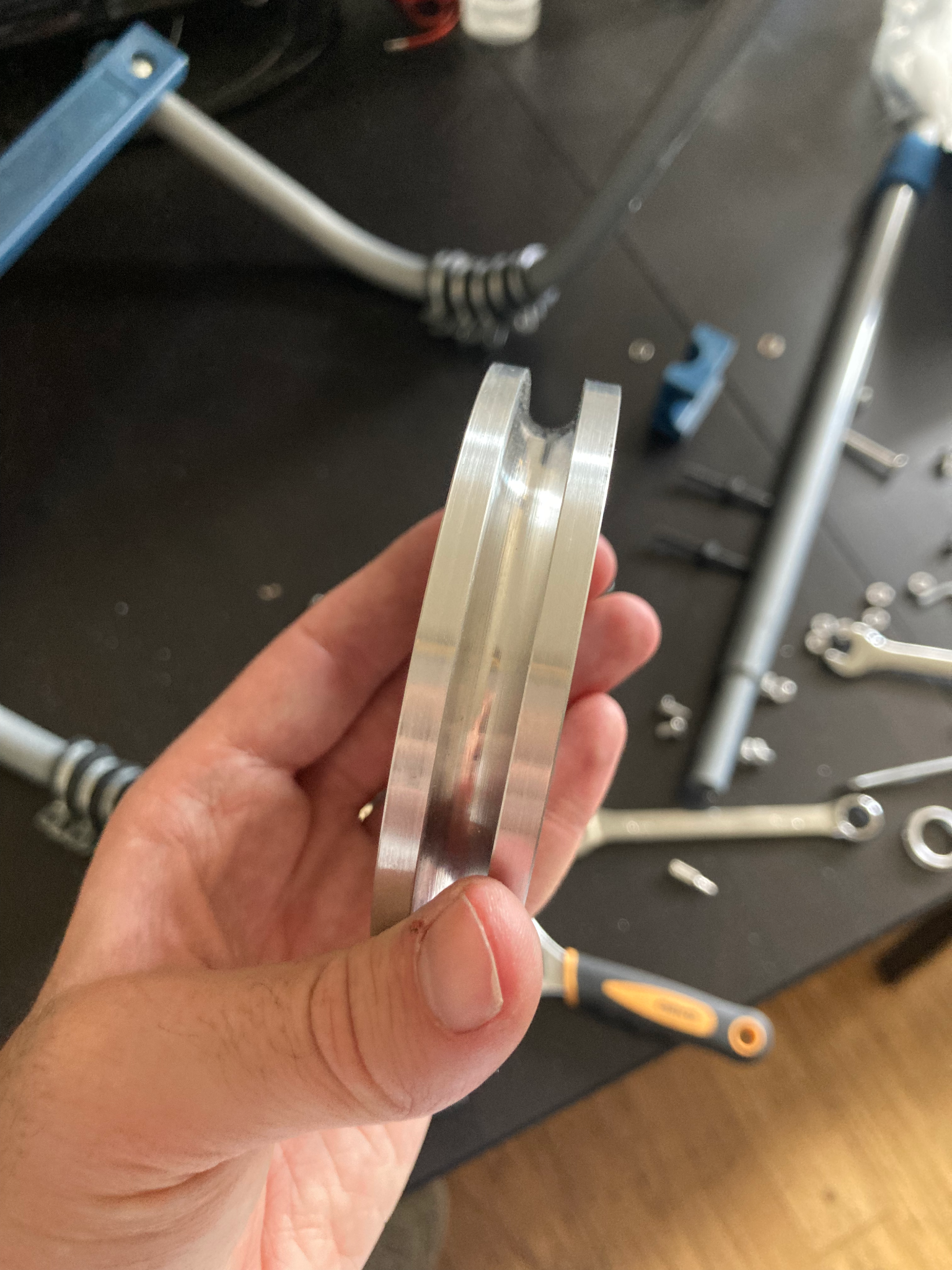
Aluminum Side Plates with Machined Bearing Sleeves
Machined Aluminum Shaft with Spline Segments
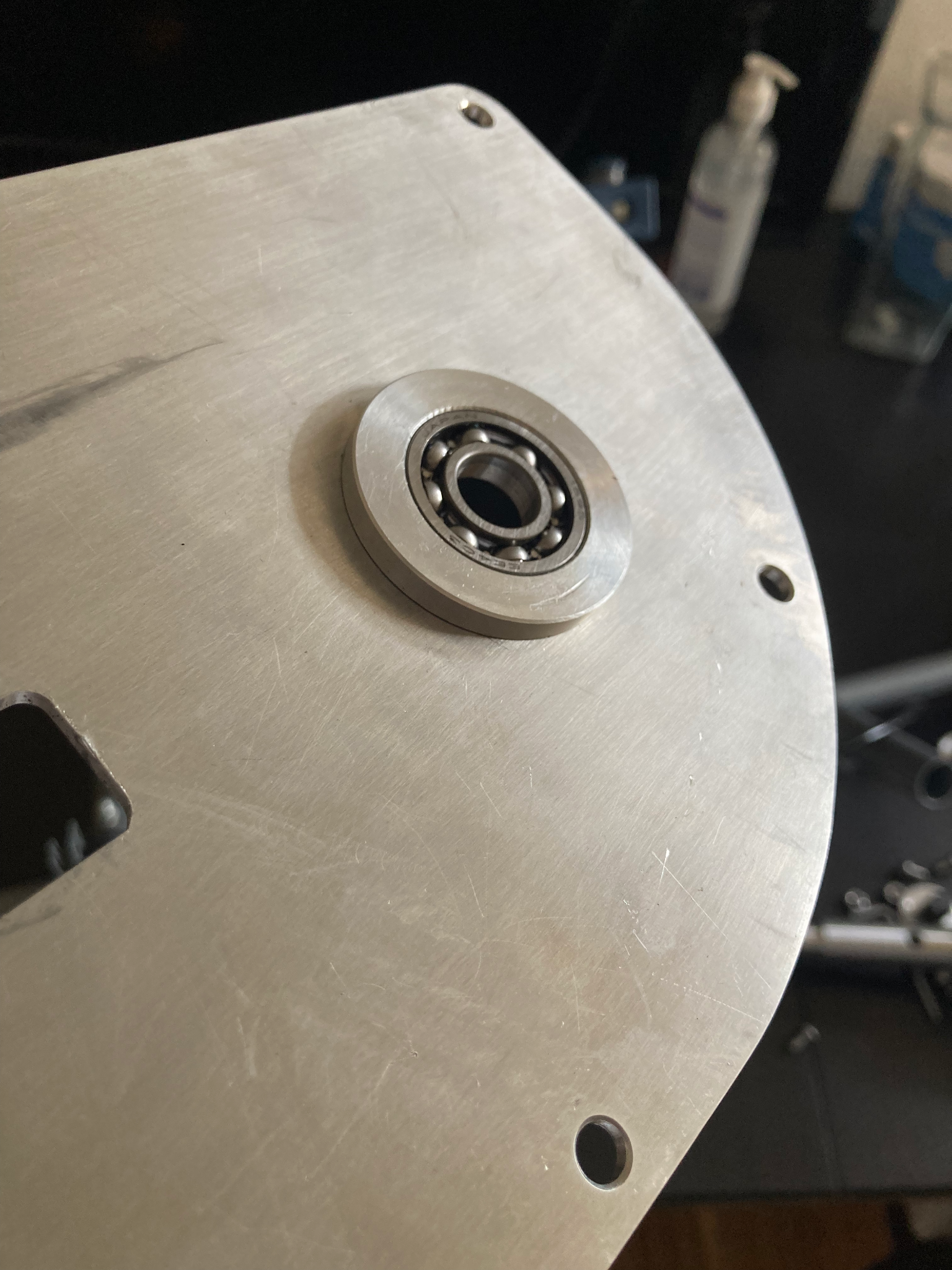
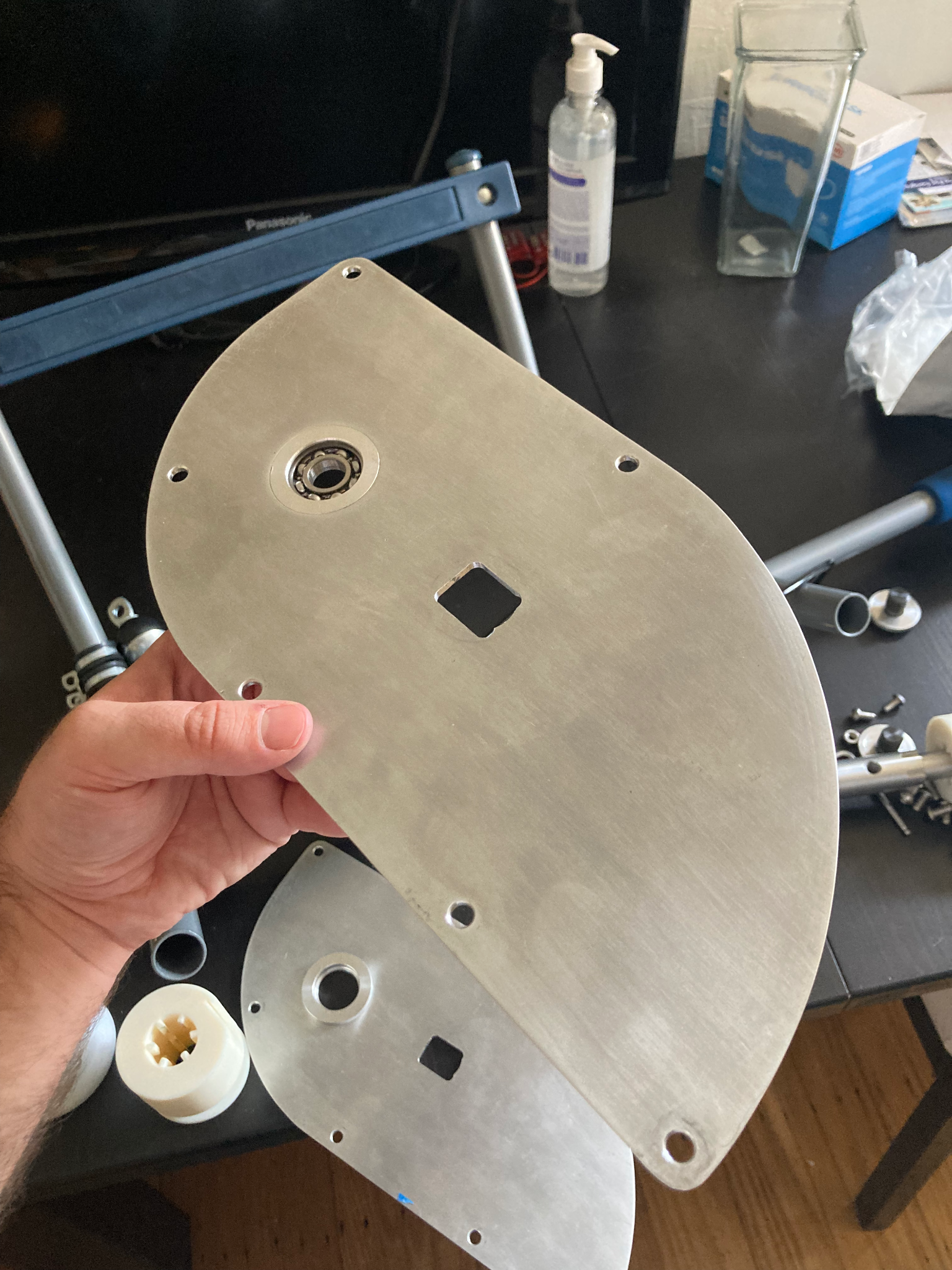
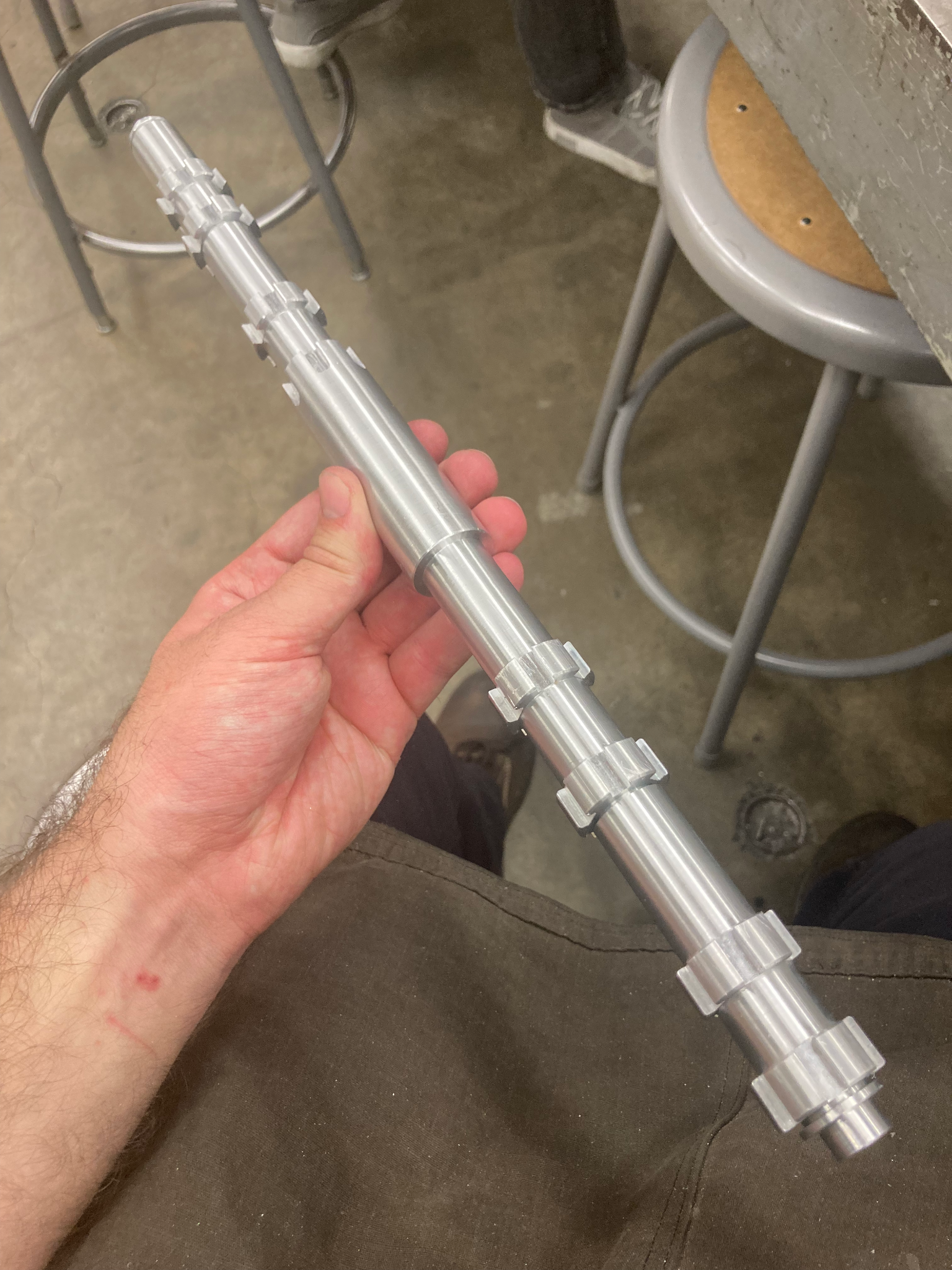
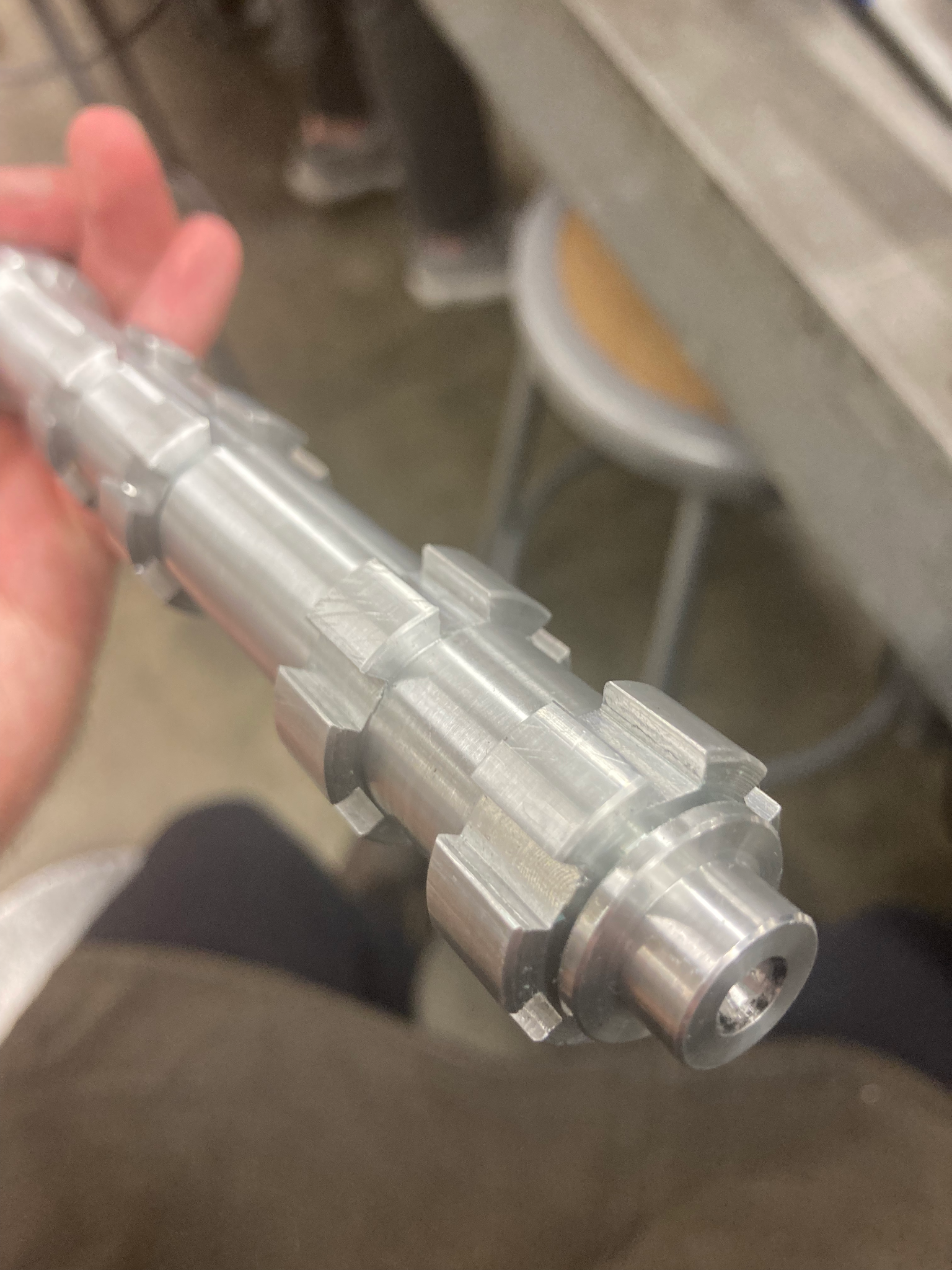
Here it is all put together!
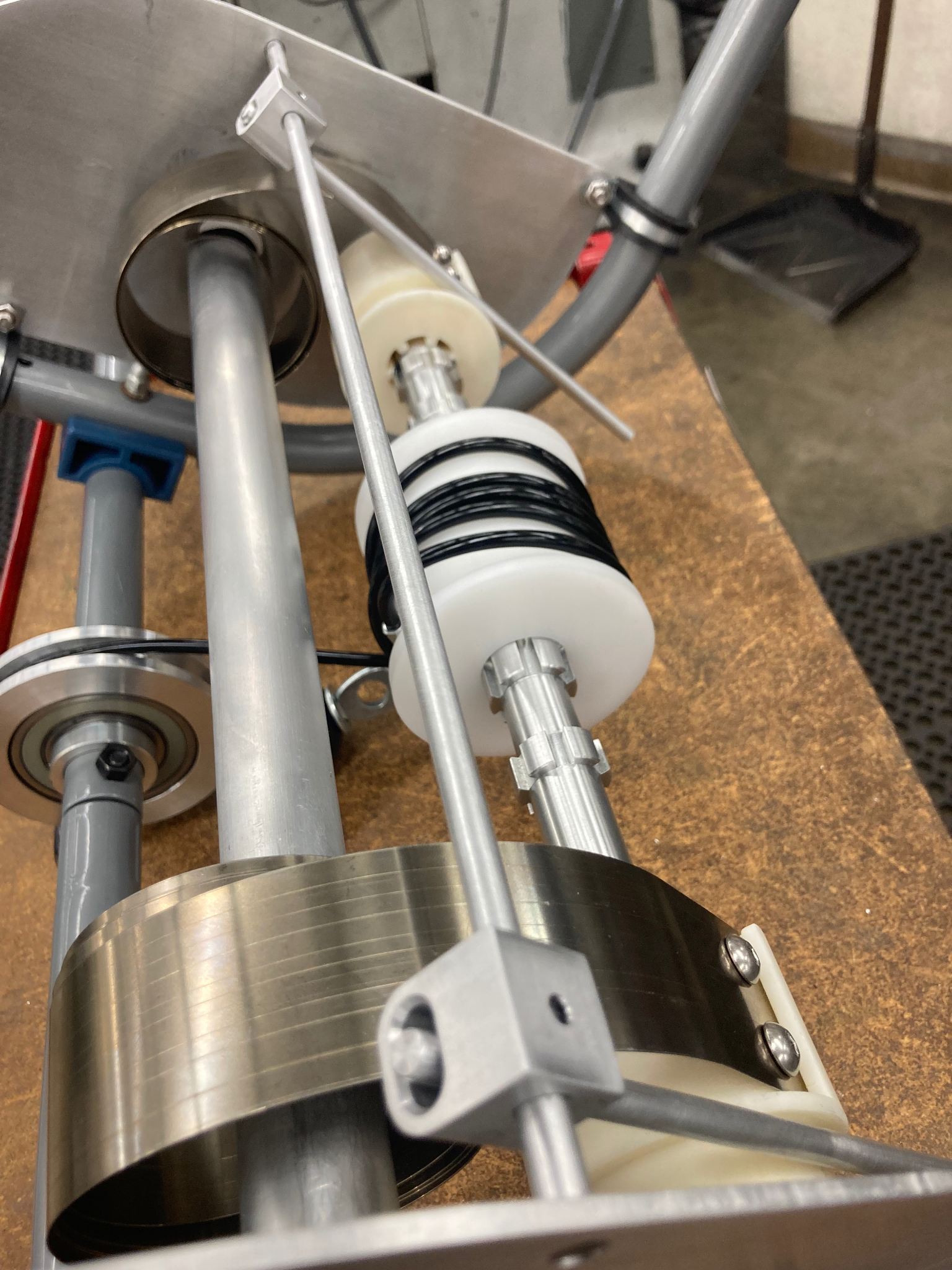
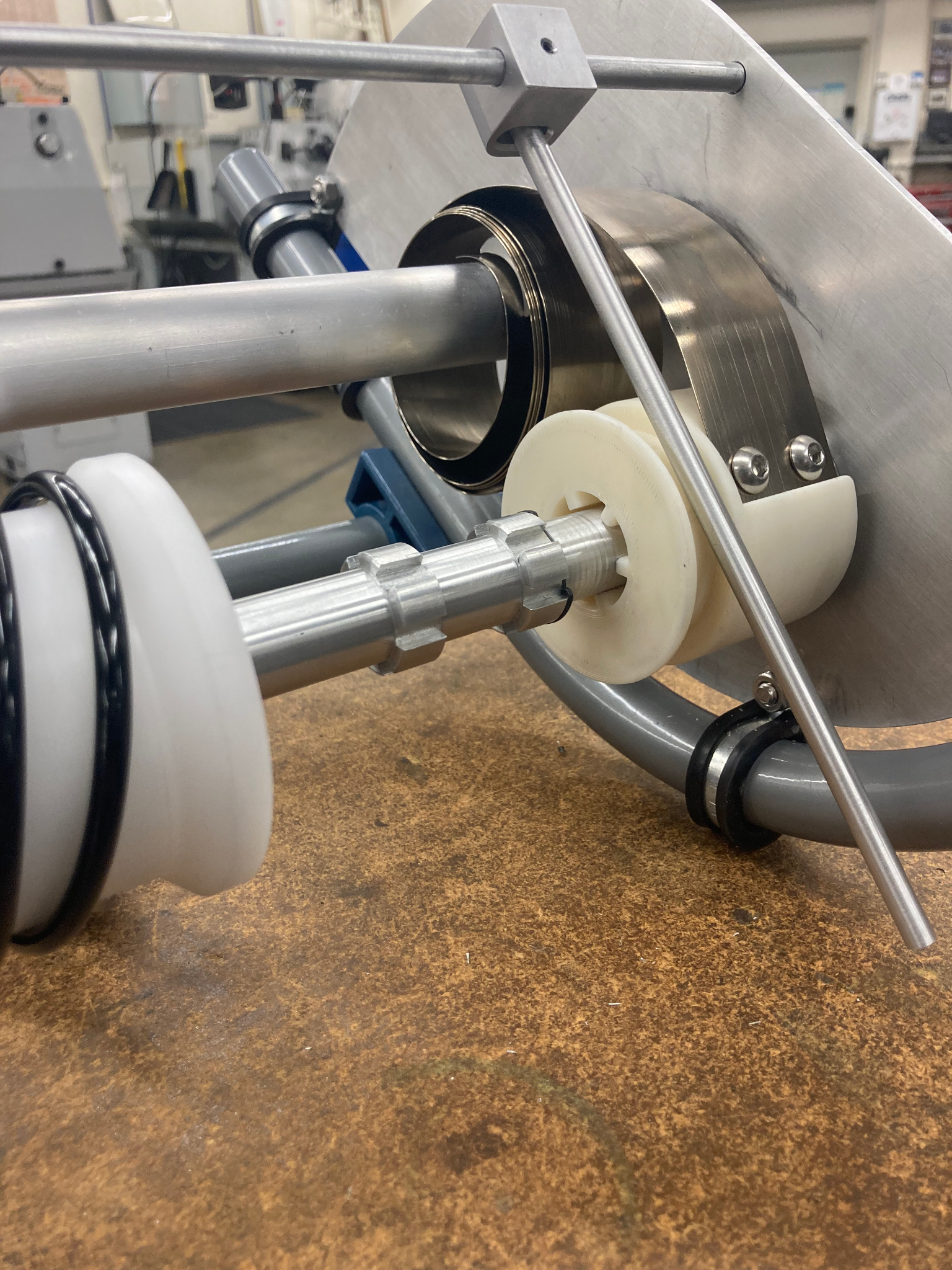
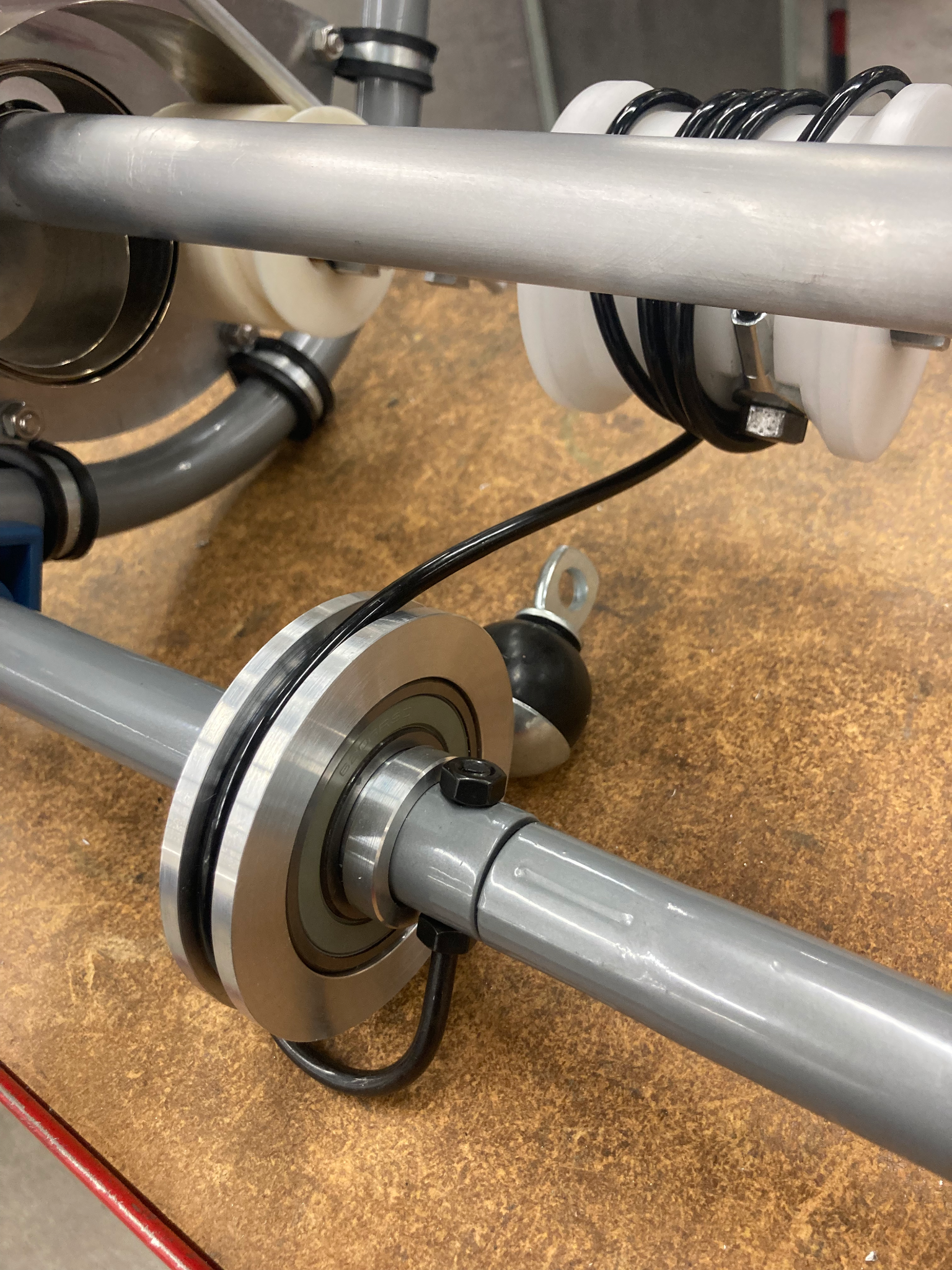
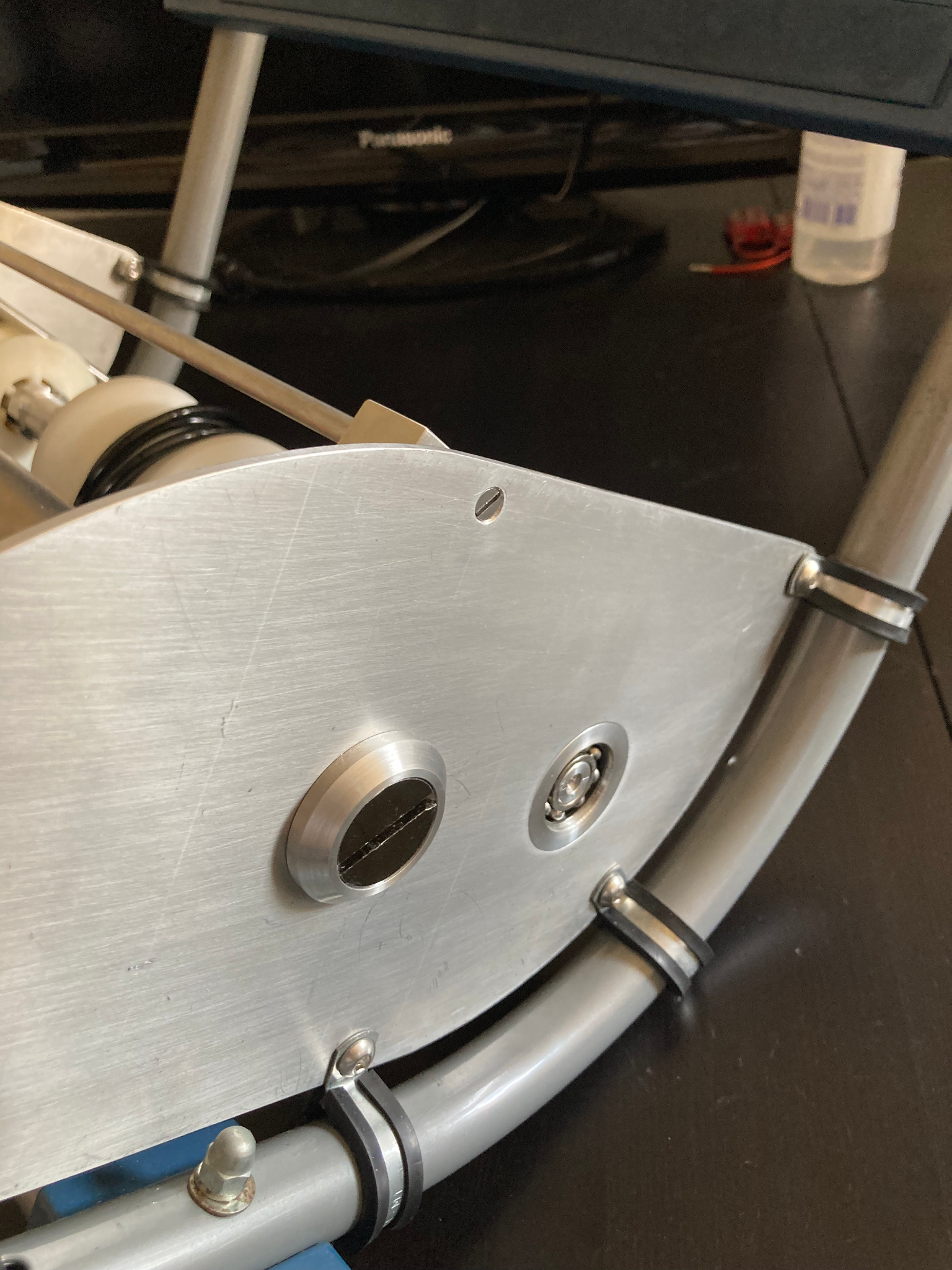
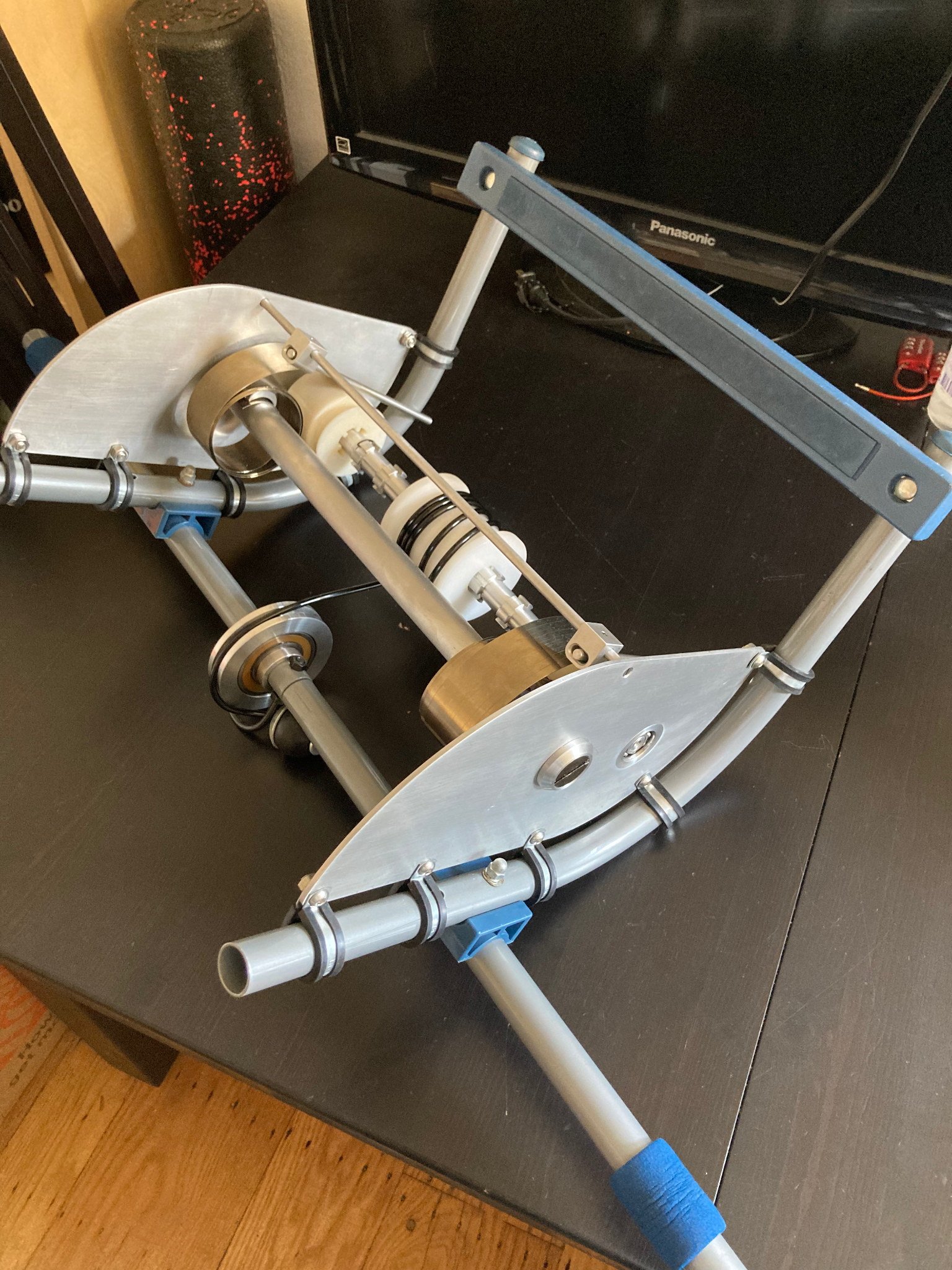
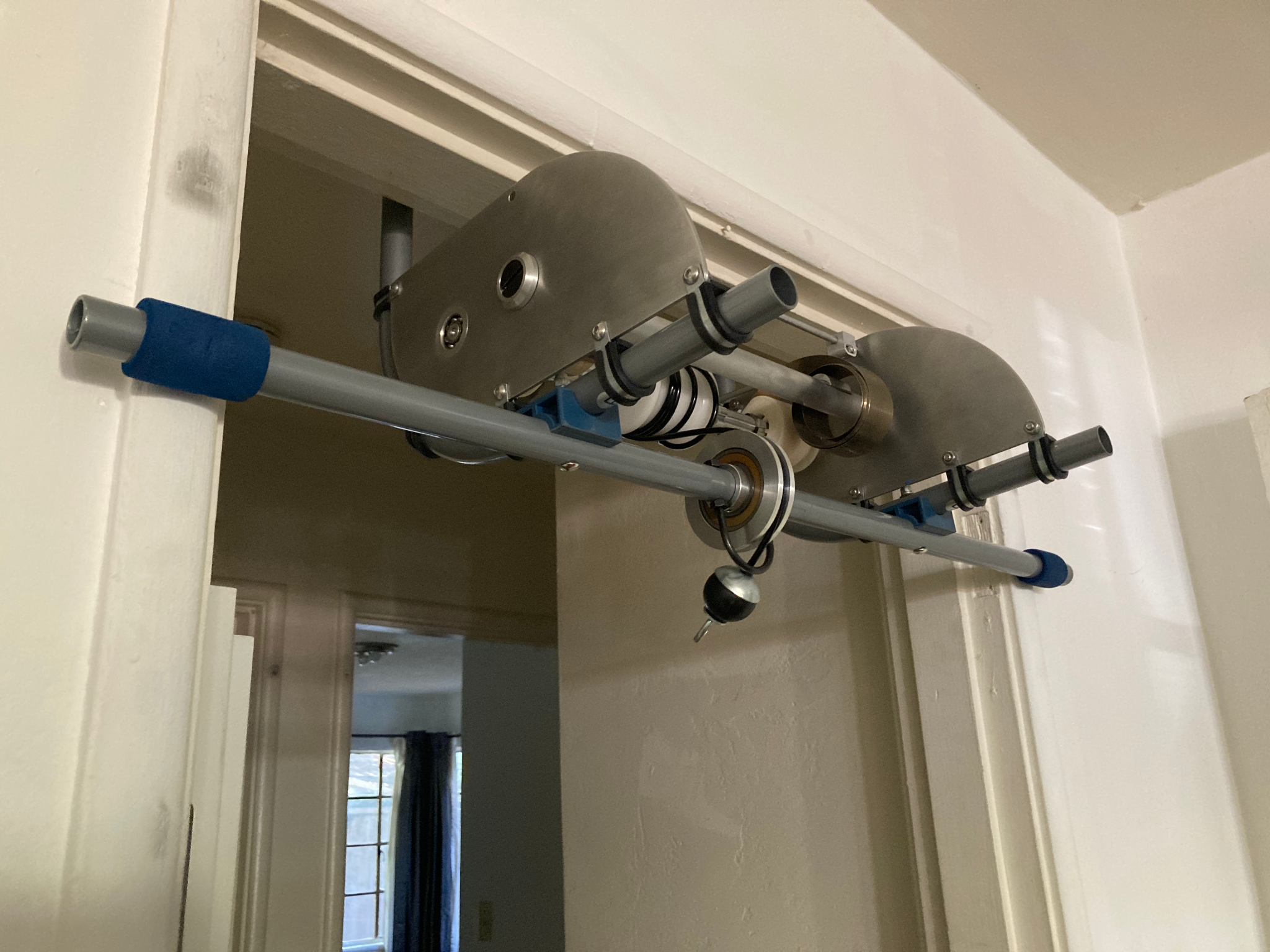
The cable was only able to extend about a foot before the springs could not stretch anymore but we believe we could have achieved a better range of motion if we used a different orientation where the spring is around the shaft. The internal-toothed drums worked very well to engage and disengage the springs onto the shaft. In the pictures, you could see thin aluminum rods used as switches to pull or push the drums back and forth, which for a future iteration would stick out of a casing, being much friendlier to the user.